3D-Druck: Das Plus beim Guss
Additive Fertigung und neue Produktionsverfahren erweitern die Möglichkeiten der Gießereibranche.
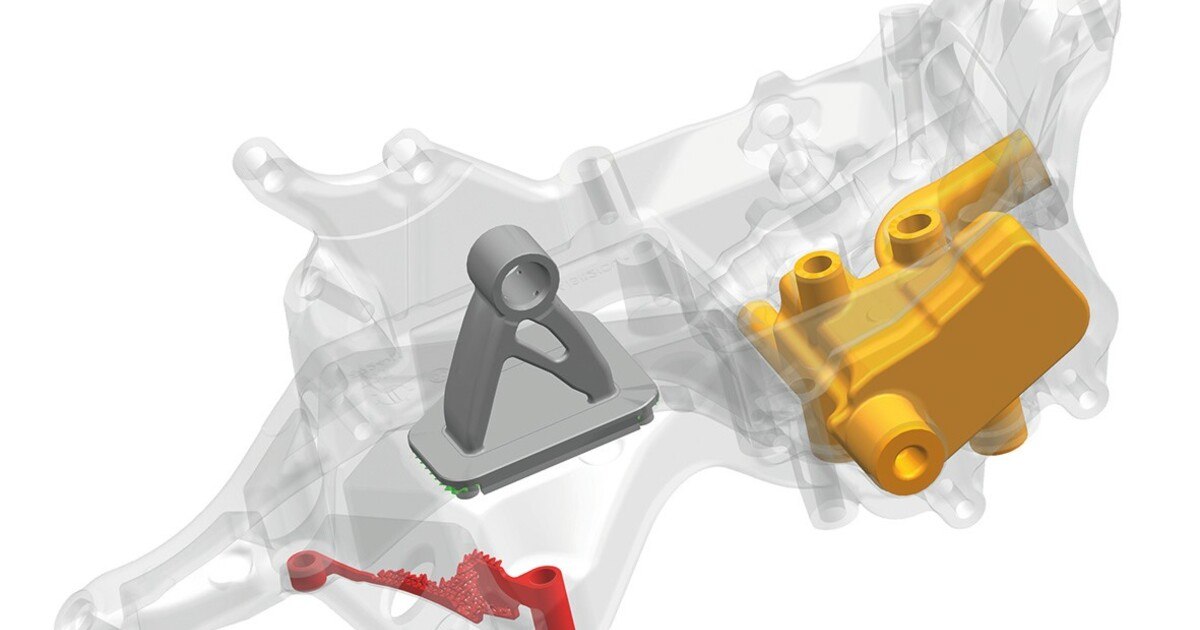
Die additive Fertigung hat in den letzten Jahren ein rasantes Wachstum verzeichnet und die Zukunft glänzt golden: Expert*innen erwarten innerhalb der nächsten vier Jahre ein weiteres Wachstum von rund 20 Prozent. Davon profitiert auch die Metallbranche: Stahlwerke und Gießereien, metallurgische Anlagenbauer und Zulieferer nutzen den 3D-Druck und neue Fertigungsverfahren für unterschiedlichste Geschäftsmodelle, wie auf den Fachmessen Metec, Gifa und Newcast vom 12. bis 16. Juni 2023 in Düsseldorf zu sehen sein wird.
Gießereien und Stahlunternehmen bietet die Additive Fertigung mit den unterschiedlichsten generativen Verfahren vielfältige Chancen. Ist für Stahlhersteller in erster Linie der direkte 3D-Druck in Metall eine Ergänzung des bestehenden Geschäfts und eine zunehmend wichtigere Säule für Reparatur und Ersatzteilbeschaffung, so stechen für Gießereien vor allem indirekte additive Verfahren, insbesondere der 3D-Druck von Formen, Kernen und Modellen mit Sand hervor.
