Mehr KI, weniger Mensch?
Die Künstliche Intelligenz (KI) erlebt derzeit einen regelrechten Boom. Einige Beispiele zeigen was in der Metallbearbeitung aktuell schon möglich ist
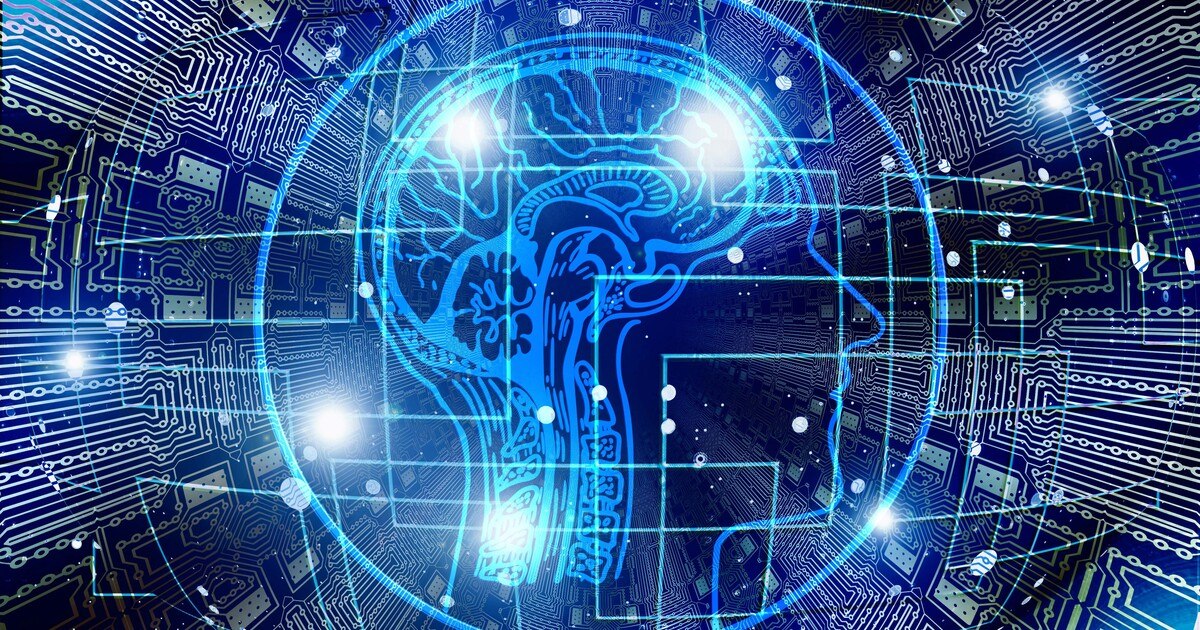
Künstliche Intelligenz (KI) ist in unserem Alltag längst Realität. In der Metallbearbeitung hält sie eher langsam Einzug und steht am Anfang. Das liege auch daran, sagt Tom Schneider, Geschäftsführer für Entwicklung des Geschäftsbereichs Werkzeugmaschinen bei Trumpf, „dass Fehlentscheidungen im Maschinenbau im Gegensatz zu Smartphone Apps mitunter desaströse Folgen haben.“ Ein anderer Grund könnte die Zurückhaltung sein, die Industrieunternehmen bei der Freigabe ihrer Produktions- und Fertigungsdaten an Dritte an den Tag legen. Denn Künstliche Intelligenz braucht Anwendungsdaten, um zu lernen.
KI-Systeme „lernen“ aus verarbeiteten Daten, indem sie ihre Algorithmen anpassen.
Die Basics
Die Idee „denkender Maschinen“ ist ziemlich alt, und auch der Begriff „Künstliche Intelligenz“ oder Artificial Intelligence (AI) wird schon seit den 1950er Jahren benutzt, wenn es um maschinelle Systeme geht, die menschenähnliche Intelligenzleistungen erbringen. KI-Systeme „lernen“ aus verarbeiteten Daten, indem sie ihre Algorithmen anpassen. Sie kommen zu Ergebnissen, die nicht im ursprünglichen Programm festgelegt sind. Im Wesentlichen geht es dabei um das Erkennen von Mustern in großen Datenmengen und um das Ableiten von Entscheidungen.
