Die gängigsten Pressschweißverfahren im Überblick
Im Metallbau kommen je nach Umständen und verwendeten Materialien vielfältige Schweißverfahren zum Einsatz. Neben den klassischen Schmelzverfahren bietet vor allem das Pressschweißen eine Reihe an Möglichkeiten und Varianten, bei denen die Werkstücke allein durch Wärme und Druck verbunden werden.
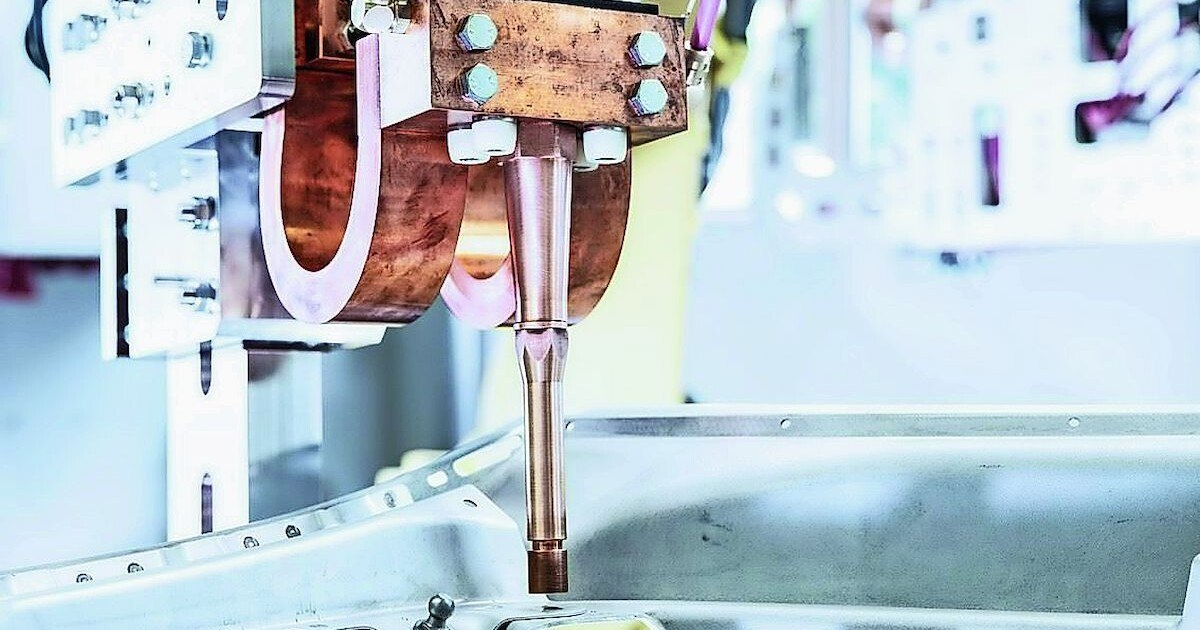
Neben den im Metallbau vorwiegend eingesetzten bekannten Schmelzschweißverfahren existieren vielfältige Varianten des Pressschweißens. Dazu gehören das zumeist im Fahrzeugbau vorkommende Widerstandsschweißen, das Reibschweißen, das Bolzenschweißen sowie Sonderverfahren wie Diffusionsschweißen, Ultraschallschweißen oder Sprengschweißen. Die Gruppe der Pressschweißverfahren hat eines gemeinsam: Die Verbindung der Werkstücke erfolgt durch Wärme und Druck (Pressen). Die Wärme kann dabei entweder durch elektrischen Strom (Widerstandsschweißen) oder durch Reibung (Reibschweißen) erzeugt werden.
Die Prozesse des Widerstandspressschweißens unterteilen sich in Punktschweißen, Buckelschweißen und Rollennahtschweißen. Die bekannteste Variante ist das Punktschweißen. Es geht schnell, meistens beträgt die Schweißzeit nur wenige Millisekunden. Bei diesem Verfahren werden zwei, manchmal auch drei Bleche an einem Punkt, durch Elektroden, zusammengepresst und dabei ein Schweißstrom in die Blechteile “gejagt”. Diese schmelzen auf, nach dem Erstarren der Schmelze entsteht die unlösbare Verbindung.