“Additive Manufacturing wird schon lange nicht mehr nur für die Herstellung von Prototypen verwendet“, sagt Dr. Markus Heering, Geschäftsführer der im vergangenen Jahr gegründeten Arbeitsgemeinschaft Additive Manufacturing (AG AM) im Verband der deutschen Maschinen und Anlagenbauer (VDMA). In der Maschinenbauindustrie ist die Additive Fertigung ein komplementäres Fertigungsverfahren, das Entwicklung und Innovation ermöglicht und neue Anwendungen erschließt. Der Maschinenbauexperte unterstreicht das Potenzial der generativen Verfahren für die Industrie.
Stahlunternehmen und Anlagenbauer können in vielfacher Hinsicht von additiven Fertigungsverfahren profitieren, wie Aussteller und Expertenvorträge auf der Metec im Rahmen der Bright World of Metals vom 12. bis 16. Juni 2023 in Düsseldorf verdeutlichen.
Als eines von weltweit wenigen Unternehmen bildet die Düsseldorfer SMS group den gesamten Prozess der additiven Fertigung ab. Schon 2017 hat der metallurgische Anlagenbauer mit Partnern die Entwicklung zusammengehöriger Prozesse im industriellen Maßstab begonnen, um die additive Fertigung auch im Serienmaßstab wettbewerbsfähig zu machen. Zum digital gesteuerten Additive Manufacturing Competence Center gehören als Herzstück eine von SMS entwickelte Metallpulververdüsungsanlage mit einer Kapazität von 4.000 Tonnen im Jahr, mit angeschlossener Pulverklassifizierung und dem Pulverhandling. Komplettiert wird das Produktionssystem durch einen großen LPBF Drucker mit einem Bauraum von 400x400x400 mm für die additive Fertigung in Metall, die Nachbearbeitung, Qualitätskontrolle sowie Versand der fertigen Werkstücke. Ein junges Team für Forschung und Entwicklung (F&E) entwirft, fertigt und testet 3D-gedruckte Teile – überwiegend für die eigenen Produkte der SMS group.
Prof. Dr. Hans Ferkel, Chief Technology Officer der SMS group, schätzt die Stärken der additiven Fertigung: Mit größtmöglicher Geometriefreiheit funktionsoptimierte Bauteile fertigen zu können, die mit den klassischen Fertigungsverfahren nicht machbar wären. SMS nutzt additive Fertigung beispielsweise zur Produktion serienmäßiger Anlagenkomponenten. Ein erstes Ergebnis war ein preisgekrönter Sprühkopf für Schmiedepressen, wahlwiese aus Kunststoff oder Metall. Das leichte und dadurch schneller bewegliche Bauteil verkürzt die Fertigungszeit beim Schmieden deutlich und erhöht somit die Wirtschaftlichkeit. Der 3D-gedruckte Sprühkopf besteht nur noch aus einem statt bislang aus 16 Teilen und wiegt gerade einmal ein Zehntel eines konventionellen Sprühkopfs, der rund 80 Kilo auf die Waage bringt. Er besitzt strömungsoptimierte Kanäle und kühlt die Gesenke gezielt und individuell angepasst. Gleichzeitig ist er kostengünstiger, wirksamer und individuell nach Bedarf herstellbar. Der 3D-gedruckte Sprühkopf ist bereits erfolgreich bei Kunden aus der Automobilindustrie im Einsatz.
