Automatisierung: Digitalisierung konkret
Die Digitalisierung hebt die CNC-Fertigung auf ein neues Level. Metall gibt einen Überblick, welche Tools die Produktivität verbessern.
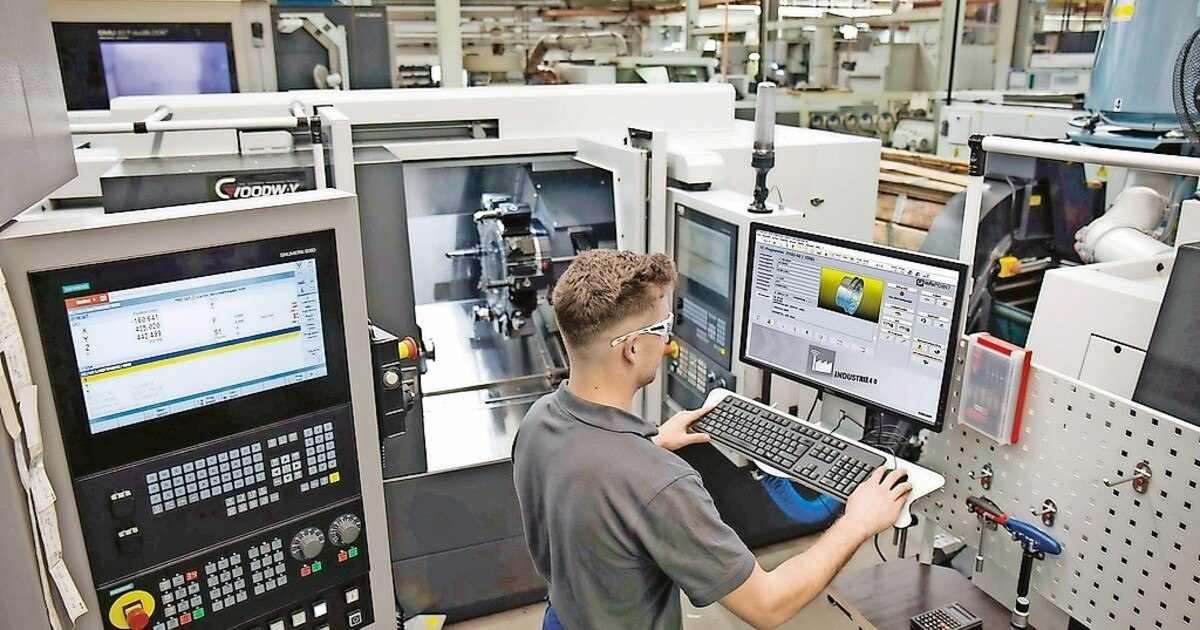
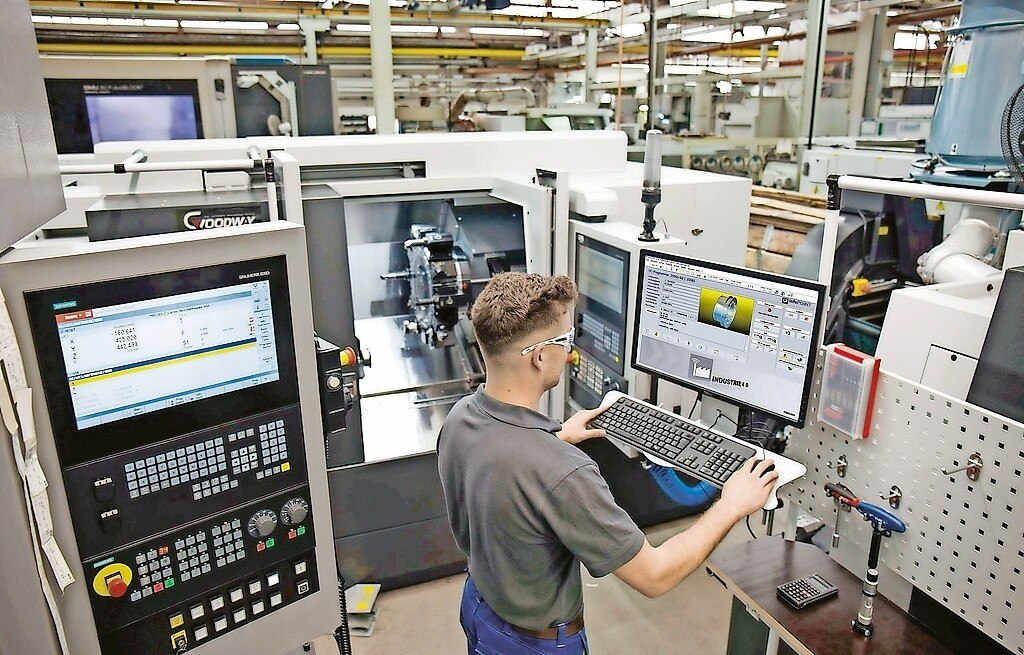
© Coscom – Source: Coscom
Moderne CNC-Maschinen, verbunden mit Automatisierungskomponenten wie Palettenspeicher, Roboter oder Stangenlader, sind heute Grundvoraussetzung für eine produktive Fertigung. Doch um das volle Potenzial der CNC-Fertigung zu heben sind heute zusätzlich intelligente Softwarelösungen wichtig, um die einzelnen Arbeitsabläufe noch effizienter zu gestalten und laufend weiter zu optimieren. Doch welche digitalen Tools sind für CNC-Lohnfertiger relevant?