Das Buckelschweißen ist ebenfalls eine sehr leistungsstarke Variante des Widerstandspressschweißens und funktioniert im Prinzip wie das Punktschweißen. Es bietet Vorteile für die Automation, da mehrere Punkte während eines Arbeitsgangs geschweißt werden können. In einem der Bauteile werden Erhöhungen (Schweißbuckel) angebracht. Durch die Geometrie des Buckels ist der Stromfluss genau definiert, denn nur die Buckel liegen auf dem zu verschweißenden Bauteil auf. Im Gegensatz zum Punktschweißen werden hier flache Kupferelektroden verwendet. Während des Schweißvorganges schmilzt der Buckel teilweise auf und bildet eine feste Verbindung mit dem angedrückten Bauteil. Man kann auch “natürliche” Buckel für diese Schweißvariante nutzen, etwa wie sie bei Gittern vorhanden sind.
Beim dritten Verfahren (Rollennahtvariante) pressen die rollenförmigen Elektroden die Bleche zusammen und leiten den Schweißstrom konzentriert in die Werkstücke. Damit lassen sich gas-, flüssigkeits- und druckdichte Nähte erzeugen, die etwa bei Kraftstofftanks und Behältern gefordert werden.
Hinsichtlich der Schweißbarkeit der Werkstoffe ist Aluminium im Gegensatz zu den Stahlwerkstoffen eine besondere Herausforderung. Für diese “Fälle” hat Fronius die beiden Punktschweißsysteme DeltaSpot und DeltaCon entwickelt. Delta-Con sind Zangen für das konventionelle Punktschweißen von Aluminium. Im Vergleich zu Stahl weist Aluminium einen geringeren Widerstand auf, wodurch höhere Kräfte und größere Stromstärken zum Verbinden der Materialien erforderlich sind. Bei den Schweißzangen verhindert ein spezieller Zangenausgleich noch vor dem Schweißvorgang, dass sich die Bleche durch Ungenauigkeiten bei der Einstellung bleibend verformen. Zudem lässt sich der Prozess überwachen.
Die DeltaCon-Zangen sind modular aufgebaut, damit kann man viele Schweißaufgaben lösen, ohne teure Lagerhaltungskosten für verschiedene Bauteile. Die schmale Bauweise erleichtert auch die Zugänglichkeit bei beengten Platzverhältnissen. Für die automatisierte Fertigung können die Delta-Con-Zangen an verschiedene Robotertypen angebunden werden. Die Programmierung der Schweißzangen erfolgt über eine grafische Oberfläche.
Das Punktschweißsystem DeltaSpot ist genau dann richtig, wenn Stahl-Aluminium- sowie Dünn- und Mehrblechverbindungen gefordert sind. Das System spielt seine Vorzüge bei Werkstücken “mit einer hohen Punktzahl” aus, denn mit DeltaSpot lassen sich bis zu 7.000 Punkte ohne Unterbrechung fügen. DeltaSpot kommt vor allem für anspruchsvolle Blechverbindungen zum Einsatz, die absolut präzise und hundertprozentig reproduzierbare Schweißergebnisse erfordern. Neben Aluminium und Stahl lassen sich mit DeltaSpot auch Titan, Magnesium, Edelstahl, beschichtete Stahlbleche und hochfeste Stähle fügen.
Als Kaltpressverschweißen bezeichnet man das Phänomen, vorwiegend metallische Werkstücke gleichen Materials bereits bei Raumtemperatur so miteinander verbinden zu können, dass die Verbindung dem “normalen” Verschweißen sehr nahekommt; daher rührt auch die Bezeichnung. Dieses Phänomen wurde bereits in den 1940er Jahren entdeckt. Verbindungen mittels Kaltpressschweißen erfolgen unter hohem Druck und unterhalb der Rekristallisationstemperatur der Einzelteile. Die beiden Teile bleiben in festem Zustand, allerdings ist eine plastische Verformung mit einer starken Annäherung der Kontaktflächen notwendig. Durch die enge Berührung erfolgt eine stabile Verbindung der beiden Werkstücke. Für eine gute Verbindung braucht man Materialien mit ausreichender Kaltverformbarkeit (Kupfer, Aluminium).
Das Ultraschallschweißen ist ein Verfahren zum Fügen von thermoplastischen Kunststoffen und metallischen Werkstoffen. Bei den metallischen Werkstoffen kommt es vor allem bei Aluminium, Kupfer und deren Legierungen zum Einsatz. Die Verschweißung wird durch eine hochfrequente mechanische Schwingung erreicht, welche zwischen den Bauteilen zu Erwärmung führt. Beim Ultraschallschweißen von Metallen wird die Schwingung zu den Fügepartnern “eingeleitet”, dass diese aneinander reiben. Danach entsteht eine feste Verbindung. Dies geschieht durch plastisches Fließen, ohne dass die Materialien schmelzen, was insbesondere bei dünnen Blechen vorteilhaft ist. Neben punktförmigen Schweißungen sind auch Nahtschweißungen möglich. Es lassen sich unterschiedliche Werkstoffe fügen, die Erwärmung ist sehr gering.
