Schwergewichte
Auch hierzulande stehen einige gewaltige Bagger im Einsatz. Unter der Haube findet sich Hightech vom Feinsten.
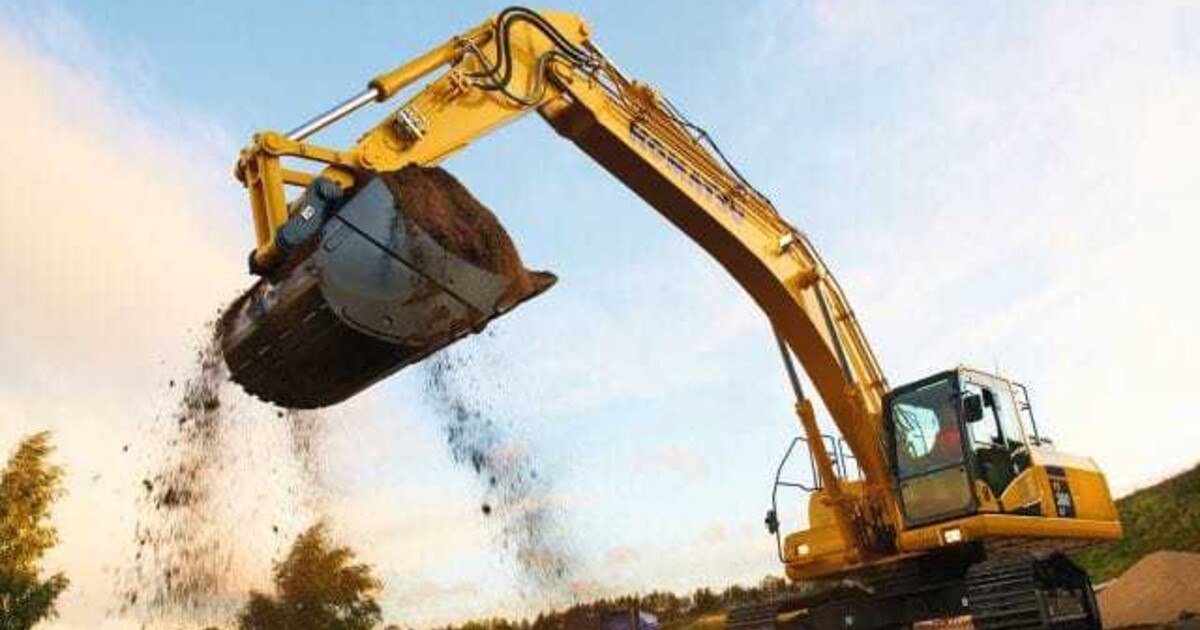
-
© Liebherr -
© Caterpillar -
© Kuhn -
© Kuhn
Mit einem Einsatzgewicht von gewaltigen 810 Tonnen geht der größte Tieflöffel-Mining-Bagger der Welt an die Arbeit. Der Liebherr R 9800 bringt das Gewicht von rund 32 Baggern der 25-Tonnen-Klasse, den Standardmaschinen auf heimischen Baustellen, auf die Waage. Mit seiner Löffelkapazität von 42 Kubikmetern könnte der Bagger eine hierzulande übliche Maschine im wahrsten Sinn des Wortes locker auf die Schaufel nehmen.
Das Megagerät ist in Europa allerdings nur auf der Bauma zu sehen – als ein vielbestaunter Anziehungspunkt des Liebherr-Standes. Zum Einsatz gelangen die Riesenmaschinen aus Deutschland vorwiegend in australischen und südamerikanischen Minen.
Die in Österreich genützten Bagger sind um einige Nummern kleiner. Aber eine paar große Brocken arbeiten auch hierzulande. Liebherr selbst hat in Österreicher bereits mehrere R 984 verkauft. Diese Maschinen bringen immerhin noch Einsatzgewichte von 125 Tonnen auf die Waage. Mit einem Löffelinhalt von sieben Kubikmetern und einem 504 kW / 685 PS starkem Motor können sie schon einiges bewegen.