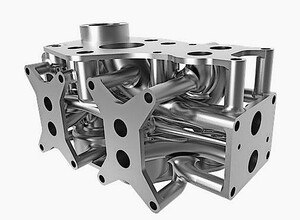
Als weiteres Erfolgsbeispiel führt der SMS-Forschungschef einen strömungsoptimiert konstruierten und additiv gefertigten Hydraulikblock für metallurgische Anlagen an. Ein herkömmlicher Hydraulikblock besteht aus einem Stahlblock mit gebohrten Kanälen, durch die das zur Kraftübertragung eingesetzte Hydrauliköl gepresst werden muss. Die in den Block gebohrten geraden Kanäle treffen zwangsläufig immer auf Stoß aufeinander. Strömungstechnisch ist der eckige Verlauf daher ungünstig. Ein am Computer gerechneter Strömungsverlauf gleicht eher einem Verdauungskanal. Nach dem Vorbild der Natur wurde auf dem Weg zwischen Eingang und Ausgang ein möglichst geringer Druckverlust realisiert. Neu gerechnet und additiv gefertigt erfüllt der Hydraulikblock das strömungstechnische Optimum. Um den erforderlichen Arbeitsdruck im Hydrauliksystem aufzubauen, ist gegenüber dem konventionellen Vorgänger ein deutlich kleinerer Kompressor ausreichend, was eine signifikante Energieeinsparung bedeutet.
Immer mehr Stahlunternehmen nutzen die gesamte Bandbreite der additiven Fertigung. Bei der österreichischen voestalpine erstreckt sich das Geschäft von der Legierungsentwicklung und der Metallpulverherstellung über die Konstruktion und Fertigung bis hin zur Nachbearbeitung. Mit additiver Fertigung bietet die Umformtechniksparte des Konzerns seinen Kunden eine Ergänzung des Technologieportfolios. Speziell im Bereich des Leichtbaus erlaubt der schichtweise metallische Aufbau Bauteile von größerer Designfreiheit und erhöhter Funktionalität schnell und im Idealfall kosteneffizient herzustellen, wie der Stahl- und Technologiekonzern hervorhebt.
Der weltgrößte Stahlkonzern ArcelorMittal arbeitet bereits seit 2017 mit dem auf Metalldruck spezialisieren Hersteller Additive Industries zusammen. Additive Industries sieht sich als das weltweit führende Unternehmen für industriell integrierte, skalierbare Metalldrucker. Im 3D-Metalldruck fertigt ArcelorMittal gebrauchsfertige Ersatzteile nach Bedarf, darunter große Stahlersatzteile für die Stahlerzeugung oder den Bergbau. “Wir begannen mit dem Druck kleiner Exemplare und sind nun zu großen und komplexen Teilen übergegangen“, berichtet Jose López Fresno, Leiter der Abteilung Additive Fertigung von ArcelorMittal.
Den Gießereien bieten additive Verfahren ebenfalls viele Chancen. In Frage kommen hier sowohl der direkte Metalldruck als ergänzendes Verfahren zum Gießen, als auch insbesondere indirekte Verfahren wie der Sanddruck von Formen, Kernen und Modellen.
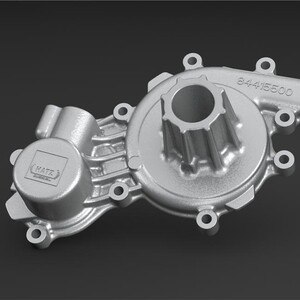
Im direkten Verfahren unterwegs ist beispielsweise die Gießerei FrankenGuss. “Die additive Fertigung ist eine hervorragende Ergänzung klassischer Gießverfahren“, heißt es bei dem Eisen- und Aluminiumgießer aus Kitzingen/D. Mit dem pulverbettbasierten Laserschmelzen von Metallen wirbt FrankenGuss auch für kleine Losgrößen und sogar Einzelstücke. Das Spektrum der Anwendung reicht vom Prototypen bis zu Leichtbauteilen für Luftfahrt und E-Mobilität, oder auch hochbelastbaren Spezialbauteilen ohne breiten Absatzmarkt, z. B. für den Motorsport. Mit Print-on-Demand lassen sich auch einzelne Ersatzteile herstellen, beispielsweise für den Oldtimer-Markt. Über das Abscannen bestehender Teile können diese mittels Reverse Engineering nachproduziert werden, selbst wenn keine Konstruktionsdaten zur Verfügung stehen.