Schließlich schwirren zu jenem Thema viele abstrakte Begrifflichkeiten durch die Fertigungswelt: Big Data, Cloud Computing, digitale Transformation, digitaler Zwilling, Industrie 4.0, Internet of Things (IoT) oder Smart Factory – die Liste ließe sich wohl ewig fortsetzen.
Hinter jeder dieser Definitionen verbergen sich konkrete Tools oder Softwarelösungen, die den Werkstattbetrieb erheblich erleichtern können –, das gilt auch für kleine Betriebe. Für den Einstieg lohnt es sich zunächst, die Prozessschwächen im Unternehmen auszuloten. Dann kann man sich speziell mit den individuell erforderlichen Tools beschäftigen und den ersten Schritt in die Digitalisierung beginnen. Die gute Botschaft: Die aktuellen Lösungen lassen sich einfacher implementieren als noch vor einigen Jahren und die Investitionen sind mittlerweile überschaubar geworden und amortisieren sich rasch. Das macht die Systeme auch für KMU zunehmend attraktiver.
Die Angebote zum Thema Digitalisierung für die CNC-Fertigung sind so vielfältig, dass im nachfolgenden Überblick zwar viele, aber nicht alle am Markt befindlichen Lösungen Platz finden konnten.
Der Hersteller Coscom verspricht mit dem Virtual-Machining-Konzept (VM) eine durchgängige Software-Lösung entlang der gesamten CNC-Prozesskette – dazu zählt etwa auch ProfiCAM VM, einem integrierten CAD/CAM-System für 2-D- und 3-D-Bear- beitungsstrategien (Zyklen für Drehen, Fräsen, Drehfräsen). Gerade die 3-D-Programmierung macht sich oft bezahlt, dazu nennt Coscom die Referenz eines Maschinenbauers, der laut des Herstellers für das Programmieren eines sehr komplexen Bauteils früher rund drei Monate gebraucht habe und mit ProfiCAM VM nur noch zwei Wochen. Dank des integrierten Postprozessors sprechen die von der Software generierten NC-Programme ohne Nachbehandlung mit jeder namhaften Werkzeugmaschine. Das freut speziell Anwender, die viele unterschiedliche Fabrikate in ihren Werkshallen stehen haben. Wer etwa Prototypen, Einzelteile oder Kleinstserien mit sehr vielen unterschiedlichen Werkzeugen fertigt, wird die digitale Werkzeugverwaltung ToolDirector VM zu schätzen wissen. Nimmt man die vorhandenen Werkzeuge einschließlich aller Technologiedaten systematisch in die Werkzeugdatenbank auf, hat man diese an einem zentralen Platz gut organisiert und ohne Zeitverlust schell parat –, das lohnt sich insbesondere bei der Produktion von Wiederholteilen. Vor der Zerspanung empfiehlt sich unbedingt ein kompletter Check. Da reicht für viele Anwendungsfälle meistens die bereits in ProfiCAM VM integrierte Standardsimulation aus, um bei einfachen 2-D-Programmierungen die Verfahrwege direkt in der Software zu sehen. Für komplexe Bearbeitungszentren empfiehlt Coscom die Maschinensimulation Profi- Kinematik VM, um die Bearbeitung vollständig virtuell anhand des digitalen Maschinenmodells inklusive Materialabtrag, Kollisionsprüfung und Bearbeitungsdauer zu simulieren.

