Eine Brücke zwischen traditioneller und digitaler Welt
Radlader sind aus dem Baustellenalltag nicht wegzudenken – nur wenige Maschinen stehen so sinnbildlich für Effizienz und Vielseitigkeit auf der Baustelle. Der technologische Fortschritt macht vor den Kraftpaketen keinen Halt, gerade in den vergangenen Jahren hat eine Welle an Innovationen die Branche erfasst.
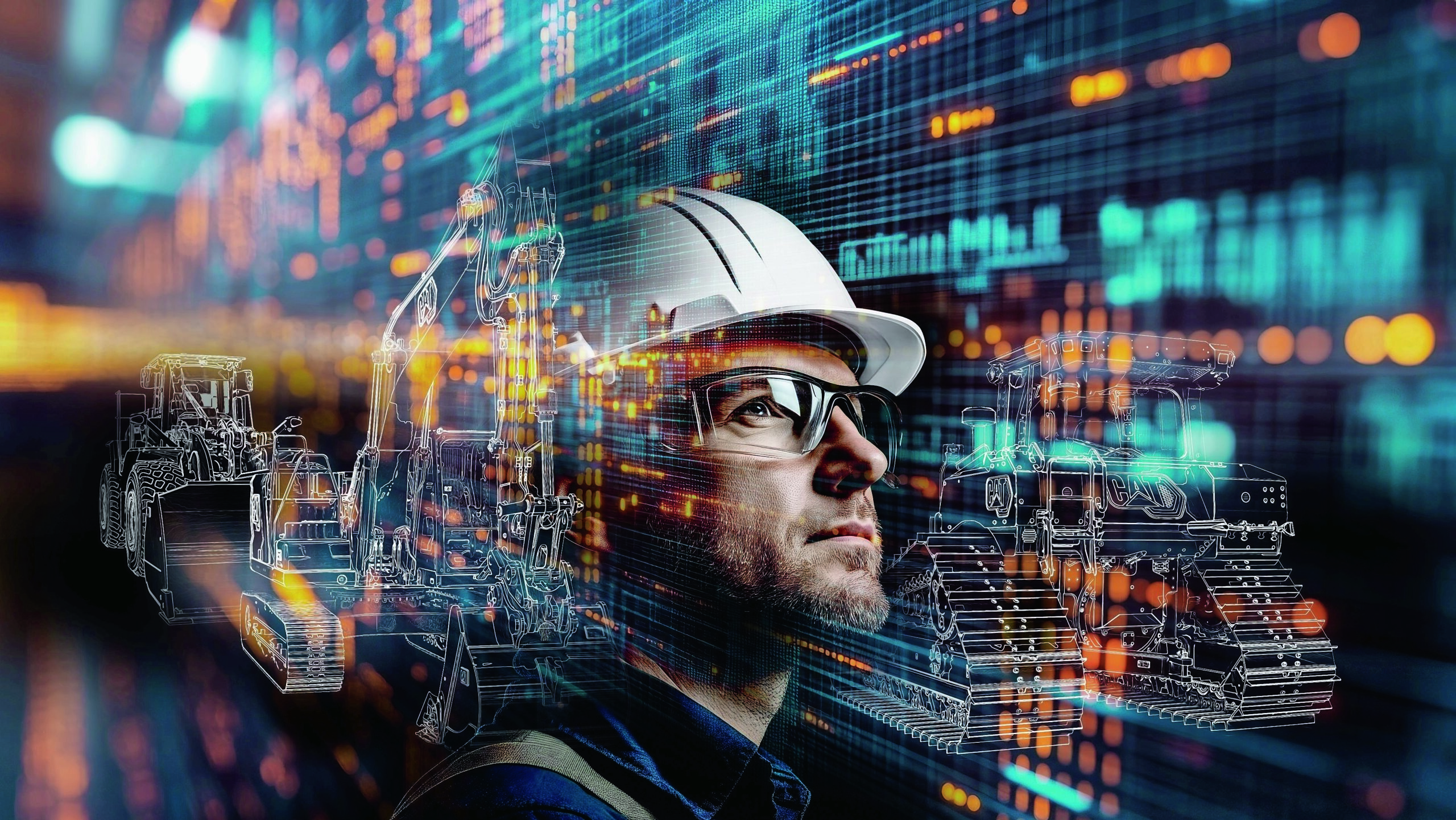
Digitalisierung, Automatisierung, Autonomisierung und Elektrifizierung sind dabei vier Trends, die in der Welt der Radlader nicht nur Schlagworte, sondern reale Transformationsprozesse sind. Die Hersteller gehen hier zwar oft ähnlich Wege, dennoch unterscheiden sich die einzelnen Ansätze im Detail. Während manche das Augenmerk eher in Richtung Elektrifizierung setzen, fokussieren sich andere auf die Integration autonomer Systeme oder digitaler Plattformen. Die Digitalisierung von Radladern beginnt beispielsweise längst nicht mehr beim klassischen Flottenmanagement. Vielmehr rückt die umfassende Maschinenvernetzung verstärkt in den Mittelpunkt. Ziel ist dabei, Arbeitsprozesse zu optimieren, Stillstandzeiten zu minimieren und durch präzise Datenanalyse wirtschaftlicher zu arbeiten.