KI im Blechhandling
Blechbearbeiter haben es nicht einfach: die starke Varianz der Werkstücke bei kleinen Losgrößen, ein hoher Kostendruck und Personalmangel sind die aktuellen Herausforderungen in der Metallbearbeitung. Mit einem mehrteiligen Automation-System von Schmalz soll das Blechteile-Handling automatisiert ablaufen. Künstliche Intelligenz spielt dabei eine tragende Rolle. Der Hebetechnik-Spezialist hat ein Solution Kit ivOS Sheet Metal entwickelt, das das Blechteile-Handling automatisiert. Das dreiteilige System besteht aus einer 3D-Kamera, dem Vision Operating System ivOS und dem flexiblen Matrixgreifer FMG. Das System passt sich automatisch an die wechselnden Werkstückgeometrien an. Aufwändige Greiferwechsel lassen sich dadurch drastisch reduzieren. Da die Ansteuerung dieses universell einsetzbaren Greifsystems komplex ist, übernimmt eine lernende KI (künstliche Intelligenz) die Aufgabe. Sie erkennt über ein Kamerasystem die unbekannten Werkstücke und steuert den Greifer so an, dass er das Blech bestmöglich aufnehmen kann. Anschließend überwacht das Vision Operating System ivOS die Griffqualität während des Handhabungszyklus und navigiert den Roboter mit dem Produkt kollisionsfrei an die Zielablage. Das alles passiert autonom, ohne dass die Nutzerinnen und Nutzer Fachkenntnisse zur Bedienung der Anlage benötigen.
KI in der Maschinenwartung
In der Industrie ist der Trend zur KI angekommen. Der Werkzeugmaschinenbauer J.G. Weisser Söhne beispielsweise setzt auf KI-Modelle, die vorausschauende Wartung von Drehmaschinen ermöglichen. „Bei der vorausschauenden Wartung wird mithilfe von KI prognostiziert, wann ein Wartungsbedarf an einer Maschine entstehen wird, bevor es zu einem Ausfall kommt“, erklärt Dr.-Ing. Robin Hirt, Geschäftsführer und Gründer des Karlsruher Start-ups Prenode GmbH. Das Softwareunternehmen unterstützt Maschinenbauer dabei, Anlagen mit kundenspezifischen KI-basierten Features auszustatten.
Moderne Produktionsmaschinen können sich mithilfe Künstlicher Intelligenz selbst optimieren, sagt Hirt. „Sie nutzen dazu in der Regel so genannte Machine-Learning-Methoden, die es ihnen ermöglichen, Muster und Zusammenhänge in den Produktionsdaten zu erkennen und daraus automatisch Verbesserungen abzuleiten.“ Auch das Lernen aus Fehlern und die Übernahme des Know-hows von anderen Maschinen sei so in vielen Fällen möglich.
Da die Daten einer einzelnen Drehmaschine häufig nicht ausreichen, um ein präzises KI-Modell zu trainieren, kommt die Technik des Federated Learning zum Einsatz. Federated Learning ermöglicht es, mit dezentral gespeicherten Daten ein gemeinsames KI-Modell zu trainieren, ohne die Daten direkt auszutauschen. Die individuellen Daten verbleiben also auf den jeweiligen Anlagen und müssen nicht zentral an einem Ort, beispielsweise in einer Cloud des Maschinenherstellers, gespeichert werden. Die KI-Modelle schätzen aufgrund aktueller Drehmaschinendaten den gegenwärtigen Zustand der Anlage ab und geben diesen an das Bedienpersonal weiter. Eingesetzt werden dabei neuronale Netze aus dem Bereich des Deep Learnings.
Beim Dezentralen Machine Learning werden mehrere Maschinen miteinander vernetzt und bilden gemeinsam ein KI-System.
KI als schlauer Sortier-Assistent
Mit Künstlicher Intelligenz funktioniert auch der Sorting Guide, ein System des Laserspezialisten Trumpf aus dem baden-württembergischen Ditzingen, das beim Sortieren produzierter Teile hilft und so die Maschinenauslastung steigern kann. Der Sorting Guide ist ein kamerabasiertes Assistenzsystem und setzt auf Dezentrales Machine Learning. Hauptbestandteile des KI-Systems sind eine hochauflösende Kamera, ein großer Bildschirm, ein Industrie-PC und eine intelligente Software zur Bildverarbeitung. „Beim Dezentralen Machine Learning werden mehrere Maschinen miteinander vernetzt und bilden gemeinsam ein KI-System“, erklärt Prenode-Geschäftsführer Hirt das Prinzip. Dabei sammeln die Maschinen kontinuierlich lokal Daten über ihre Arbeitsvorgänge. Dann wird für jede Maschine ein KI-Modell entwickelt, das anschließend zentralisiert wird. „In einer zentralen Cloud werden diese Modelle dann fusioniert und wieder in die einzelnen Anlagen zurück übertragen“, so Hirt weiter. Das KI-System könne dann lokal auf alle Erfahrungen der anderen Maschinen zurückgreifen, ohne dass jemals sensible Rohdaten ausgetauscht werden müssten. „Auf diese Weise können die Maschinen ihre Arbeitsvorgänge effizienter gestalten und eine höhere Produktivität erreichen“, verspricht Hirt.