© Emco
Mit seiner modular aufgebauten Software Esprit CAM unterstützt DP Technology ein breites Spektrum von CNC-Maschinentypen über eine gemeinsame Benutzeroberfläche und einen einheitlichen Arbeitsablauf. Da- runter große Portalmaschinen, Langdrehmaschinen für Kleinteile, Drehfräsmaschinen sowie Multitasking-Maschinen. Mit einem digitalen Zwilling liefert die Software eine exakte Simulation der CNC-Maschine und generiert einen maschinenoptimierten NC-Code, der nicht mehr bearbeitet werden muss. Ein Highlight der CAM-Software sind zwei Zyklen für die Hochgeschwindigkeits- bearbeitung. Dabei verspricht der Anbieter vollmundig, dass ProfitMilling im Vergleich zur traditionellen Fräsbearbeitung die Zykluszeit um 75 Prozent verkürzt und die Werkzeuglebensdauer um 500 Prozent verlängert. ProfitMilling habe sich bei vielen Werkstoffen sehr gut bewährt, besonders bei harten und stabilen wie Inconel und Titan. Ebenso rasant dreht der Zyklus ProfitTurning: Ein Viertel weniger Zykluszeit und die dreifache Werkzeugstandzeit. Mit dem Zyklus „Multitasking“ lassen sich multifunktionale Fräs- und Drehmaschinen programmieren, optimieren und simulieren.
Auch der Steuerungshersteller Heidenhain hat sich im Kontext der intelligenten CNC- Fertigung einigen Fragen gestellt: Wie steigere ich die Produktivität der Fertigung? Wie behalte ich den Überblick bei der Mehrmaschinenbedienung? Lohnt sich die Investition in eine neue Werkzeugmaschine? Daraus resultierte die digitale Werkstatt. Dahinter verbergen sich zwei Softwarelösungen, die den Anwender entlang der gesamten Prozesskette unterstützen, die Fertigung komplett digital abbilden und einen kompletten Rundumblick auf die Werkstatt ermöglichen. In die digitale Werkstatt lassen sich CNC-Maschinen und Steuerungstypen aller gängigen Marken einbinden.
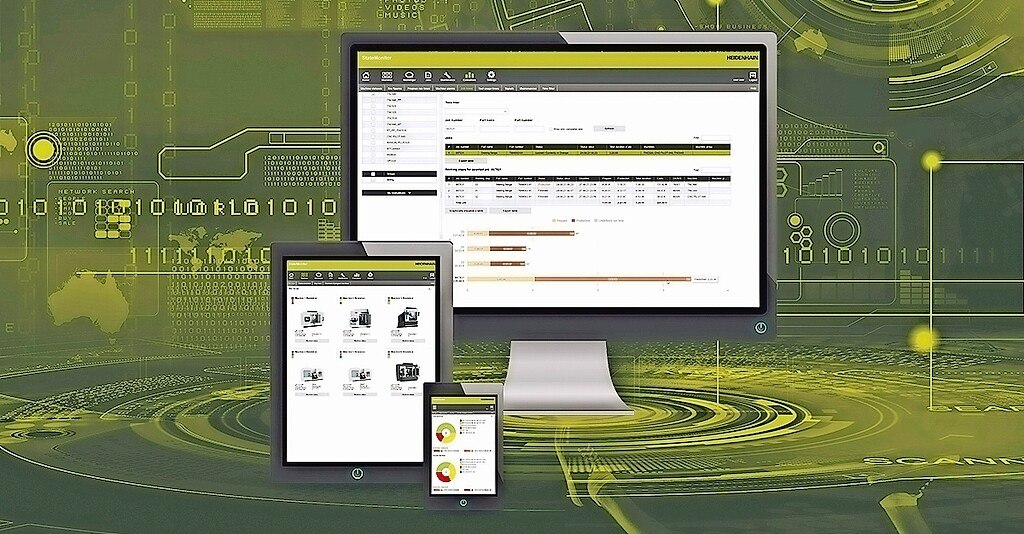
© Heidenhain
Mit der Software StateMonitor werden Maschinendaten erfasst, ausgewertet und visualisiert. Man bekommt eine Echtzeitsicht auf den Fertigungsstatus seiner CNC-Werkzeugmaschinen. In der Software wird der Maschinenpark übersichtlich dargestellt, auf welchem Endgerät, PC, Laptop, Tablet oder Smartphone, bleibt dem Anwender überlassen. Die Statusansicht zeigt den Zustand der Maschinen: produktiv, nicht produktiv, wartend oder nicht im Einsatz. So kann man die Maschinenzustände genau beobachten und anschließend Optimierungsstrategien ableiten. Detaillierte Kennzahlen und Programmlaufzeiten kann man sich auch per E-Mail zu vordefinierten Ereignissen schicken lassen: Beispielsweise, wenn die Maschine steht, der Kühlmittelstand niedrig ist oder ein CNC-Programm abgeschlossen ist. Der StateMonitor überwacht auch die eingesetzten Werkzeuge und deren tatsächliche Nutzungsdauer.
