Sensorik in der Zerspanung
Digitalisierung. Zerspanungsprozesse lassen sich mithilfe intelligenter Sensornetzwerke analysieren und optimieren.
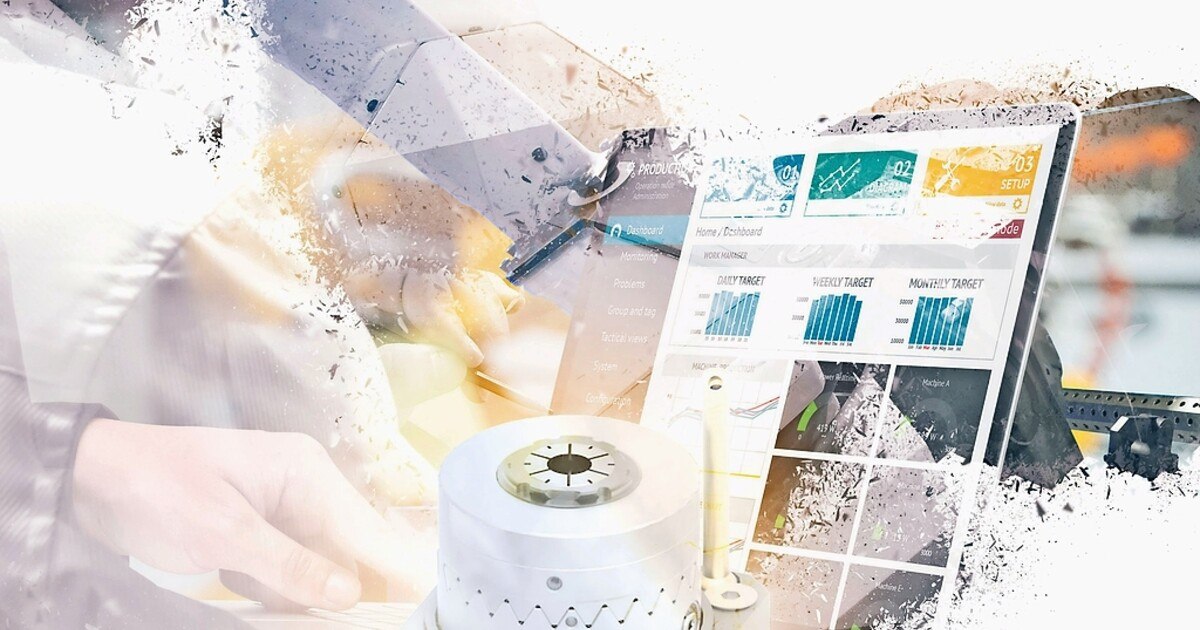
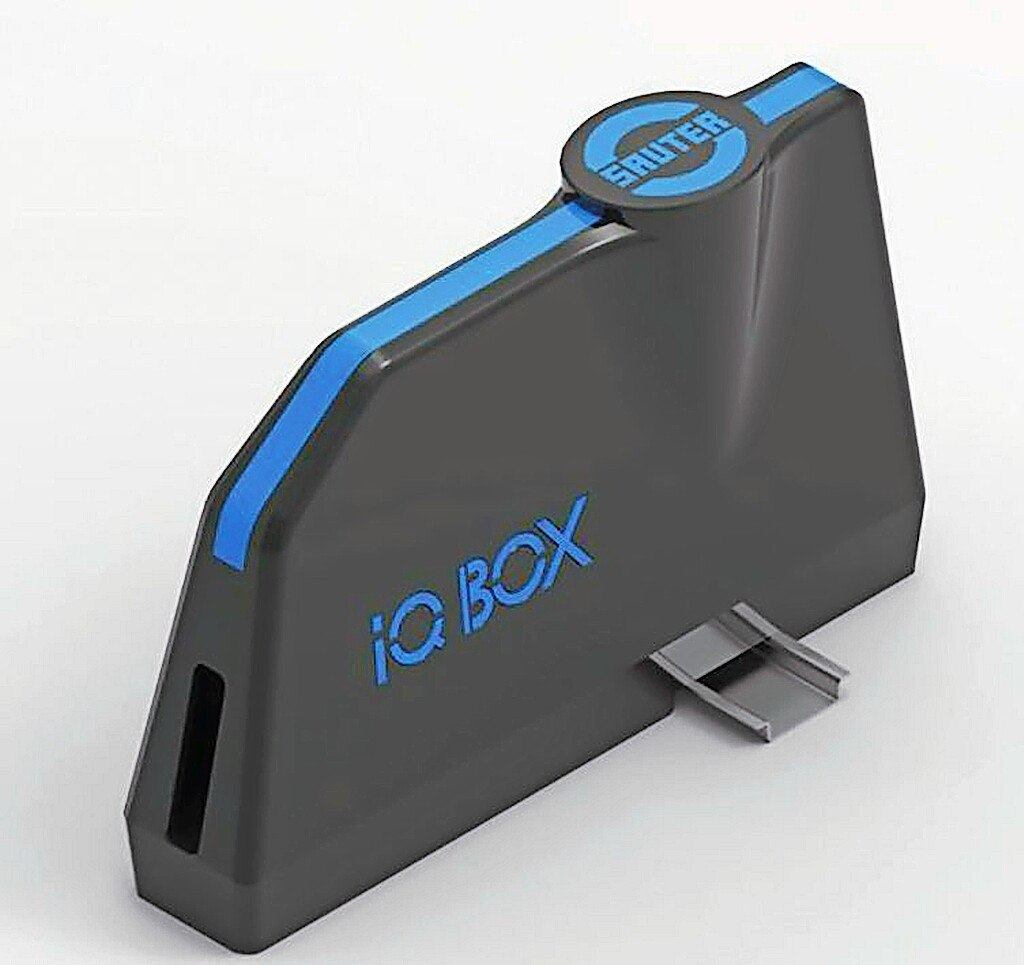
Die Digitalisierung bietet Unternehmen im Maschinenbau ein großes Potenzial, um Werkzeugmaschinen zu optimieren und deren Effizienz zu erhöhen. Allerdings greifen Unternehmen der spanenden Fertigung aus dem Mittelstand bislang noch wenig auf Industrie-4.0-Lösungen zurück. Häufig erfolgt die Regelung von Werkzeugmaschinen manuell oder über binäre Signale. Es fehlen einheitliche Kommunikationsstandards zur einfachen und intelligenten Vernetzung von Maschinen in der industriellen Produktion. Das Maschine-zu-Maschine-Kommunikationsprotokoll OPC Unified Architecture (OPC UA) gilt als vielversprechende Lösung, um herstellerunabhängig Maschinen miteinander zu vernetzen und deren Daten sinnvoll zu bündeln. Werkzeugmaschinenausstatter Sauter setzt auf die Weiterentwicklung OPC UA TSN – eine Kombination mehrerer Technologien, die Daten herstellerübergreifend und in Echtzeit mit einem einheitlichen, offenen Standard übertragen. Der Spezialist für Werkzeugträgersysteme will damit eine durchgehende Kommunikation von der Feldebene bis in die Cloud sicherstellen. Dabei stehen die Informationen nicht nur einem Nutzer, sondern einem Netzwerk aus vielen Teilnehmern zur Verfügung (Publish/Subscribe-Modell). „Die große Herausforderung besteht darin, ein offenes und einheitliches System zu schaffen und die Protokollvielfalt zu beschränken“, erklärt Martin Worch, Leiter Digitalisierung bei Sauter. „Vergleichbar mit IO-Link in der Sensortechnik sind die Schnittstellen eigentlich standardisiert, aber dennoch gibt es zu viele Abweichungen und unterschiedliche Profile.“ Zusätzlich zu OPC UA TSN präferiert das Metzinger Hightechunternehmen das offene Nachrichtenprotokoll MQTT (Message Queuing Telemetry Transport) für die Übertragung von Nachrichten, die nicht zeitkritisch sind. Dabei verbinden sich Sender und Empfänger von Daten kurzzeitig oder als Stream mit einem zentralen Server (Broker). Nachrichten werden nach einem bestimmten Schema übermittelt.