Eine aktuelle Studie unter Beteiligung des Fraunhofer-Instituts für Gießerei-, Composite- und Verarbeitungstechnik IGCV erwartet innerhalb der nächsten vier Jahre ein Wachstum von rund 20 Prozent im Bereich der additiven Fertigung. Vor allem bei vergleichsweise geringen Stückzahlen, z. B. wenn eine komplizierte Geometrie und ein hoher Individualisierungsgrad gefordert sind, haben sich die additiven Verfahren bereits erfolgreich behauptet. Bislang waren das vor allem im Werkzeugbau, der Luft- und Raumfahrt oder bei medizinischen Produkten der Fall.
Der Industrialisierungsgrad additiver Verfahren schreitet voran und mit dem Laserschmelzen von Metall gewinnen generative Fertigungsverfahren auch als vollwertige Fertigungstechnologien an Bedeutung. “Wir sind im Bereich der Serienfertigung angekommen“, bestätigt Dr.-Ing. Wolfram Volk, Professor an der TU München und geschäftsführender Leiter des Fraunhofer-Instituts für Gießerei-, Composite- und Verarbeitungstechnik IGCV. Ein Verfahren wie das selektiven Laserschmelzen (SLM) von Metall sei aber eher bei kleineren Bauteilen wirtschaftlich. Professor Volk verweist auf das Beispiel der Automobilindustrie, wo bereits Stückzahlen im Bereich 1000 bis 2000 Bauteile additiv gefertigt werden.
“Additive Fertigung kann die Angebote einer Gießerei signifikant verändern“, sagt Professor Volk. In der Gießereiindustrie sieht der Experte erhebliches Potenzial für den 3D-Druck vor allem bei indirekten Verfahren wie dem Sanddruck von Formen, Kernen und Modellen mittels Binder-Jetting. Beim Sand-Binder-Jetting werden Kerne und Formen schichtweise aus Sand aufgebaut, der mit einem aushärtenden Binder zusammengehalten wird. Der richtige Binder spielt dabei eine Schlüsselrolle. Gießereichemieunternehmen wie Hüttenes–Albertus, Reinsicht oder ASK haben daher spezielle Bindersysteme entwickelt, die genau auf die Anforderungen von additiv gefertigte Formen und Kernen abgestimmt sind.
Der eigentliche Gussvorgang bleibt beim Sand-Binder-Jetting unverändert. Diese nahtlose Integration in die klassischen Produktionsverfahren des Gießens sind ein entscheidender Vorteil gegenüber der direkten additiven Fertigung in Metall, auch im Prototypenbau. Die Eigenschaften additiv gefertigter Bauteile sind signifikant andere als von gegossenen Komponenten. Laserschmelzen von Metall zur Protoypenteilfertigung zu nutzen, ist daher sehr beschränkt. “Das direkte Verfahren lässt sich nutzen, um ein Demonstratorbauteil herzustellen, aber das geht meistens auch über indirekt additiv gefertigten Bauteile“, hebt Experte Volk hervor.
Komplexitätsgrad und Filigranität beim Binder-Jetting werden mit den herkömmlichen Gießverfahren nicht erreicht. Durch den Wegfall des Modellbaus verkürzt der Einsatz eines Sanddruckers deutlich die Herstellungszeiten von Gussbauteilen. Die Fertigung von Sandformen und -kernen oder Feingussmodellen ist in nur wenigen Stunden möglich. Das kann je nach Komplexitätsgrad eine Zeiteinsparung von mehreren Wochen bedeuten.