„In einer Welt, in der die Erwartungen an Effizienz, Transparenz und Service steigen, geht es darum, die Brücke zwischen traditionellem Geschäft und digitalen Lösungen zu schlagen Frederik Terschluse, Leiter Digitale Produkte & Services bei Zeppelin
„In einer zunehmend vernetzten Welt, in der die Erwartungen an Effizienz, Transparenz und Service immer weiter steigen, geht es darum, die Brücke zwischen traditionellem Geschäft und digitalen Lösungen zu schlagen“, erklärt Frederik Terschluse, Leiter Digitale Produkte & Services bei Zeppelin. Dementsprechend zentral sei die Rolle, die das digitale Eco-System von Caterpillar hierbei spiele. So soll die Lösung Nutzer*innen dabei unterstützen, „das Maximum aus den Arbeitsgeräten herauszuholen“ und die tägliche Arbeit für Kund*innen „so einfach wie möglich zu gestalten.“ Der Hersteller will Kund*innen und deren Maschinen daher noch besser mit den digitalen Plattformen von Caterpillar verbinden und sie „mit dem notwendigen Rüstzeug rund um Baumaschinen“ ausstatten.
Schneller zum Ersatzteil
Das System umfasst dem Fachmann zufolge fünf Säulen, die von Caterpillar und somit direkt aus der Hand des Herstellers kommen. Letzter Baustein, der im vergangenen Jahr erst ergänzt wurde, ist „parts.cat.com“, eine Plattform für die Online-Bestellung von Ersatzteilen. Darüber soll die Suche nach rund 1,4 Millionen verfügbaren Ersatzteilen sowie der Bestellprozess deutlich einfacher werden, verspricht das Unternehmen. So wurde beispielsweise die Suche nach Ersatzteilen optimiert, indem diese nun auf die Seriennummer der Maschine bezogen werden kann. Über eine Kompatibilitätsprüfung wird dabei sichergestellt, dass das benötigte Ersatzteil auch exakt zur Maschine passt. Ein weiterer Teil des digitalen Eco-Systems ist die mobile Lösung des Shops für Ersatzteile. Dabei handelt es sich nicht um eine eigene beziehungsweise separate App, sondern um ein und dieselbe Anwendung, die jedoch auch über den Browser am Smartphone oder Tablet aufgerufen werden kann. Alle Funktionen stehen dadurch auch auf mobilen Endgeräten zur Verfügung.