Edge-Computing – ein vielversprechendes Konzept
Edge-Computing ist ein zielführendes Konzept, das eine Verarbeitung großer Datenmengen bei geringen Latenzzeiten ermöglicht. Sensordaten werden direkt oder nahe am Ort ihrer Entstehung verarbeitet, um in Echtzeit aussagekräftige Daten über Maschinenkomponenten und Prozesse zu erhalten. Die Übertragung an ein zentrales Rechenzentrum oder Cloud-Data-Center ist nicht notwendig. Rückmeldungen als Ergebnisse der Datenauswertung erfolgen somit ohne großen Zeitverzug. Datensammler selektieren die Daten und schicken nur ausgewählte Informationen, die für zentrale Prozesse benötigt werden, an die Cloud. Irrelevante Daten werden verworfen. Die dezentrale Datenverarbeitung wird künftig immer mehr an Bedeutung gewinnen, da durch den Einsatz vieler Sensoren in Maschinen und Geräten eine enorme Datenmenge erzeugt wird. Für diese Daten ist weder die vollständige Übertragung noch die längerfristige Speicherung sinnvoll. Für die Umsetzung von Edge-Computing im Bereich der Zerspanung sind Sensoren an den bisher rein mechanischen Komponenten, wie der Schneide, dem Werkzeughalter oder Werkzeugrevolver, notwendig, die wertvolle Prozess- und Statusinformationen liefern. In die Werkzeuge und Werkzeughalter sind Datensammler integriert, die mithilfe spezifischer Auswertelogiken unterschiedliche Informationen selektieren, kombinieren und übermitteln. Eine Auswerteeinheit (etwa die Sauter IQ-Box) führt verwertbare Daten der Datensammler zusammen und verarbeitet diese, um ein Gesamtbild zu erstellen.
Einsatz und Bedeutung von Sensorik
Mit sensorgestützten Systemen lassen sich Zerspanungsprozesse besser überwachen und regeln. Die integrierte Sensorik liefert aussagekräftige Daten über Prozesskräfte und -parameter, wie Vibrationen, Drehmomente, Kräfte, Lagertemperaturen usw. Digitale Signale des Revolvers zeigen beispielsweise an, ob die Werkzeugscheibe verriegelt ist, das Werkzeug eingekuppelt ist und ob das Werkzeug im spanenden Eingriff steht. Indem nicht nur der Revolver, sondern auch Werkzeughalter und Werkzeuge mit Sensoren ausgestattet werden, ergibt sich ein intelligentes Sensornetzwerk. Daten werden somit an mehreren Orten gesammelt und zusammengeführt, um ein möglichst genaues Bild der Bearbeitungsprozesse zu erhalten. Neben den dynamischen Informationen wie Temperatur, Vibration, Rotationsgeschwindigkeit, Moment, Kühlmitteldruck und Kraft sind pseudostatische Informationen wie Betriebsstunden, Bearbeitungshistogramme und die Angabe von aktiven Werkzeugen von großer Bedeutung für die Analyse.
