Die richtige Dosis
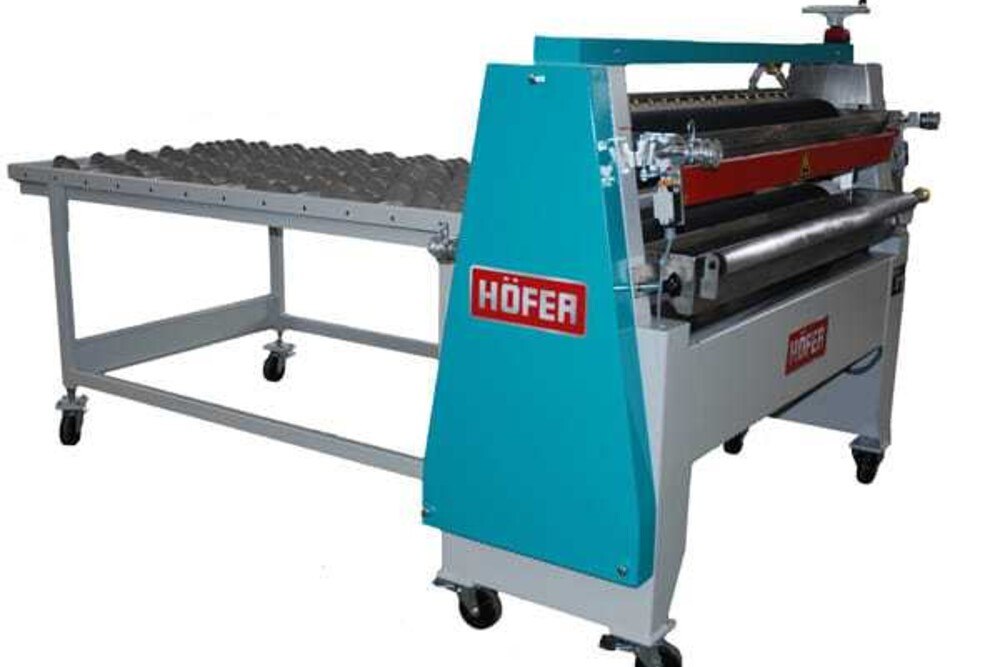
Die Tischlerei wird seit jeher mit Hobel und Leim in Zusammenhang gebracht, auch wenn sich im Laufe der Zeit unter anderem die Klebemittel an neue Aufgabenstellungen angepasst haben. Mittlerweile sind häufig neben einem herkömmlichen Weißleim auch andere Systeme, wie beispielsweise PUR-Varianten, üblich. Für einen rationellen Einsatz im Zusammenspiel mit der geforderten Produktivität sind damit oftmals Änderungen im Arbeitsablauf notwendig. Im Folgenden auszugsweise einige grundlegende Konzept und Umsetzungslösungen.
Gestaltung der Klebefläche
In der Praxis finden neben der Überlappungsverbindung auch Schäftungen, Gehrung und Dübel, Schlitz und Zapfen, Keilzink- und stumpfe Verbindungen, sowie Punktklebungen bei Spanplatten Ihren Einsatz. Für kraftschlüssige Kombinationen mit hoher Festigkeit ist es zweckmäßig, möglichst große Klebflächen zu wählen, wobei die Breite wichtiger ist als die Länge.
Als wichtiger Bestimmungsfaktor für die Festigkeit gelten unteranderem die Holzfeuchte und die Oberflächenvorbehandlung. Erstere beeinflusst dabei die Benetzung, Härtung und die Bindungsfestigkeit der Klebstoffe. Liegt diese unter fünf Prozent, so wird das Lösemittel des Klebers zu schnell abgetrocknet. Dies führt zu einer Verringerung des Fließvermögens sowie der Benetzungsfähigkeit und bewirkt Quellspannungen bei einer späteren Klimatisierung der Fügeteile. Analog verursacht eine zu hohe Holzfeuchtigkeit von über 15 Prozent eine verminderte Benetzbarkeit durch wässrige Leime.Das Wasseraufnahmevermögen wird verkleinert und die Abbindegeschwindigkeit verzögert. Infolge des Lösungsmittelüberschusses prägt sich eine schaumige, wenig feste Klebefuge aus. Dies führt bei einer anschließenden Lagerung zu erheblichen Trocknungsspannungen, welche sich festigkeitsmindernd auswirken. In einem Holzfeuchtebereich von acht bis zwölf Prozent, werden die besten Festigkeiten mit geringen Klebefugenspannungen erreicht. Dabei ist auch auf die Luftfeuchtigkeit und eine ideale Raumtemperatur mit rund 19 Grad Celsius zu achten, sodass eine eventuelle Vorkonditionierung von Materialien aus dem Außenlager notwendig sein kann.