Service und Information
Der dritte Baustein des digitalen Eco-Systems betrifft das SIS, das Service- und Informationssystem von Caterpillar, welches einerseits als Desktop-Anwendung verfügbar ist und andererseits auch als „SIS 2 Go“ mobil angeboten wird. Die Lösung dient quasi als Nachschlagewerk und enthält umfassende Informationen sowie Anleitungen rund um die Wartung und Reparatur von Baumaschinen. Dazu gehört auch der Zugriff auf eine Vielzahl von technischen Dokumentationen, wie Servicehandbücher, Informationen zu Ersatzteilen, Diagnosetools zur Unterstützung bei der Fehlerdiagnose sowie Schaltpläne für verschiedene Maschinenmodelle oder Bauteilzeichnungen. Damit werde es zu einem „unverzichtbaren Werkzeug für Techniker, die an und mit Cat Maschinen arbeiten“, weil sie darüber schnell und effizient die notwendigen Informationen erhalten können, um Wartungs- und Reparaturarbeiten durchzuführen. Mit der mobilen Anwendung stehen all diese Informationen auch auf dem Smartphone und Tablet zur Verfügung. Zudem können die technischen Dokumentationen lokal gespeichert werden und sind dadurch auch offline abrufbar.
Mit „VisionLink“ existiert der vierte Baustein des digitalen Eco-Systems bereits seit 2009. Die Plattform zum Flottenmanagement wurde seit damals weiterentwickelt und bietet eine Vielzahl von Funktionen. Größter Vorteil sei dabei die Übersicht aller Baugeräte in einem System. Durch die Übermittlung der Gerätedaten wie Standort, Betriebsstunde, Kraftstoff und Leerlauf können Bauunternehmer individuell agieren. Erzeugt die Maschine einen ausfallkritischen Fehler, wird eine Warnung via Push-Benachrichtigung direkt auf das Smartphone der Nutzer*innen geschickt. Wartungsarbeiten können damit dokumentiert und abgeschlossen werden. Die Lösung biete vielen Bauunternehmern eine Möglichkeit, analoge Prozesse zur Fuhrparkverwaltung zu digitalisieren.
QR-Codes im Einsatz
Das fünfte und letzte Element im digitalen Eco-System des Unternehmens bilden QR-Codes, die seit 2022 an allen Neumaschinen im Inneren der Kabine angebracht sind. Diese enthalten die Seriennummer der Maschine. Wird der QR-Code gescannt, wird die mobile Anwendung vom parts.cat.com geöffnet und alle Ersatzteile der Maschine aufgelistet, die mit dem QR-Code verknüpft ist.
Darüber können Kunden die passenden Ersatzteile suchen oder sie können technische Dokumentationen zur Maschine ansehen. „An dieser Stelle erfolgt der Übergang vom sprichwörtlich gelben Eisen in die digitale Welt von Caterpillar, damit Kunden auf die Caterpillar Lösungen zugreifen können.“
Autonom arbeitende Maschinen
Mit der Digitalisierung der Radlader geht nicht selten auch eine stärkere Automatisierung der Maschinen einher, die bei Assistenzsystemen beginnt und beim teilautonomen Betrieb endet. Moderne Radlader unterstützen ihre Bediener*innen dabei auf vielfache Weise – vom automatisierten Wiegen bis zur automatischen Rückführung der Schaufel in Lade- oder Entladeposition. Auf der Fachmesse „Bauma“ präsentierte Liebherr beispielsweise jüngst das autonome System „Autonomous Operations“. Die autonome Lösung, die sich in einem fortgeschrittenen Entwicklungsstadium befindet, ermöglicht einen komplett fahrerlosen Betrieb und eigne sich dem Hersteller zufolge vor allem bei monotonen Standardtätigkeiten sowie bei Einsätzen in Gefahrenbereichen.