Aufgaben von Datensammlern
Durch den Zerspanungsprozess hervorgerufene Schwingungen können zu erhöhtem Verschleiß der Werkzeuge, schlechten Oberflächenqualitäten des Werkstückes, Werkzeugbruch oder gar Maschinenschäden führen. Bestimmte Schwingungsmuster lassen Rückschlüsse auf den Zustand der Lager und die Qualität des Bearbeitungsprozesses zu. Sensoren an der Schneide erfassen die Vibrationen sowie weitere Parameter und leiten die Messdaten an Datensammler. Durch zusätzliche Sensorik im Werkzeughalter wird der Bearbeitungsprozess ebenfalls überwacht. Indem durch die Datensammler eine erste Datenverarbeitung erfolgt, lassen sich bereits interpretierbare Informationen gewinnen, beispielsweise über Werkzeugverschleiß oder Materialfehler im Bauteil. Zusätzlich zu einer reinen Statusangabe zeigt die Auswertung an, ob die gemessenen Bearbeitungskräfte größer sind als die für diesen Prozess zulässigen Werte. Daten sind miteinander kombinierbar und stehen häufig in Relation zueinander. Ist beispielsweise über die Sensoren von Werkzeughalter und Revolver ein abnormaler Verlauf des Kühlmitteldruckes messbar, kann dies ein Anzeichen für eine Leckage sein. Die Sauter IQ-Box gibt nach dem Empfang der Daten aus den Datensammlern eine direkte Rückmeldung. Im Falle einer Grenzwertüberschreitung ergreift entweder eine Logik oder der Bediener gezielt Maßnahmen, ändert zum Beispiel Vorschub oder Drehzahl oder stoppt den gesamten Bearbeitungsvorgang. Intelligente Auswerteeinheiten sind künftig in der Lage, selbstständig Entscheidungen zu treffen, dem Nutzer wichtige Informationen zur Verfügung zu stellen und unwichtige Daten zu unterdrücken. Indem sich das Netzwerk selbst konfiguriert, kann es dynamisch auf unterschiedliche Sensordaten reagieren. Damit bleibt der Verwaltungsaufwand für den Nutzer überschaubar, trotz komplexer Bearbeitungsprozesse mit vielen verschiedenen Werkzeugen und Werkzeughaltern.
Vorteile der Digitalisierung
Stehen aussagekräftige Daten über Prozesskräfte und -parameter für die Analyse von Bearbeitungsvorgängen zur Verfügung, kann die IQ-Box schnell reagieren. So ist es beispielsweise möglich, die Ursachen für übermäßigen Verschleiß frühzeitig zu identifizieren und Prozesse entsprechend anzupassen. Das intelligente Sensornetzwerk erkennt mögliche Defekte einer Maschine oder Störungen im Prozess, noch bevor sie tatsächlich eintreten. Plötzliche Ausfälle und Stillstandszeiten der Maschinen sind somit vermeidbar. Instandhaltungs- und Wartungsarbeiten lassen sich besser planen, was in einer erhöhten Verfügbarkeit der Maschinen resultiert. Neben Predictive Maintenance ermöglicht die konsequente Nutzung einer Sauter IQ-Box einen weiteren zukunftsorientierten Service: Predictive Manufacturing. Da der Austausch von Verschleißteilen perfekt vorbereitet werden kann, ist er sehr schnell durchführbar. Somit lässt sich eine auf den Kunden zugeschnittene Ersatzteilbevorratung realisieren.
Fazit: Die Analyse gezielter Parameter und die smarte Vernetzung von Daten ermöglichen eine Optimierung von Bearbeitungs- und Einkaufsprozessen. So bietet Sauter mit einer Prototypenanwendung beim Kunden die Möglichkeit, Daten anonymisiert auf einen Cloudserver zu übertragen und voll- sowie teilautomatisch auf Anomalien hin zu untersuchen. Nach erfolgter Datenauswertung und Ursachenforschung ist der Kunde in der Lage, Bearbeitungsabläufe besser zu überblicken und durch gezielte Änderungen eine Prozessoptimierung herbeizuführen.
Intelligente Sensornetzwerke
Werkzeugrevolver und Tooling werden mit Sensoren ausgerüstet, die eine Vielzahl von Daten liefern und miteinander kommunizieren können. Geeignete Systeme wie Edge-Computing verarbeiten aussagekräftige Daten über Maschinenkomponenten und Prozesse in Echtzeit. Dabei reduzieren spezifische Auswertelogiken die Daten, kombinieren sie und übermitteln signifikante Informationen an Auswerteeinheiten. Diese erzeugen stets ein genaues Bild des Bearbeitungsprozesses. Beim Auftreten von Alarmmeldungen können gezielte Maßnahmen ergriffen werden, um einen möglichst kontinuierlichen und effizienten Fertigungsprozess sicherzustellen. Damit ebnet intelligente Sensorik den Weg für Industrie-4.0-Konzepte wie Predictive Maintenance und Predictive Manufacturing.