Mit der Software PlantMonitor lassen sich sämtliche Maschinen im Betrieb oder auch an verschiedenen Standorten, vernetzen und somit alle Maschinendaten ortsunabhängig einsammeln und auswerten, um die Fertigungsprozesse überall zu optimieren. Jede Maschine lässt sich live anzeigen und auswerten, der Anwender kann dazu sein Dashboard individuell konfigurieren.
Mit HyperMill Virtual Machining kann Open Mind sämtliche Prozessschritte in der CNC-Fertigung virtuell abbilden. Für die Verschmelzung der virtuellen und realen Welt ist die Software mit drei Modulen ausgestattet: Im Modul Center werden reale Bearbeitungssituationen mit der Maschine und Steuerung virtuell abgebildet und NC- Code-basiert simuliert. Das Modul Connected Machining ermöglicht eine tiefgehende Vernetzung und Synchronisation mit der Maschine. DieSimulationssoftware kann so beispielsweise Abweichungen beim Nullpunkt oder bei den Werkzeugplätzen erkennen. Im dritten Modul Optimizer sorgen Optimierungsalgorithmen für eine effiziente Gestaltung der Mehrachsbearbeitung. Automatisch identifiziert die Software die beste Lösung für eine präzise Bearbeitung. Anwender gehen bei der CAM-Programmierung von Portalfräsmaschinen nun genauso vor wie bei einem 5-Achs-Fräszentrum. Die durch Rund- und Linearachsenlimits sowie durch Kollision erforderlichen Rewinds fügt der Optimizer auf Basis des digitalen Zwillings die Informationen der Maschine automatisch hinzu. Auf unnötige Rückzüge an Sicherheitspositionen zwischen zwei Bearbeitungsschritten mit demselben Werkzeug kann man somit verzichten. Beim Zusammenfassen von Jobs mit dem gleichen Werkzeug werden auch 2-D- und 3-D-Bearbeitungsschritte zu einer fließenden Bewegung.
Ein weiteres Tool für mehr Effizienz in der Bearbeitung ist die intelligente Bauteilausrichtung im CAM in Echtzeit mit HyperMill Best Fit. Mittels einer 3-D-Messung wird das unausgerichtete Bauteil auf der Maschine angetastet und die Messpunkte in Form eines Messprotokolls zurück an das CAM-System gesendet. Anschließend passt HyperMill Best Fit den NC-Code exakt an die reale Bauteilposition an. Der angepasste NC- Code wird dann in der virtuellen Maschine auf der tatsächlichen Aufspannsituation simuliert und automatisch optimiert. Um eine sichere und exakte Bearbeitung zu gewährleisten, führt der Maschineneinrichter eine Verifikationsmessung durch. Dann kann er die Bearbeitung starten, ohne das Bauteil vorher in der Maschine ausrichten zu müssen, was immens viel Zeitgewinn bringt.