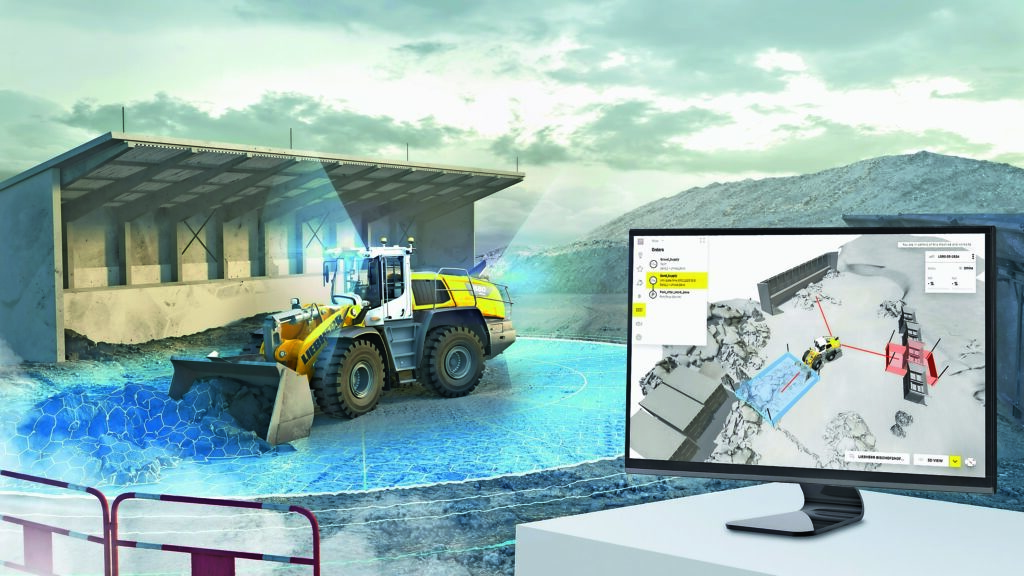
Die Lösung definiere Effizienz und Sicherheit im Radlader-Einsatz neu und ermögliche zukünftig einen vollautonomen Betrieb, wie der Hersteller verspricht. So könnten monotone Standardtätigkeiten, wie etwa das wiederkehrende Beschicken von Aufgabetrichtern oder das Verladen von A nach B ohne Fahrer, komplett eigenständig ausgeführt werden. Dies wirke vor allem der Schwierigkeit entgegen, Mitarbeitende für monotone Routinetätigkeiten zu finden, betont der Hersteller. In Folge können sich Arbeitskräfte abwechslungsreicheren Aufgaben zuwenden, wodurch sich die Arbeitszeit effektiver gestalten lässt. „Gleichzeitig kann damit Raum geschaffen werden, um sich komplexeren Tätigkeiten zu widmen, die menschliche Expertise erfordern“, erklärt Manuel Bös, seines Zeichens Abteilungsleiter für Aufstrebende Technologien im Liebherr-Werk Bischofshofen. Zusätzlich können herausfordernde Arbeiten, etwa in den Gefahrenbereichen eines Steinbruchs, vom autonomen System ausgeführt werden, ohne dabei Mitarbeitende den Risiken auszusetzen, so der Experte.
Die Einsätze des autonomen Radladers werden dabei mit der von Liebherr entwickelten Webapplikation „Autonomous Job Planner“ geplant. „Man benötigt keine besonderen IT-Kenntnisse, um den Radlader-Einsatz zu starten. Das System ist sehr intuitiv, benutzerfreundlich und benötigt nur wenige Inputs für den Arbeitsauftrag“, erläutert Bös. Die Maschine nehme dabei ihre Umgebung, Haufwerke und Hindernisse mittels 3D-Umfeldsensorik wahr, weshalb keine Drohnen oder separate Vermessungstechnik mehr nötig seien. Auf den Daten der Sensorik basierend werde dann der Arbeitszyklus geplant.
Anschließend führe das autonome System den Auftrag eigenständig aus, passe sich dabei der veränderlichen Umgebung vollautomatisch an und benötige zudem keinen GPS-Empfang, womit der Einsatz in Hallen, Untertage, an hohen Abbruchwänden oder unter der Vegetation möglich werde. „In diesen Einsätzen kommen heute übliche GPS-basierte Systeme an ihre Grenzen, während Liebherr Autonomous Operations überall einsatzfähig ist – von einer engen Industriehalle bis zum offenen Steinbruch“, unterstreicht Bös. Darüber hinaus könne der autonom fahrende Radlader rund um die Uhr selbstständig Arbeiten ausführen und ermögliche damit einen zeitunabhängigen und konstanten Materialumschlag.