Vorbehandlung
Die Oberflächenvorbehandlung hat den allgemeinen Zweck die physikalisch-chemische Reaktionsfähigkeit durch Vergrößern oder Aktivieren zu erhöhen. Bei Holzoberflächen erfolgt dies mit einem spanenden Abtrag zur Entfernung von Verunreinigungen und Trennmitteln. Die Oberflächen werden dabei nicht vergrößert, da infolge des zellulären Aufbaues eine ausreichende Mikroporosität gegeben ist. Es ist jedoch beim Zuschnitt auf eventuelle Holzmerkmale, die Lage der Holzfasern und die Stellung der Jahresringe zu beachten, um ein Arbeiten des Werkstückes gering zu halten. Es gelten die althergebrachten Tischlerregeln mit „nur Kernholz an Kernholz und Splint an Splint“, wobei die rechten und linken Seiten abwechselnd (gestürzte Fuge) verleimt werden. Genauso sind Herzstücke zu entfernen und beim Aushobeln ist auf die Ausrissfreiheit und eine gerade Winkelkante zu achten.
Klebstoffe
Wie bereits eingangs erwähnt haben sich die Anforderungen an Klebstoffe für Holzteile in den letzten Jahren verändert, wodurch sich ein höheres Beanspruchungsfeld ergibt. So finden beispielsweise immer häufiger PUR-Systeme ihren Einsatz, da sie durch ihre aufschäumende Wirkung fehlertoleranter hinsichtlich der Oberflächenqualität sind. Genauso werden bei einer Holzfeuchte von 16 Prozent noch beste Resultate erzielt, da dies dem feuchteliebenden Klebstoffaufbau entgegenkommt. Auf der anderen Seite stehen dazu jedoch die prompte reaktive Haltung bei Luftkontakt, die äußerst schwierige Reinigung von Arbeitsmaterialien und nicht nur der hohe Einstandspreis. Darüber hinaus finden weitere Systeme ihre Verwendung, wobei immer die dafür wesentlichen Zeitangaben für die Verarbeitung sowie der Säuberungsaufwand zu bedenken sind.
Klebstoffauftrag
Dieser soll in unbedingt notwendiger Menge und gleichmäßig erfolgen, da ansonsten Schwindspannungen hervorgerufen und sich der Klebstoff abzeichnen kann. Die Auftragsmenge richtet sich nach der Oberflächenqualität, ihrer Rauigkeit, Saugfähigkeit und Ebenheit, der Art des Klebers, seiner Viskosität, dem Füllvermögen, dem Schwinden und der Auftragstechnik. Eine zu hohe Dosierung bewirkt ein Herausdrücken des Leimes beim Fügen der Teile. Analog wird mit einer zu kleinen Menge die offene Wartezeit reduziert sowie ein Wegschlagen ins Holz begünstigt und ein „Verhungern“ der Klebefuge verursacht. Grundsätzlich verursachen dicke Fugen, als auch bei zu geringer Auftragsmenge, eine mindere Festigkeit.Das Auftragen kann durch manuelle oder maschinelle Verfahren erfolgen. Zu der ersten Gruppe zählen Pinsel, Rolle, Spachtel, Spritzpistole und das Tauchverfahren. Genauso sind Kämme und Leimspritzen zum Aufstecken gebräuchlich, um ein effizienteres Arbeiten zu ermöglichen. Eine Besonderheit stellen die Leimauftraggeräte dar, welche aus einem Druckkessel mit einem Schlauch, einer Leimpistole und entsprechenden Spritzdüsenaufsätzen bestehen. Dabei wird der Leim im Kessel mit bis zu fünf Bar Luft beaufschlagt und so eine schnelle, dosierte Applikation ermöglicht. Das System steht dauerhaft unter Druck und lediglich die Spritzdüsen unterliegen einer einfachen Reinigung. Eine Automatisierung für spezielle Anwendungsfälle durch eine pneumatische Steuerung ist ebenso möglich, wie ein Umbau für PUR-Leime. Dabei wird die Auftragsdüse nach der Verwendung entsorgt.