Mithilfe des Sprengschweißverfahrens ist es möglich, zwei nicht schmelzschweißbare Materialien zu verbinden. Dabei prallen die beiden Schweißflächen unter Zuhilfenahme von Sprengstoff mit mindestens 100 m/s unter einem Winkel von 2 bis 30 Grad aufeinander. Die Kollisionsenergie bringt die Schweißpartner bis zur atomaren Ebene zusammen, so dass auch die Gitterkräfte (bei Metallen) wirken. Da die Schmelztemperatur nicht erreicht wird, können sich keine intermetallischen Phasen bilden. In der industriellen Anwendung werden auf diese Art meist zwei auf konventionelle Weise nicht schweißbare Metallpartner miteinander verbunden, beispielsweise Titan und Kupfer. Als Sprengstoffe kommen vorwiegend hochbrisante plastische Sprengstoffe mit Detonationsgeschwindigkeiten von mehr als 5.000 m/s zum Einsatz. Durch den Aufprall der Schweißpartner entstehen an den Grenzflächen wellenartige Verwerfungen, die eine stoffschlüssige Verbindung herstellen.
Mit dem Elektromagnetischen Pulsschweißen/EMP-Schweißen kann das sehr schnell gehen. Artgleiche oder verschiedene Werkstoffe werden in Sekundenbruchteilen verbunden, indem eine der Flächen durch ein Magnetfeld einen Impuls erhält und gegen den anderen Fügeteil prallt. Das geht rasant schnell. Mindestens eine der Flächen muss dazu aus einem gut leitfähigen Metall wie Aluminium bestehen. Denn für die Verbindung sorgt ein sehr hoher Wechselstromimpuls, der nahe der Verbindungsstelle auf das Metall gerichtet wird. Wie beim Sprengschweißen kommt es zu einer stoffschlüssigen Verbindung in einer festen Phase. Da diese Methode kaum Wärme in die Bauteile einbringt, lassen sich metallische Werkstoffe mit stark unterschiedlichen Schmelzpunkten verschweißen, ohne dass sich das Gefüge in der Festigkeit verändert. Aufgrund der eher aufwendigen Anlage ist EMPT-Schweißen zwar vorwiegend für die serielle Massenfertigung geeignet. Doch die geringen Wartungsintervalle von bis zu zwei Millionen Impulsen lassen die Kosten etwa bei Stahlrohrverbindungen in den Cent-Bereich sinken.
Das Diffusionsschweißen erlaubt das Verbinden von Metallteilen ohne Zusatzwerkstoffe. Ein enger Kontakt zwischen den Fügeteilen und hohe Temperatur regen das Kornwachstum zwischen den Bauteilen an, somit wird eine fugenlose Verbindung erzeugt. Das Verfahren kann für große als auch für Mikrobauteile eingesetzt werden. Die Vorteile: Sehr hohe Festigkeit, die Fügestelle ist makro- und mikroskopisch nicht zu erkennen, kein Korrosionsangriff an der Fügestelle, großflächige Verbindungen mit geringem Materialverzug, metallisch blanke Bauteile nach dem Fügeprozess. Es sind Werkstoffverbunde möglich (z.B. Kupfer und Wolfram). Die Palette an bereits erfolgreich diffusionsgeschweißten Werkstoffverbunden ist vielfältig: Kupfer, Stähle, Edelstähle, Molybdän und Titan. Ebenso Verbunde aus hochlegierten und niedrigschmelzenden Aluminiumwerkstoffen. Mittels Diffusionsschweißen lassen sich schwierige Fügeaufgaben lösen, die mit konventionellen Methoden nicht mehr realisiert werden können.
