Was Tischler beim Nesting beachten müssen
Tipps, wie Tischler eine Nesting-Maschine für ihre Bedürfnisse finden bzw. um deren Potenziale optimal zu nutzen.
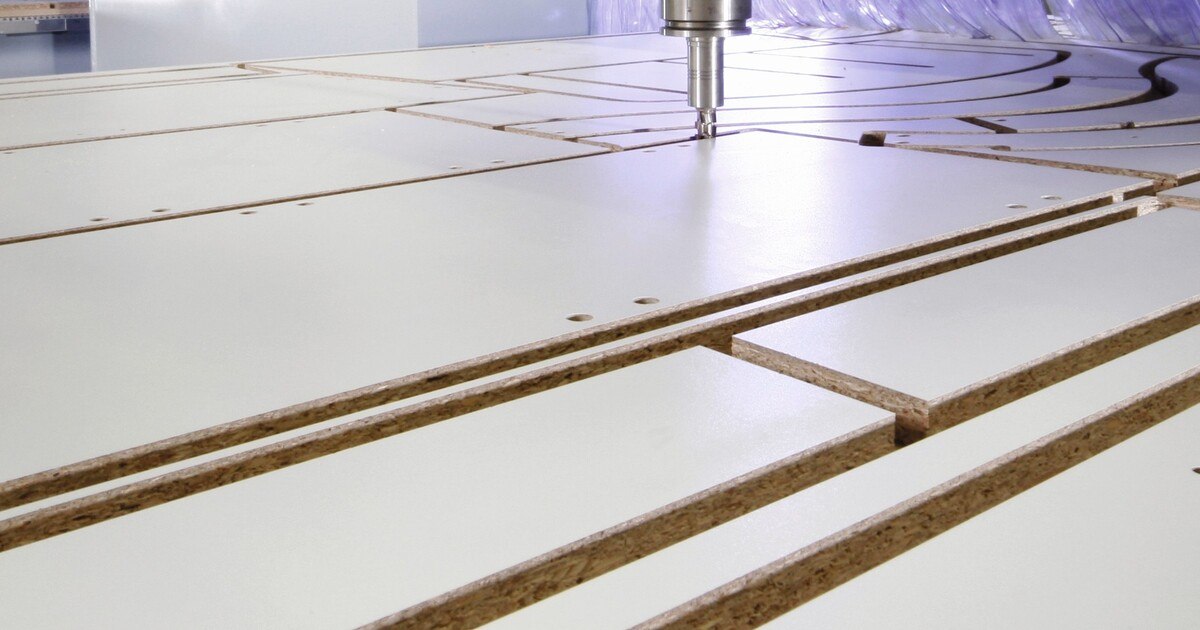
-
© Homag -
© Homag -
© Homag -
© Homag -
© Homag
Ein international sehr etabliertes Produktionsverfahren findet in Europa in den vergangenen Jahren immer mehr Anklang und weckt die Neugier vieler Tischler – Nesting. In dem Zusammenhang ist oft von Nesting-Maschinen, Nesting-Software oder Nesting-Optimierung die Rede. Die Begriffe prägen sich ein, obwohl beispielsweise der Begriff Nesting-Maschine genaugenommen falsch ist.
Ein international sehr etabliertes Produktionsverfahren findet in Europa in den vergangenen Jahren immer mehr Anklang und weckt die Neugier vieler Tischler – Nesting. In dem Zusammenhang ist oft von Nesting-Maschinen, Nesting-Software oder Nesting-Optimierung die Rede. Die Begriffe prägen sich ein, obwohl beispielsweise der Begriff Nesting-Maschine genaugenommen falsch ist.