Betriebskosten senken
Das autonome System ermögliche den Betrieb der Maschine von Beginn an mit gleichbleibender Performance und Effizienz über die gesamte Einsatzdauer und unabhängig von der Tageszeit. „Aufgrund der konstanten Arbeitsleistung des autonomen Radladers lassen sich sämtliche Prozesse einfacher planen und effizienter gestalten“, so Bös. „Der von der Software gesteuerte autonome Radlader arbeitet besonders maschinenschonend, wodurch sich vor allem der Komponenten- und Reifenverschleiß und der Treibstoffverbrauch nachhaltig verringern. Das senkt die laufenden Betriebskosten. Zudem können Betreiber nahtlos zwischen dem klassischen, manuellen Kabinenbetrieb oder dem vollautonomen Betrieb umschalten und so die Maschinenauslastung maximieren.“
Nahtlose Maschinensteuerung
Auch Komatsu setzt verstärkt auf digitale Lösungen, erst kürzlich gab der Hersteller bekannt, dass das hauseigene System „Smart Construction Remote“ künftig zur Standardausrüstung für Maschinen mit Steuerungssystemen von Komatsu gehören wird. Zur Lösung gehören die intelligente Maschinensteuerung (iMC) und das „Smart Construction 3D Anzeigesystem“. Smart Construction Remote ist eine cloudbasierte Lösung, mit der Nutzer aus der Ferne sowohl auf Maschinen von Komatsu als auch auf Maschinen anderer Hersteller zugreifen können. Damit können Probleme schneller und effizienter gelöst werden, was Stillstand-zeiten reduziert und die Leistung steigert, erklärt Stefan Kuhn, einer der Geschäftsführer der Kuhn Holding. Zudem könnten mit der Lösung beispielsweise auch Konstruktionsdateien an die Maschinen gesendet werden, selbst wenn diese gerade ausgeschaltet sind. Dadurch werde für eine nahtlose Zusammenarbeit zwischen Büro und Einsatzort.
Durch den Fernzugriff auf die Maschinen sind weniger Fahrten zur Baustelle erforderlich.
Durch den Fernzugriff auf die Maschinen sind unter anderem weniger Fahrten zur Baustelle erforderlich, sodass der Kraftstoffverbrauch und die CO2-Emissionen sinken. Diese Vorteile kommen besonders bei Unternehmen zum Tragen, die mehrere Baustellen gleichzeitig leiten. Die Möglichkeit, Smart Construction Remote mit Maschinen verschiedener Hersteller einzusetzen, unterstreiche dabei auch die kontinuierlichen Bemühungen von Komatsu, die Maschinenkommunikation über bisherige Grenzen hinweg zu ermöglichen, die digitale Transformation zu vereinfachen, Innovationen zu fördern und die Einführung intelligenter Technologien zu beschleunigen. Mit Smart Construction Remote als Standardausrüstung sorge Komatsu für eine stärkere Verknüpfung der Maschinen einer Flotte und unterstütze Kund*innen in ihrer Entwicklung hin zu digitalisierten Arbeitsabläufen, verweist der Hersteller. Komatsu legt dementsprechend großen Wert darauf Technologien zu entwickeln, welche die Nachhaltigkeit, Effizienz und Sicherheit für die gesamte Industrie fördern.
Produktivität steigern
Digitalisierung spielt auch bei den Radladern von Volvo CE eine wichtige Rolle. Das Unternehmen führte unlängst, in einer ersten Welle, fünf überarbeitete Modelle einer neuen Radlader-Generation ein. Im Fokus der Entwicklung standen dabei dem Hersteller zufolge maximale Produktivität und Effizienz bei einer Vielzahl von Anwendungen, darunter Materialumschlag, Einsätze im Steinbruch, in der Holzindustrie, Erdarbeiten oder Aufgaben rund um Abfall und Recycling.