Das MBP-Schweißen (Pressschweißen mit magnetisch bewegtem Lichtbogen) wird auch als Magnetarc-Schweißen bezeichnet. Mit dem Verfahren werden Hohlprofile unter Schutzgas stumpf verschweißt. Die eingespannten Bauteile werden in Kontakt gebracht. Dann wird der Schweißstrom zugeschaltet, der Lichtbogen gezündet und dieser mit einem Magnetfeld in Rotation versetzt. Der rotierende Lichtbogen erwärmt die Schweißfläche. Ein Stauchvorgang verbindet dann die Bauteile miteinander. Beim Magnetarc-Schweißen können Hohlprofile mit Wandstärken von 1 bis 10 mm, sowie Rohrdurchmesser bis 140 mm verbunden werden. Diese Technologie bietet sehr kurze Schweißzeiten, ein Zusatzwerkstoff ist nicht nötig. Der Verzug ist gering, die Reproduzierbarkeit hoch. Voraussetzung für dieses Schweißverfahren: leitfähige, anschmelzbare Bauteile. Dazu eigen sich Werkstoffe wie unlegierte und legierte Stähle, Gusseisen und Stahlguss. Bei oberflächenbeschichteten (verzinkten oder verchromten) Fügeteilen müssen die Stoßflächen unbeschichtet sein. Anlagen zum Magnetarc-Schweißen bietet etwa der Roboterhersteller Kuka an.
Beim Reibschweißen erfolgt die Erwärmung der Bauteile durch mechanische Reibung. Diese wird durch eine Relativbewegung zwischen einem drehenden und einem feststehenden Fügeteil erzeugt. Unter hoher Krafteinwirkung, aber ohne Zusatzwerkstoff, werden die Teile sicher miteinander verbunden. Das Reibschweißen zeichnet sich allgemein durch eine hohe Produktivität, einfache Automatisierbarkeit und hohe Qualität der Verbindung aus. Durch die Reibung kommt es zur Erwärmung und Plastifizierung des Werkstoffes, aber nicht zur Aufschmelzung. Am Ende des Reibvorganges wird die Relativbewegung abgebremst und ein erhöhter Stauchdruck aufgebracht. Dadurch sind die Teile verschweißt, und es entsteht ein feinkörniges, hochfestes Schmiedegefüge.

In vielen Bereichen ist das Reibschweißen bereits etabliert, erobert aber laufend neue Anwendungsgebiete. Neben herkömmlichen Metallen eignet sich das Reibschweißen besonders zum Verbinden von Sonderwerkstoffen und von Mischverbindungen, die sich mit Schmelzschweißverfahren nicht oder nur eingeschränkt herstellen lassen. So zum Beispiel Verbindungen mit hochkohlenstoffhaltigen Stählen, hochfeste Verbindungen mit temperatursensiblen Stählen, NE-Werkstoffen oder Leichtbau-Mischverbindungen, wie Aluminium/Stahl, Aluminium/Kupfer oder Titan/Stahl. Das Reibschweißen ist durchaus für Lohnbetriebe mit kleinen und mittleren Losgrößen wirtschaftlich interessant. Nachfolgend ein kurzer Überblick zu den Verfahrensvarianten: Rotationsreibschweißen, Orbitalreibschweißen sowie Rührreibschweißen.
Das Rotationsreibschweißen ist weit verbreitet für das Fügen im Rohrleitungsbau. Der große Vorteil dieses Verfahrens liegt auch darin, dass man nicht nur gleich, sondern auch unterschiedliche Materialien miteinander formschlüssig und sicher verbinden kann, wie Aluminium und Stahl. Die einzige Voraussetzung: Einer der zu fügenden Teile muss rotationssymmetrisch sein. Das Verfahren läuft folgendermaßen ab: Ein Werkstück wird in Rotation gebracht, gleichzeitig presst man das andere Bauteil mit einem definierten Druck dagegen. Durch Rotation und den gleichzeitigen Druck erwärmen sich die Berührungsflächen, es kommt zur “Reibphase”. Die Rotation wird beendet und der Druck noch einmal erhöht. Der plastifizierte Werkstoff kann so mit dem anderen Bauteil verbunden werden. Danach können die Werkstoffe langsam abkühlen.
Mit dem Orbitalreibschweißen können auch im Gegensatz zum nahe verwandten Rotationsreibschweißen nicht runde Querschnitte und nicht drehbare Teile reibgeschweißt oder mehrere Verbindungen in einem Arbeitsgang hergestellt werden. Die Teile führen keine Drehung zueinander aus. Das Verfahren wird erst seit wenigen Jahren speziell in der Zulieferindustrie für Serienteile eingesetzt. Verbinden kann man eckige Hohlprofile, Strangpressprofile oder Gehäuseteile aus Stahl, Aluminium, Kupfer, Messing und Titanlegierungen.