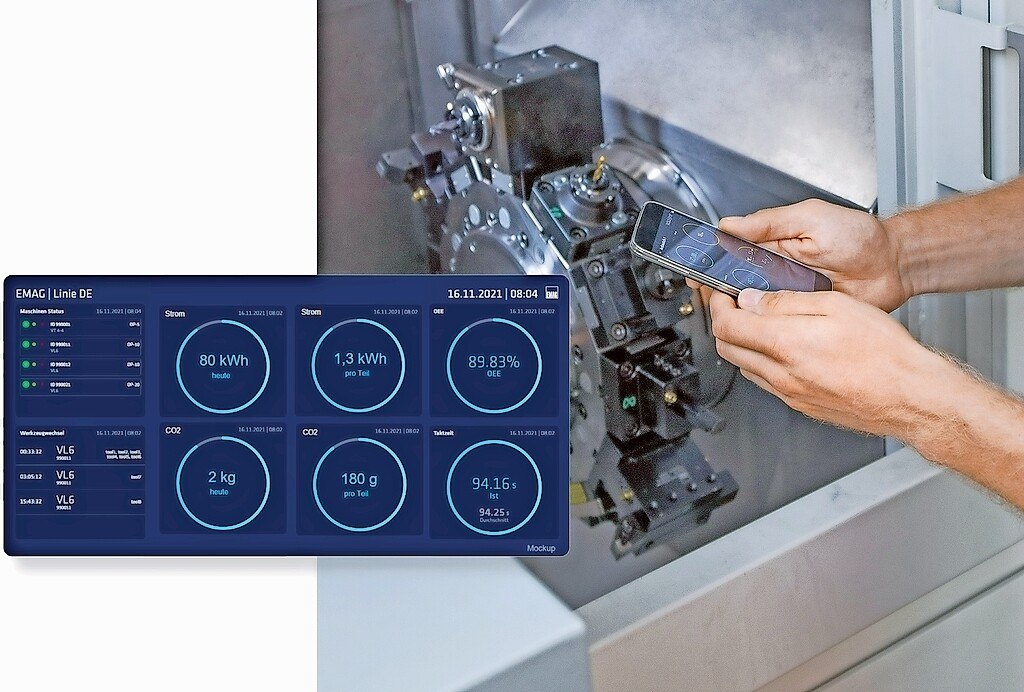
© Emag
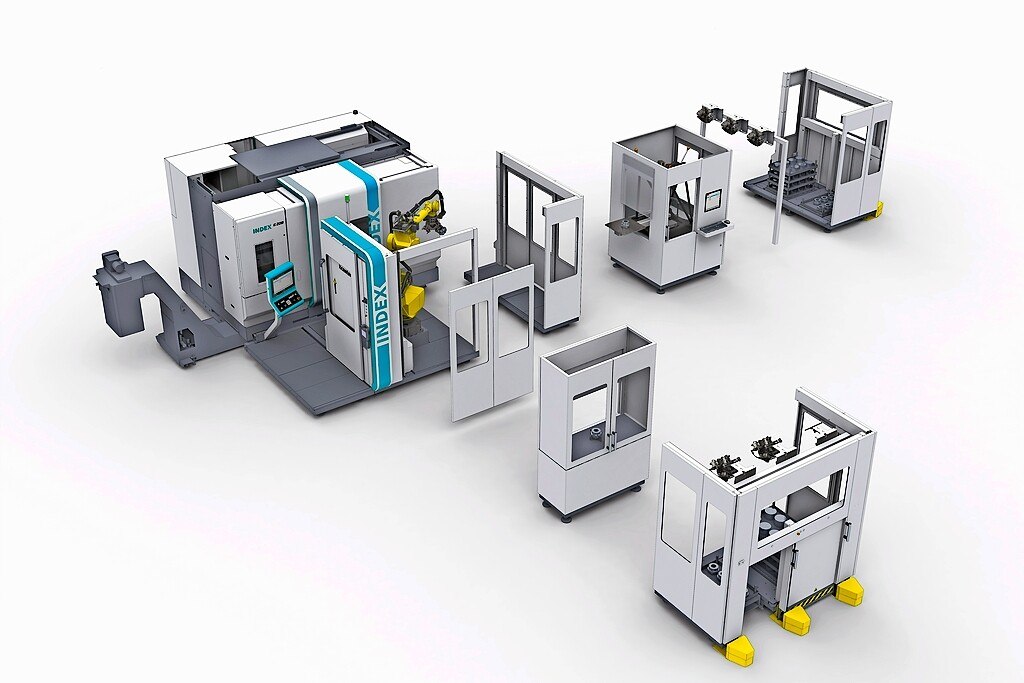
© Index 8“9
Mit der offenen digitalen Businessplattform Xcelerator will Siemens die reale mit der digitalen Welt verbinden. Durch die AnalysevonProduktionsdatensoll das Potenzial zur Optimierung von Werkzeugmaschinen genutzt werden. Dazu bietet das Unternehmen neben Hardware für das Internet der Dinge (IoT) eine Menge Apps. Mit Anwendungen wie Manage My Resources/Tools, Manage My Resources/Programs, Analyze My Performance/OEE, Manage My Machines, Manage My Machines/ Remote und Analyze My Machine/Condition sowie der Industrial Edge for Machine Tools Plattform stellt Siemens auch Angebote für die Werkzeugmaschine über diese Plattform zur Verfügung.