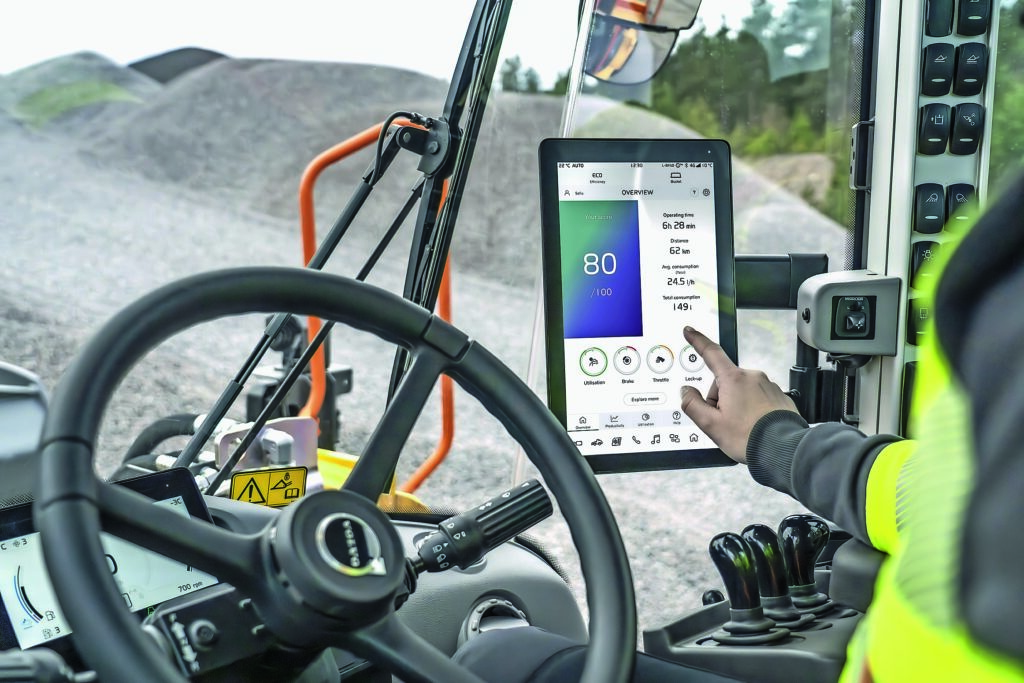
Bei den ersten fünf überarbeiteten Maschinen handelt es sich um die Modelle „L150“, „L180“, „L200 High Lift“, „L220“ und „L260“. „Unsere neue Generation von Radladern stellt hinsichtlich Technologie und Design einen bedeutenden Sprung nach vorn dar“, unterstreicht Erich Kribs, Produktmanager bei Volvo CE. „Mit diesen Modellen erhöhen wir nicht nur Produktivität und den Komfort, sondern setzen auch neue Maßstäbe für Innovation und Effizienz in der Branche. Diese jüngste Markteinführung ist Teil unseres bisher ehrgeizigsten Jahres, in dem wir weitere bahnbrechende Produkte für die sich wandelnden Bedürfnisse unserer Kunden auf den Markt bringen.“
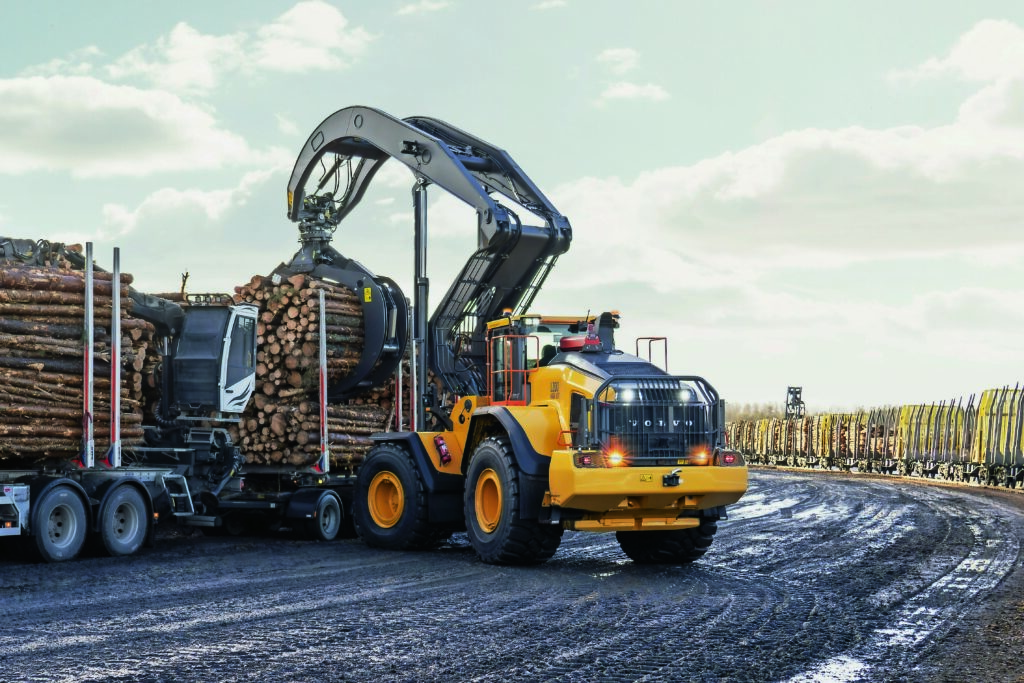
Die jüngste Generation der „Load-Sensing-Hydraulik“ optimiere beispielsweise die Reaktionsfähigkeit der Anbaugeräte, verbessere die Hub- und Senkgeschwindigkeit des Hubgerüsts und ermögliche dadurch kürzere Zykluszeiten. Die Nivellierfunktion bringt die Schaufel zudem automatisch aus der Kipp- und Transportposition zurück, während die intelligente Auto Bucket Fill-Funktion für eine optimale, gleichmäßige Befüllung sorge. Außerdem werde mit der aktualisierten „Smart Control“ beim Starten der Maschine standardmäßig ein kraftstoffsparender Motormodus aktiviert.
Nachhaltiger arbeiten
Die Digitalisierung trägt auch dem Trend zur Nachhaltigkeit Rechnung, liegt doch eine Herausforderung der Baubranche darin, Leistung, Reichweite und Ladeinfrastruktur der elektrischen Baumaschinen in Einklang zu bringen. Ein Segment, in dem etwa Wacker Neuson Akzente setzen will. Zur Bauma