Maschinen dieser Kategorie hat auch Komatsu in Österreich verkauft, wie Herbert Kreiseder, Verkaufsleiter bei Kuhn in Salzburg, erzählt. Am steirischen Erzberg steht seit dem Vorjahr eine Komatsu PC 1250 im Einsatz. Diese Maschine hat wie der Bagger von Liebherr ein Einsatzgewicht von 125 Tonnen und einen Löffelinhalt von sieben Kubikmetern. Sie wird beim Abbau von Eisenerz eingesetzt. Komatsu ist mit Großmaschinen auf dem Erzberg überhaupt stark präsent.
Neben dem Bagger stehen in diesem steirischen Tagbau noch vier große Radlader und zehn Muldenkipper – die größten in Mitteleuropa – im Einsatz.
Der größte Baggerhersteller
Häufiger als Bagger mit mehr als 100 Tonnen sind hierzulande Maschinen mit Einsatzgewichten in der 70- und der 80-Tonnen-Klasse im Einsatz. Komatsu hat im Vorjahr die Modelle PC 700 sowie PC 800 an Steinbrüche verkauft, wie Kuhn-Mitarbeiter Kreiseder erzählt. Im Steinbruch des Basaltwerkes Pauliberg im Burgenland etwa wird ein PC 700 für Ladearbeiten eingesetzt. Mit bis zu 5,5 Kubikmeter Material pro Löffelfüllung lässt es sich mit diesem Komatsu dabei effizient arbeiten. Die japanische Marke soll – so der Verkaufsleiter – in diesem Marktsegment Spitzenreiter sein: „Komatsu ist der größte Baggerhersteller weltweit, wir sehen uns aber auch in Österreich bei den großen Maschinen als Marktleader“, sagt Kreiseder.
Die neuesten Geräte von Komatsu in dieser Klasse sind die „-10“-Bagger wie der PC360LC/NLC-10. Diese in den vergangenen Jahren schrittweise eingeführten Hydraulikbagger verfügen über die neueste Motortechnologie und entsprechen den Vorschriften der Abgasemissionsstufe IIIB / Tier 4i. Die Maschinen sind im Vergleich zu den Vorgängermodellen schwerer und bieten mehr Leistung bei weniger Dieselverbrauch, berichtet Kreiseder: „Unser 36-Tonnen-Hydraulikbagger liegt laut Comtrax bei gemischten Einsätzen bei einem Verbrauch von 22 Litern. Diese hervorragenden Werten bestätigen auch unsere Kunden.“
Als einen einzigartigen Vorzug der Komatsu-Bagger gegenüber dem Wettbewerb streicht Kreiseder die Technik zur Regeneration des Rußpartikelfilters hervor: „Bei uns ist kein Ausbrennvorgang erforderlich, somit gibt es keine außerplanmäßigen Stillstandzeiten, und das Gerät ist immer mit hundertprozentiger Leistung verfügbar.“
Der Verkaufsleiter von Kuhn behauptet, dass Komatsu damit das einfachste System am Markt biete und sich dieses mittlerweile auch bewährt habe: „2011 wurde diese Technologie erstmals bei Schubraupen eingesetzt. Es hat seither absolut keine Probleme gege-
ben.“
Motor denkt voraus
Bei Caterpillar ist die Baggergeneration E die derzeit jüngste Serie. Die Maschinen entsprechen ebenfalls der Stufe IIIB / Tier 4i, und auch sie bieten mehr Wirtschaftlichkeit als die Vorgängermodelle. „Die gesamte Antriebstechnik und ihr Zusammenspiel wurde bei diesen Maschinen optimiert“, erzählt Wolfgang Szigeti, Leiter Service und Technik bei Zeppelin Österreich. Die Elektronik, die über dutzende Sensoren verschiedenste Zustände der Maschine erfasst und analysiert, ermöglicht dem Motor quasi einen kleinen Blick in die Zukunft: „Sobald der Fahrer den Joystick bewegt, läuft die Kommunikation kreuz und quer durch die Maschine, der Motor weiß dadurch um Sekundenbruchteile früher, was auf ihn zukommt“, sagt Szigeti. Dadurch wird bei Lastanforderung nicht wie in der Vergangenheit zuerst die Drehzahl hinuntergedrückt und dann hochgefahren.