Im Gießereitechnikum des Fraunhofer IGCV arbeiten Volk und sein Team mit verschiedenen Anlagenherstellern zusammen. Gemeinsam mit den Experten des IGCV hat der Druckerhersteller Voxeljet in einem Projekt einen Sanddrucker entwickelt, der Formen für bis zu 80 t schwere Bauteile fertigen kann, etwa für Windenergieanlagen. “Die Skalierung der Technologie ist erfolgreich, die Wirtschaftlichkeit muss allerdings noch gezeigt werden“, berichtet Volk. Dem Vorteil der Nahtfreiheit gegenüber zusammengebauten Formen steht der Nachteil der technologische Aufwand der Skalierung der Anlage gegenüber.
Eine Alternative zum Drucken einer Großform ist das so genannte Stapel- oder Voxelgießverfahren, das auch am IGCV erforscht wird. Hierbei wird nicht eine große Form gedruckt, sondern einzelne Segmente, die dann wie ein 3-D-Puzzle wieder zusammengefügt werden. “Mit dem Stapel-Voxelguss haben wir sehr glatte Flächen, die man automatisiert zusammenbauen kann“, erläutert Prof. Volk, der in dem Verfahren eine sehr große Chance sieht. “Hier können wir mit dem automatisierten Zusammenbauen der Kernpakete, dem Abgießen und dem automatisierten Entgraten mit Robotern ein sehr wirtschaftliches Verfahren erreichen, mit dem wir sehr große Bauteile realisieren können.”
Was heutige Sanddruckverfahren zu leisten vermögen, lässt sich am Beispiel Hetitec verfolgen. Die finnische Gießerei kann mithilfe des 3-D-Drucks von Sandformen und Kernen komplexe Gussteile bis zu 600 kg innerhalb weniger Tage fertigen. Das macht sie nach eigenen Angaben zur schnellsten Gießerei Finnlands. Mit diesem hybriden Ansatz des Printed Casting lässt sich die Geometriefreiheit des 3D-Druck mit dem Kostenvorteil des konventionellen Gießens kombinieren. Ein weiterer Vorteil: Gegenüber direkten metallverarbeitenden additiven Technologien verfügt der Metallguss über eine deutlich größere Materialvielfalt. Neben Eisenlegierungen kann Hetitec auch verschiedene spezielle Stahl- und Aluminiumlegierungen vergießen.
Was Tempo in der Praxis bedeutet, verdeutlicht das Unternehmen gern am Beispiel eines havarierten Eisbrechers. Das Schiff lag mit Motorschaden vor der kanadischen Küste, die übliche Lieferzeit für das benötigte Ersatzteil hätte fünf Monate betragen. Die Reederei wandte sich mit einem 2D-Konstruktionsplan des Bauteils an die finnische Gießerei, wo die Zeichnung innerhalb einer Stunde in eine 3D-CAD-Datei umgewandelt wurde. Am darauffolgenden Montag begann die Produktion mit dem 3D-Druck der Sandformen und am Freitag derselben Woche war das bearbeitete, fertige Gussteil auf dem Weg nach Kanada.
Das Sand-Binder-Jetting-Verfahren beschränkt sich nicht im Druck von Formen, Kernen und Modellen. Gießereiexperte Volk sieht auch in einer Verbindung von additiver Fertigung und Gießen erhebliches Potenzial. „Hybridfertigung, also das Eingießen von additiv gefertigten Bauteilen als Einlegeteil macht Sinn, um damit den Komplexitätsgrad zu steigern. Hier sehe ich das größte Potenzial bei den gebauten Sandgießverfahren.“ Mögliche Anwendungsfelder seien neben der Automobilindustrie (z.B. Batteriewannen) auch im Bereich Robotik oder der Medizingerätetechnik zu sehen.