wurde der elektrisch angetriebene Radlader 5065e gezeigt, der mit einer 96 Volt Lithium-Ionen Batterie ausgestattet, eine Laufzeit bis zu vier Stunden ohne Zwischenladung erreichen kann. Unabhängig von der E-Technologie biete der Lader zudem kompakte Abmessungen und liefere optimale Leistungswerte im Stapel- und Schaufelbetrieb. Mit einer Stapelnutzlast von 1.750 Kilogramm steht der Radlader seinem Diesel-Pendant in nichts nach, wie der Hersteller betont. Kund*innen haben dabei die Wahl zwischen zwei verschieden Batteriegrößen: 28,8 kWh (Serie) und 37,5 kWh (Option).
Die Verschmelzung von Digitalisierung, Automatisierung und Elektrifizierung wird das Bauwesen transformieren. Radlader werden in Zukunft Teil einer durchgängigen, datengetriebenen Prozesskette sein. Die Verbindung mit BIM, Cloud-Plattformen und KI-Systemen wird Bauprozesse transparenter, planbarer und effizienter machen. Die Transformation ist in vollem Gange – und sie betrifft nicht nur Maschinen, sondern ganze Arbeitsprozesse. Unternehmen wie Ascendum, Kuhn, Liebherr, Wacker Neuson und Zeppelin geben mit innovativen Produkten und Systemlösungen die Richtung vor, gleichzeitig treiben Firmen wie Bobcat, Develon, Huppenkothen, Kubota oder auch Yanmar den Wettbewerb weiter an. Für Bauunternehmen ergeben sich daraus völlig neue Perspektiven, etwa geringere Betriebskosten, bessere Planbarkeit, schnellere Umsetzung – und ein zukunftssicheres Maschinenportfolio.
www.liebherr.com
www.zeppelin-cat.at
www.ascendum.at
www.kuhn.at
www.wacker-neuson.at
www.bobcat.com
eu.develon-ce.com
www.huppenkothen.com
www.kubota-eu.com
www.yanmar.com