Der Motor kann sich auf die Mehrleistung vorbereiten, fährt dadurch immer im optimalen Drehzahlbereich und verbraucht weniger Treibstoff. Auf die Spitze getrieben wird diese Technologie beim Hybridbagger von Cat, meint Wolfgang Szigeti. Zeppelin hat kürzlich den ersten Bagger dieses Typs ausgeliefert. Die Reaktion des Kunden soll äußerst positiv sein.
Auch bei Liebherr weist man auf das optimale Zusammenspiel von Hydraulik und Elektronik als ein wesentliches Kennzeichen der neuen Maschinengeneration hin. „Einzelbewegungen und überlagerte Bewegungen werden damit besonders effizient ausgeführt“, erzählt Elisabeth Weitgasser, Leiterin des Vertriebs- und Servicemarketings in Bischofshofen. Sie fügt hinzu, dass die perfekte Abstimmung aller Komponenten dafür sorgt, dass der Energieaufwand während des Einsatzes möglichst niedrig gehalten wird und die Maschinen im Vergleich zur Vorgängergeneration um bis zu 20 Prozent verbesserte Energieeffizienz bieten.
„Die Technik basiert auf einem Positive-Control-Hydrauliksystem sowie einer speziellen Steuerungslogik. Zwei voneinander unabhängige hydraulische Kreise ermöglichen die sinnvolle Ansteuerung der Komponenten, insbesondere bei überlagerten Bewegungen“, erzählt Weitgasser. Der benötigte Volumenstrom wird dadurch ausreichend schnell und bei optimaler Energienutzung zur Verfügung gestellt.
Neben der Motorentechnik wurden bei der jüngsten Generation der großen Bagger auch viele Details verbessert. Liebherr präsentierte zuletzt auf der Bauma seine neuen Schwergewichte. Als Nachfolger des R 974 C wurde der 90 Tonnen schwere R 976 mit einer verschleißgeschützten 5,1-Kubikmeter-Klappschaufel vorgestellt. Das 60-Tonnen-Gerät R 960 SME ersetzt die Super-Mass-Excavation-Variante des R 954 C.
Schwerer Bagger mit Touch-Display
Neben der serienmäßigen Rückfahrkamera bieten die Novitäten etwa auch verschiedene Schutzvorrichtungsoptionen für Einsätze im Steinbruch, wie zum Beispiel den Steinschlagschutz (FOPS und FGPS), den Kolbenstangenschutz für die Zylinder sowie einen Schutz für Schmierleitungen und das Drehwerk. In der verbesserten Kabine befindet sich ein spezielles Liebherr-Touch-Display. Es ermöglicht intuitive Bedienung von Betriebsfunktionen wie Arbeitsmodi oder die Auswahl von Anbauwerkzeugen sowie die Steuerung zahlreicher Fahrer-Komfortfunktionen.
Die großen Hersteller haben in die Entwicklung ihrer neuen Maschinen kräftig investiert. Herbert Kreiseder erzählt, dass Komatsu in den vergangenen Jahren seine Forschungs- und Entwicklungsabteilung um mehr als 1.000 Mitarbeiter aufgestockt hat. Die Abgasemissionsstufe Stufe IIIB / Tier 4i in Verbindung mit höherer Wirtschaftlichkeit war die großen Herausforderung für die Entwicklerteams. Die Stufe IV / Tier 4 final ist in der Entwicklung großteils schon abgeschlossen. Zur Abgasreinigung wird vor allem bei den großen Maschinen auf SCR-Technologie gesetzt.
Bei Liebherr, aber vermutlich auch bei den anderen Herstellern wird diese Technik ein SCRonly-System sein, das ohne Partikelfilter oder Abgasrückführung auskommt. Und da mit der Optimierung der Motorentechnologie die Baumaschinenproduzenten auch zu Elektronikspezialisten wurden, geht die Entwicklung auf diesem Gebiet weiter: Bagger, die weitgehend automatisch und ohne Fahrer ihre Arbeit machen, sollten in einigen Jahren auf den Markt kommen.