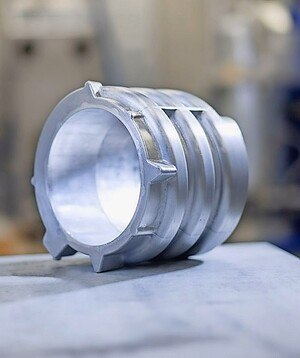
Das Eingießen von Bauteilen wird seit Jahren erprobt. Erfolgreich beispielsweise am Fraunhofer IFAM in Bremen, wo mit der sogenannten Castronics-Technologie das direkte Eingießen elektronischer Sensoren und adaptronischer Funktionselemente im Druckgussverfahren entwickelt wurde. Mit der Verbindung von Druckgießen und additiver Fertigung konnte das IFAM vor zwei Jahren einen E-Motor-Gehäuse mit eingegossenem Kühlkanal vorstellen.
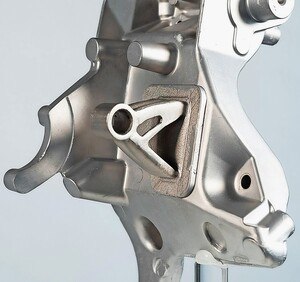
In einem weiteren Forschungsprojekt haben die Fraunhofer-Institute IWS und IWU hybride Fertigungsketten für automobile Anwendungen untersucht. Gemeinsam mit dem Autozulieferer Edag Engineering und der Gießerei Trimet Automotive (heute Bohai Trimet) wurde das Ein- bzw. Angießen von additiv erzeugten metallischen Bauteilen untersucht. Ziel des Forschungsprojekts CastAutoGen war es, den beim Gießen entstehenden Kostenvorteil (Skaleneffekt) zu nutzen, um auch bei größeren Stückzahlen mit additiver Fertigung eine bessere Wirtschaftlichkeit zu erzielen. Durch das Eingießen additiv gefertigter metallischer Komponenten, z.B. als Wärmetauscher oder als Verstärkung, lässt sich die Funktionalität eines Bauteils erhöhen. Damit steigen zwar auch die Herstellkosten gegenüber einem reinen Druckgussbauteil, liegen aber deutlich unterhalb einer rein additiven Fertigung.
In einem weiteren Forschungsprojekt haben die Fraunhofer-Institute IWS und IWU hybride Fertigungsketten für automobile Anwendungen untersucht. Gemeinsam mit dem Autozulieferer Edag Engineering und der Gießerei Trimet Automotive (heute Bohai Trimet) wurde das Ein- bzw. Angießen von additiv erzeugten metallischen Bauteilen untersucht. Ziel des Forschungsprojekts CastAutoGen war es, den beim Gießen entstehenden Kostenvorteil (Skaleneffekt) zu nutzen, um auch bei größeren Stückzahlen mit additiver Fertigung eine bessere Wirtschaftlichkeit zu erzielen. Durch das Eingießen additiv gefertigter metallischer Komponenten, z.B. als Wärmetauscher oder als Verstärkung, lässt sich die Funktionalität eines Bauteils erhöhen. Damit steigen zwar auch die Herstellkosten gegenüber einem reinen Druckgussbauteil, liegen aber deutlich unterhalb einer rein additiven Fertigung.
Eine wirtschaftliche Mehrwertgenerierung durch die Kombination von Druckguss und additiver Fertigungsmethoden konnte am Beispiel des Eingießens eines verstärkenden Kernbauteils aus einer Chrom-Nickel-Molybdän-Legierung in ein Aluminiumbauteil dargestellt werden. Mit Hilfe von metallischen Einlegern und Verstärkungen sowie dem Laserauftragsschweißen wurde ein Nebenaggregate-Halter von Audi in Aluminium-Druckgussbauweise zu einem variantenintensiven, funktionsintegrierten Produkt mit bestmöglicher Leistung weiterentwickelt.
Das Ergebnis hat Potenzial, beispielsweise für elektrische Antriebsstränge. Auch für Produkte mit kleinerer Stückzahl wie High-performance Fahrzeugen die neue hoch-funktionsintegrierte Bauteile erfordern, kann die Kombination von additiver Fertigung und Druckguss ein zukunftweisendes Fertigungsverfahren darstellen.
[Autor: Gerd Krause, Mediakonzept Düsseldorf]