Weitgehend bekannt ist bereits, dass der Begriff Nesting eine Verschachtelungsphilosophie beschreibt. Es handelt sich um ein Verfahren, bei dem einzelne Formen so optimiert und verschachtelt angeordnet werden, dass so wenig Verschnitt wie möglich anfällt. Dieses aus der Textilindustrie stammende Prinzip kann in dieser Logik auf diversen CNC-Maschinen zum Einsatz kommen. Voraussetzung dafür ist der richtige Softwarebaustein und dass das Spannsystem des CNC-Tisches diese Bearbeitung zulässt.
Die optimale Verschachtelung von Werkstücken kann auf mehreren Maschinen unterschiedlich profitabel und optimal durchgeführt werden. Wenn im Maschinenbau demnach von Nesting-Maschinen gesprochen wird, handelt es sich in der Regel um Gerät mit flacher Auflagefläche und einem durchgehenden Spannsystem – auch Rastertisch oder Flachtisch genannt . Dabei wird mittels Vakuum auf der Tischplatte die gesamte Rohformat-Platte gleichmäßig ansaugt und so für die optimale Haltekraft für das auszufräsende Werkstück gesorgt.
Sie interessieren sich für eine Flachtischmaschine oder möchten den Anforderungen an die Materialeinsparung gerecht werden? Im Folgenden finden Sie acht Tipps, um ein Produkt für Ihre Bedürfnisse zu finden – oder, falls Sie bereits glücklicher Besitzer einer Maschine sind, um die Potenziale optimal zu nutzen.
Tipp 1: Die Haltekraft
Je größer die Zerspanungsfläche, desto größer die benötigte Vakuumleistung. Besteht Ihr Produktprogramm z. B. aus vielen Kleinteilen oder Ausschnitten, benötigen Sie eine höhere Vakuumleistung als bei Hochschränken. Spezialisten verwenden bei Flachtischmaschinen die Faustformel 100m³/h pro Quadratmeter um ein vielseitiges Programm prozesssicher und ohne Aufsicht zu produzieren.
Um bei der Bearbeitung nicht in den Tisch zu fräsen, wird eine sogenannte Schonplatte/ Verschleißplatte auf dem Flachtisch befestigt. In der Regel ist diese Platte zwischen 5 und 22 mm dick. Das Material ist MDF. Der positive Nebeneffekt dieser Schonplatte ist, dass das Vakuum, welches mittels vieler kleiner Zugangspunkte auf dem Tisch verteilt wird, über die Schonplatte trichterförmig an die Oberfläche gelangt und somit ein gleichmäßiges Vakuum erzeugt. Bei dünnen Schonplatten wirkt das Vakuum somit in einem kleineren Bereich und es kann passieren, dass das Werkstück nicht mehr optimal auf dem Flachtisch hält.
Der Algorithmus einer Flachtischmaschine ist für die Bearbeitung kleiner Werkstücke so ausgelegt, dass zunächst alle möglichen flächigen Bearbeitungen durchgeführt werden, bevor der Zerspanungsprozess gestartet wird. Sobald die Auftrennung erfolgt, wird das Werkstück den Kräften innerhalb des Portals ausgesetzt: Vakuum saugt das Werkstück von unten an, die Absaugung zieht das Werkstück nach oben, und die Splitterschutzlappen laufen seitlich über das Werkstück. Letzteres ist oft Ursache dafür, dass das Werkstück seine Position verlässt und somit der Unterdruck zwischen Werkstück, Schonplatte und Tisch verloren geht. Im Randbereich ist dieser aufgrund der trichterförmigen Verteilung schwerer aufrechtzuerhalten als in der Mitte des Tisches.
Mit der Schnitt Profi(t)-Optimierungssoftware können Kleinteile bevorzugt mittig positioniert werden.
Die Flexibilität der Splitterschutzlappen ist entscheidend, gegebenenfalls können diese durch zusätzliche Funktionen minimal höhenreguliert werden.