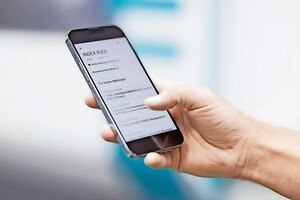
Im Bereich der Arbeitsvorbereitung dienen die Apps Ma- nage My Resources/Tools, Manage My Resources/Programs und Analyze My Performance/OEE einer intelligenten Ressourcenverwaltung, mit der Fertigungsaufträge reibungslos vorbereitet werden können, indem die richtigen Werkzeuge und NC-Programme bereitgestellt werden. Manage My Resources/Tools erlaubt Einblicke in die Werkzeugnutzung, beispielsweise zur Dauer von bestimmten Werkzeugtypen. Es lassen sich auch Werkzeuge für einen bestimmten Maschinen- oder Fertigungsauftrag reservieren. In Analyze My Performance/OEE lässt sich der Maschinenstatusindividuellkonfigurieren. Darüber hinaus ermöglicht die App detaillierte Einblicke in die Werkstückstatistik und den Produktionsfortschritt. Will man die CNC- Maschinen während des Betriebes überwachen, sind die Apps Manage My Machines, Manage My Machines/Remote und Analyze My Machine/Condition zur Stelle und liefern Daten zur Verbesserung der Wartung. Treten unerwartete Veränderungen, zum Beispiel bei der Zerspanleistung oder der Vibration, auf, kann Manage My Machines Meldungen zu technischen Störungen noch genauer zu untersuchen. Manage My Machines ist sehr „offen“, wodurch neben Siemens auch andere Steuerungshersteller unterstützt werden.
Sind in der Fertigung die Zerspanungswerkzeuge nicht zum richtigen Zeitpunkt an der richtigen Maschine, dann läuft der Bearbeitungsprozess nicht reibungslos ab. Eine einheitliche Datenbank für alle Werkzeuge ist dafür unverzichtbar. Dafür bietet TDM Systems seine Softwarelösungen für die digitale Verwaltung der Werkzeuge an. Die „große“ Lösung TDM Global und speziell für kleinere Zerspaner, die auf der Suche nach einer einfachen, kostengünstigen Einstiegslösung sind, die cloudbasierte Softwarelinie TDM Cloud Essentials. Damit gewinnen auch kleinere Betriebe den exakten Überblick über ihre Werkzeuge und treiben die Digitalisierung nachhaltig voran.
Um die Produktivität und Effizienz zu erhöhen, bieten auch die Werkzeugmaschinenhersteller eine Menge zusätzlicher digitaler Lösungen. Bei Chiron sorgt SmartLine bei den CNC- Bearbeitungszentren für eine höhere Verfügbarkeit und gesteigerte Produktivität. Die Software übernimmt das Monitoring der Maschinen, die automatische Zustandsüberwachung, simuliert und optimiert die Bearbeitungsabläufe und hilft auch Kollisionen zu vermeiden.