Beim Sorting Guide von Trumpf soll das konkret so funktionieren: Durch vorhandene Stammdaten und selbstlernende Bildverarbeitung erkennt der Sorting Guide entnommene Teile und gibt über den Bildschirm eine Empfehlung zum Absortieren. Die produzierten Teile sind auf dem Bildschirm farbig markiert, beispielsweise nach Kundenauftrag oder folgenden Arbeitsschritten wie zum Beispiel Abkanten, Entgraten, Lackieren oder Versand. Aufwändiges Nachzählen der Teile und manuelle Rückmeldungen oder Begleitpapiere sollen so überflüssig werden. Das Bedienpersonal der Maschine sieht auf einen Blick, welche Teile bereit sind für die Weiterverarbeitung und wo gegebenenfalls die Nachproduktion eingeleitet werden muss. Das Absortieren wird beschleunigt, Fehler werden vermieden, und die Maschine kann schneller weiter produzieren. KI und Fertigung gehen Hand in Hand, da Menschen und Maschinen im industriellen Produktionsumfeld eng zusammenarbeiten müssen.
KI optimiert die Zerspanung
Auf Künstliche Intelligenz setzt auch ein neues Verfahren, das den Werkzeugverschleiß in Zerspanungsprozessen, also etwa beim Bohren oder Fräsen, analysiert. Einerseits sollen die teuren Werkzeuge möglichst lange eingesetzt werden. Andererseits ist es wichtig, die Restlebensdauer genau abzuschätzen. Denn ein Werkzeugbruch und ein zerstörtes teures Werkstück oder sogar ein Schaden an der Werkzeugmaschine müssen vermieden werden.
Bislang löst man diesen Zielkonflikt so: Die Werkzeuge werden vorzeitig nach einer erfahrungsbasierten Zahl von Arbeitsgängen ersetzt, um Qualitätsverluste oder gar teure Stillstandzeiten durch Werkzeugbrüche zu vermeiden. Allerdings kostet der Werkzeugaustausch Zeit und Geld, weshalb es sich lohnt, die Wechselzyklen zu optimieren. Hier kommt die KI ins Spiel. Um den Verschleißzustand zuverlässig vorhersagen und so Zerspanprozesse optimieren zu können, haben Forscher der Technischen Universität Kaiserslautern ein Verfahren entwickelt, das das System anhand von realen Prozess- und Messdaten trainiert.
Konkret läuft das so: Um den Verschleißzustand von Zerspanwerkzeugen vorhersagen zu können, werden zunächst prozessbezogene Kenngrößen herangezogen. Dazu zählen unter anderem die beim Zerspanen wirkenden Kräfte, Schwingungen der Maschine sowie der Leistungsbedarf der Maschinenachsen. Ebenso werden Daten aus kontinuierlichen Messungen am Werkzeug und am Werkstück gesammelt. Die größte Herausforderung besteht dann darin, Korrelationen in den gesammelten Daten zu ermitteln.
Suche nach Mustern
Hierfür trainieren die Forscher das KI-gestützte System, das Methoden des Maschinellen Lernens nutzt, um mögliche Muster zu erkennen und daraus Schlüsse zum Verschleißzustand abzuleiten. Darüber hinaus soll es vorhersagen können, mit welchen Prozessparametern Unternehmen bei bestimmten Zerspanprozessen arbeiten müssen, um das Werkzeug für eine angestrebte Nutzungsdauer zuverlässig im Einsatz zu halten. Die Daten, die das System zum Lernen braucht, werden bei fünf Partnerunternehmen erhoben – darunter sind Global Player ebenso wie kleine und mittlere Unternehmen.
Dabei werden verschiedene Varianten durchgespielt, was etwa Werkzeug- und Werkstofftypen oder Prozessparameter betrifft, und so eine breite Datenbasis über die gesamte Lebensdauer bis hin zum Versagen des Werkzeugs erfasst. Die Beispiele zeigen: Künstliche Intelligenz ist also schon ziemlich schlau. //