In der Regel entspricht die Größe des Flachtisches auch der des gängigen Plattenformates, z. B. Halbformat. Durch diese Konzipierung in Kombination mit dem Tischaufbau wird sichergestellt, dass zu dem gewünschten Zeitpunkt die gesamte Platte auf dem Tisch gehalten wird. Werden individuelle Werkstücke oder kleinere Platten verarbeitet, wird der nicht benötigte Bereich abgedeckt, oder er kann über eine Funktion deaktiviert werden. Die Feldeinteilung ist herstellerabhängig und hängt ganz von den individuellen Bedürfnissen ab. Je mehr Felder Sie individuell steuern können, desto geringer ist Ihr Bedarf und umso fokussierter die Leistung, die auf dem Bereich erreicht werden kann.
Ein gleiches Phänomen sehen wir auch bei der Verwendung von doppelt wirkenden Vakuumsaugern auf der Schonplatte. Deren Haltekraft kann deutlich erhöht werden, sofern der Rest der aktivierten Schonplatte luftdicht verschlossen ist. Besteht Ihr Produktionsportfolio aus vielen unterschiedlich großen Rohformatplatten, sollten Sie eine automatische Aktivierung der Vakuumfelder in Erwägung ziehen, sodass nur ein geringer Teil der Schonplatte abgedeckt werden muss.
Hier heißt es Achtung: Immer wieder ist zu hören, dass doppelt wirkende Sauger auf die Schonplatte gesetzt werden und das Werkstück direkt darauf gespannt werden kann. In der Realität ist das nur die halbe Wahrheit. Denn wie Sie bereits erfahren haben, müssen nicht verwendete Bereiche mit einer Folie oder einem luftdichten Gegenstand abgedeckt werden und die Sauger müssen, um den notwendigen Unterdruck zu erzeugen, über Schläuche direkt an das Vakuum-System der CNC-Maschine angeschlossen werden. Dennoch können durch den Einsatz doppelt wirkender Sauger Stillstandzeiten verringert werden, da die Schonplatte nicht vom Tisch gelöst und später wieder befestigt werden muss.
Übrigens, der geforderte Unterdruck bei doppelt wirkenden Saugern ist 0,6 bar.
Beim Handling oder Positionieren von Halbformatplatten kann es passieren, dass es durch das Schieben auf der Schonplatte zu Beschädigungen oder Kratzspuren im Werkstück kommt. Je nach Dichte des Materials kann es für den Nutzer sehr schwer sein, diese Platte von einem zum nächsten Punkt zu bewegen. Der Einsatz der Luftkissenfunktion des Geräts generiert eine Art Luftpolster zwischen Schonplatte und Werkstück und ermöglicht so ein werkstückschonendes und ergonomisches Handling für den Bediener.
Tischler setzen sehr häufig qualitativ hochwertige Möbelverbinder ein, um sich von den Massenherstellern zu differenzieren; auch Scharniere und Beschläge werden mittlerweile häufig direkt in die Werkstückseite eingelassen. Anwendungen wie diese sind jedoch nur über einen separaten Umspannvorgang möglich.
Betrachten wir den internationalen Markt, der wie zu Beginn erwähnt, mit dem Nesting-Verfahren sehr vertraut ist, sehen wir den Trend zur Ergänzungsmaschine, wie die Bohr- und Dübelspechtmaschine Drillteq D-510. Hier werden die Bearbeitungen im Randbereich auf eine separates kleines Gerät ausgelagert, während die Flachtischmaschine ihre materialeinsparende Aufgabe übernehmen kann.
Bei einer Investition in eine Flachtischmaschine mit Nesting-Verschachtelung informieren Sie sich bei Homag, um eine Anlage zu finden, die zur Ihren Bedürfnissen passt.
Text: Vera Katharina Zimmermann/Homag Produktmanagerin für CNC-Technik.
Herkunft von Nesting
Hintergrund
Das Nesting-Verfahren erscheint zwar neu, wurde aber schon vor etlichen Jahren in der Textilindustrie eingesetzt und diente der optimalen Verwendung von Stoffen ohne Reste.