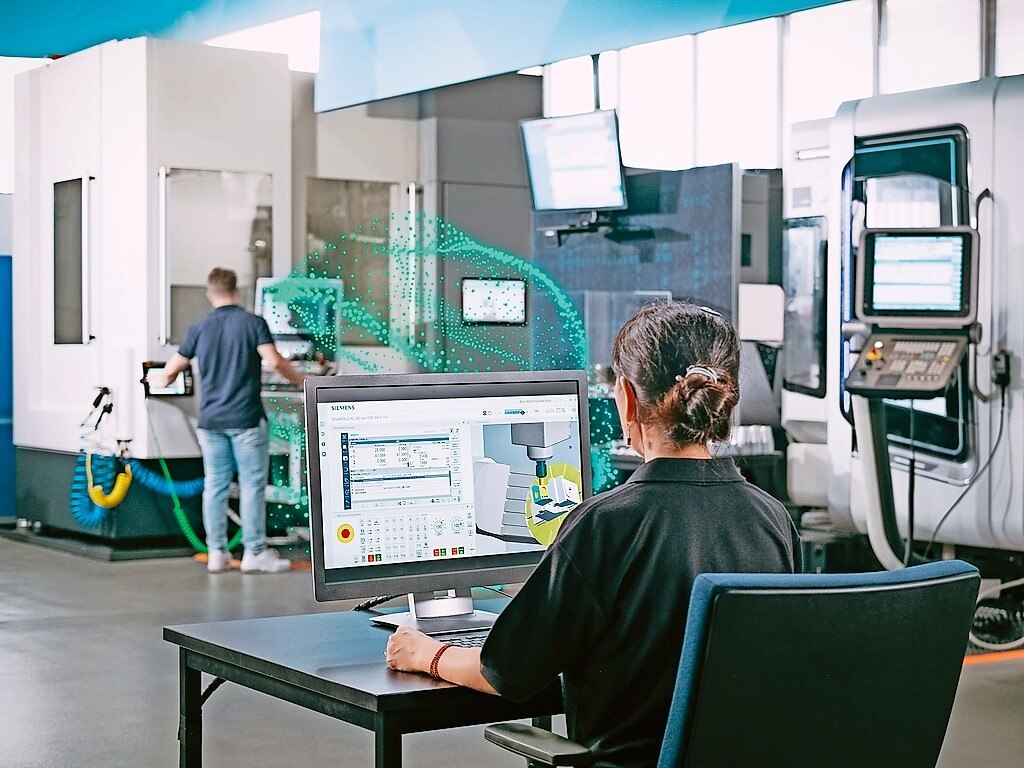
© Siemens
Bei Emag bleibt die datenbasierte Analyse und Optimierung von Produktionsprozessen im Fokus. Unter dem Namen Edna (Emag DNA) treiben die Maschinenbauer die datenbasierte Vernetzung ihrer Produktionslösungen weiter voran. Auf diese Weise lassen sich etwa der Zustand einer Maschine exakt bestimmen und ihre aktuelle Produktionsleistung abfragen. Nunmehr präsentiert Emag den „Edna Energy Monitor“, mit dem man einen ungewöhnlich hohen Energieverbrauch der Maschine und auch pro Werkstück jederzeit erkennen kann.
Mit dem CPS-Pilot gibt Emco dem Anwender einen digitalen Zwilling der Maschine an die Hand. Damit wird der gesamte Bearbeitungsprozess vorab simuliert, um auch die Rüst- und Einfahrzeiten an der Maschine zu reduzieren. Der Digital Twin begleitet den Prozess mit dem Ziel, ein prozesssicheres NC-Programm in die reale Fertigung zu übergeben. Zusätzlich kann der CPS-Pilot schon im Vorfeld exakte Zeitstudien und eine vorgelagerte Kollisionsprüfung durchführen.
Index verhilft dem Anwender über die cloudbasierte Plattform iXworld und zahlreichen Apps zu mehr Effizienz über die gesamte Prozesskette. In die neue iX4.0-App iXmobile für Smartphones kann man alle Maschinen hinzufügen und jederzeit den aktuellen Produktionsstatus ansehen. Deuten sich Maschinenprobleme an, erhält der User sofort eine Benachrichtigung. Dadurch lassen sich kostenintensive Stillstände besondere im bedienerarmen oder bedienerfreien Betrieb schnell erkennen und verhindern.
Das deutsche Unternehmen Okuma unterstützt den Anwender durch seinen 3D Virtual Monitor, der anhand der exakten technischen Daten der Werkzeugmaschine, die detaillierte, dreidimensionale Simulation des gesamten Fertigungsprozesses ermöglicht. So sind eventuelle Programmierfehler, die zu teuren Kollisionen führen können, noch vor dem Fertigungsstart schnell erkannt und lassen sich korrigieren.
Der Hersteller WFL verwendet zur Optimierung seiner großen Werkzeugmaschinen smarte Gehilfen wie my WFL. Damit behält der User rund um die Uhr den Überblick über die Betriebsdaten und den Maschinenzustand. Die Software sammelt alle Daten in der Produktion, analysiert diese, um danach eine höhere Produktivität zu ermöglichen. Die Familienmitglieder myWFL Cockpit zeigen die Performance und myWFL den aktuellen Energieverbrauch (Strom, Druckluft) einer Maschine auf. Die visualisierten Infor- mationen kann man sich auf der Steuerung, am PC oder und mobil am Smartphone ansehen.
[Erschienen in: METALL 10/2022]