Maschinelle Verfahren
Gegenüber den händischen Verfahren werden durch maschinelle Systemen eine größere Genauigkeit, Gleichmäßigkeit und vor allem eine wesentlich höhere Geschwindigkeit erreicht. Die Umsetzung erfolgt dabei meist mit Walzenauftrag, Gießen sowie Spritzen.
Das erste Verfahren wird für Breit- und Schmalflächen sowie geringfügig verformte Oberflächen (Softforming) eingesetzt. Zum Einsatz kommen je nach Ausführung Klebstoffauftragsmaschinen mit zwei oder vier Walzen. Die erste Variante findet sich oft in Handwerksbetrieben wieder, wobei das jeweilige Leimbecken als Vorratsbehälter sowie als Rakel dient. Systeme mit vier Walzen erreichen eine höhere Präzision und finden sich oft im industriellen Umfeld in Kombination mit automatischen Leimmischanlagen wieder. Dabei erfolgt eine kontinuierliche und gleichmäßige Zufuhr des Klebstoffes in den Spalt zwischen Auftrags- und Dosierwalze, wodurch eine homogene Leimschicht ausgebildet wird. Je nach Konsistenz der Flotte kommen unterschiedliche Umdrehungsgeschwindigkeiten der Walzen zum Einsatz, die Dosierwalze wird dabei mit einer höheren Drehzahl betrieben und wirkt damit als Rakel. Die Teile sind mit verschleißfestem und chemikalienresistentem Gummi beschichtet, womit Anpassungen an die Oberflächenunebenheiten möglich sind. Abhängig von der Viskosität können verschiedenartige Profilierungen gewählt werden, um den Klebstoff gezielt in verschiedene Zonen abzulegen und eine Druckentlastung der Walzen zu gewährleisten. Um eine Veränderung der Zähigkeit des Klebemittels, durch die auftretende Reibungswärme zwischen den Walzen, zu kompensieren, kommen oftmals gekühlte Ausführungen zum Einsatz. Für die Reinigung wird entweder auf eine rasche Demontagemöglichkeit geachtet oder auf Flachstrahldüsen in Verbindung mit Warmwasser und einer Abwasserfilteranlage gesetzt.
Ein weiteres Verfahren ist das Gießen, wobei der einseitige Auftrag kontaktlos erfolgt und damit ein Umstellen bei wechselnder Stärke der Bauteile entfällt. Dadurch sind sehr hohe Auftragsgeschwindigkeiten möglich, auch wenn bei welligen Materialien meist Nachbesserungen notwendig sind.
Ferner zählt der Spritzauftrag zu den gängigen Möglichkeiten, vor allem wenn ein direkter Kontakt vermieden werden soll. Dies tritt beispielsweise bei der überstehenden Kante bei Postformingmaterialien, der Applikation von Zweikomponenten-Klebstoffen mit sehr kurzen Topfzeiten oder bei reaktiven Schmelzklebern auf. Der Betrieb der Spritzpistolen erfolgt dabei mit als auch ohne Luftzufuhr, wobei ein definierter und konstanter Sprühkegel erforderlich ist, der durch die Form und Durchmesser der Düsen erreicht wird. Damit können die Sprühdüsen für einen gleichmäßigen wie zielgerichteten Auftrag, angeordnet werden.
Eine wichtige Voraussetzung dafür ist eine entsprechend niedrige Viskosität des Klebstoffs und eine Vermeidung von Gel-Teilchen mit der Verwendung von Reinigungsfiltern. Besonders wichtig die Reinigung nach jeder Unterbrechung, da ansonsten die Düsen durch eingetrocknetes Klebemittel verschlossen sind.
Text: Jürgen Fragner