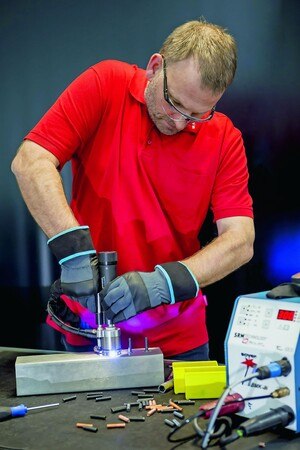
Das Rührreibschweißen ist ein Verfahren um Aluminiumbleche, Aluminium-Stahl-Mischverbindungen, Kupfer- oder Titanlegierungen miteinander zu verbinden. Hierbei werden nicht wie beim Rotationsreibschweißen die Werkstücke bewegt, sondern es wird ein rotierender Dorn durch den Spalt der zu verbindenden Teile geführt. Das Rührreibschweißen von Aluminium zeigt hohe Festigkeitswerte, und es treten keine Poren oder Verunreinigungen auf. Die von Stirtec durchgeführten Zug- und Biegetests waren sehr positiv. Die Daten der Dauerfestigkeitstests waren sogar besser als bei anderen Schweißverfahren. Außerdem ist die Naht weitgehend spannungsarm. Das Rührreibschweißen eignet sich gut für das Verbinden von Strangpreßprofilen und flachen Platten in einem Wanddickenbereich von 1,6 mm bis 30 mm. Verwendung findet das Verfahren hauptsächlich bei eher großflächigen Bauteilen im Stahlbau sowie mittlerweile auch verstärkt bei kleineren Losgrößen im Behälterbau. Experten und Anlagen für die Reibschweißverfahren findet man bei Kuka und Stirtec.
Täglich werden Millionen von Bolzen, Hülsen oder Stiften mit dem Bolzenschweißverfahren an Bleche, Rohre oder Profile aufgeschweißt. Bolzenschweißen ist ein “altes” Verfahren. Ted Nelson, ein Schweißer der US-Marine, entwickelte es 1939. Damit konnte er bei den großen Schiffen zeitsparend Tausende Gewindebolzen auf die Stahlplatten schweißen. Seit damals hat sich das Verfahren rasch auf viele andere Branchen ausgebreitet. Bolzenschweißen ist heute im Fahrzeugbau praktisch Standard, ebenso gut geeignet im Metallbau, bei Stahlkonstruktionen oder für hochwertige Schweißverbindungen im Fassadenbau.
Zwischen Bolzen und Werkstück wird ein Lichtbogen erzeugt, der beide Teile anschmilzt. Sekundenbruchteile später taucht der Bolzen in die Schmelze ein, der Schweißstrom wird abgeschaltet, die Schmelze erkaltet und die vollflächige, formschlüssige Verbindung “steht”. Die Vorteile: Keine Bohrungen, Schrauben oder Nieten, die bei Hohlkörpern eventuell zu Undichtigkeiten führen können, kaum Verzug aufgrund der extrem kurzen Schweißzeit und keine mühsame Nacharbeit. Es können Werkstoffe wie unlegierter oder legierter Stahl, Edelstahl, verkupferter Stahl und Aluminium miteinander verschweißt werden. Dabei können die Bolzendurchmesser zwischen 2 und 25 mm liegen und die Bleche sehr dünn sein, etwa 1 bis 3 mm. Die zum Bolzenschweißen notwendige Ausrüstung liefern Anbieter wie HBS, Köco, Nelson und Soyer: tragbare, akkubetriebene Handschweißgeräte für den mobilen Einsatz bis zu teil- und vollautomatisierten CNC-Bolzenschweißanlagen. Dazu auch eine große Vielfalt genormter Schweißbolzen. Neben den Standardlösungen können die meisten Anbieter auch individuell anwendungsbezogene Systeme konfigurieren. Die aktuellen Bolzenschweißgeräte sind bestens ausgestattet mit moderner Technik: digitaler Prozesskontrolle, vorab abgespeicherten Schweißparametern, Mikroprozessorsteuerung, Einknopfbedienung, einem 4-Zoll-Grafik-Display und Software. Die Mehrstellentechnik erlaubt den gleichzeitigen Anschluss von bis zu vier Schweißpistolen für unterschiedliche Bolzen. Damit kann man auf das “in-mehreren-Durchgängen-Schweißen” verzichten.
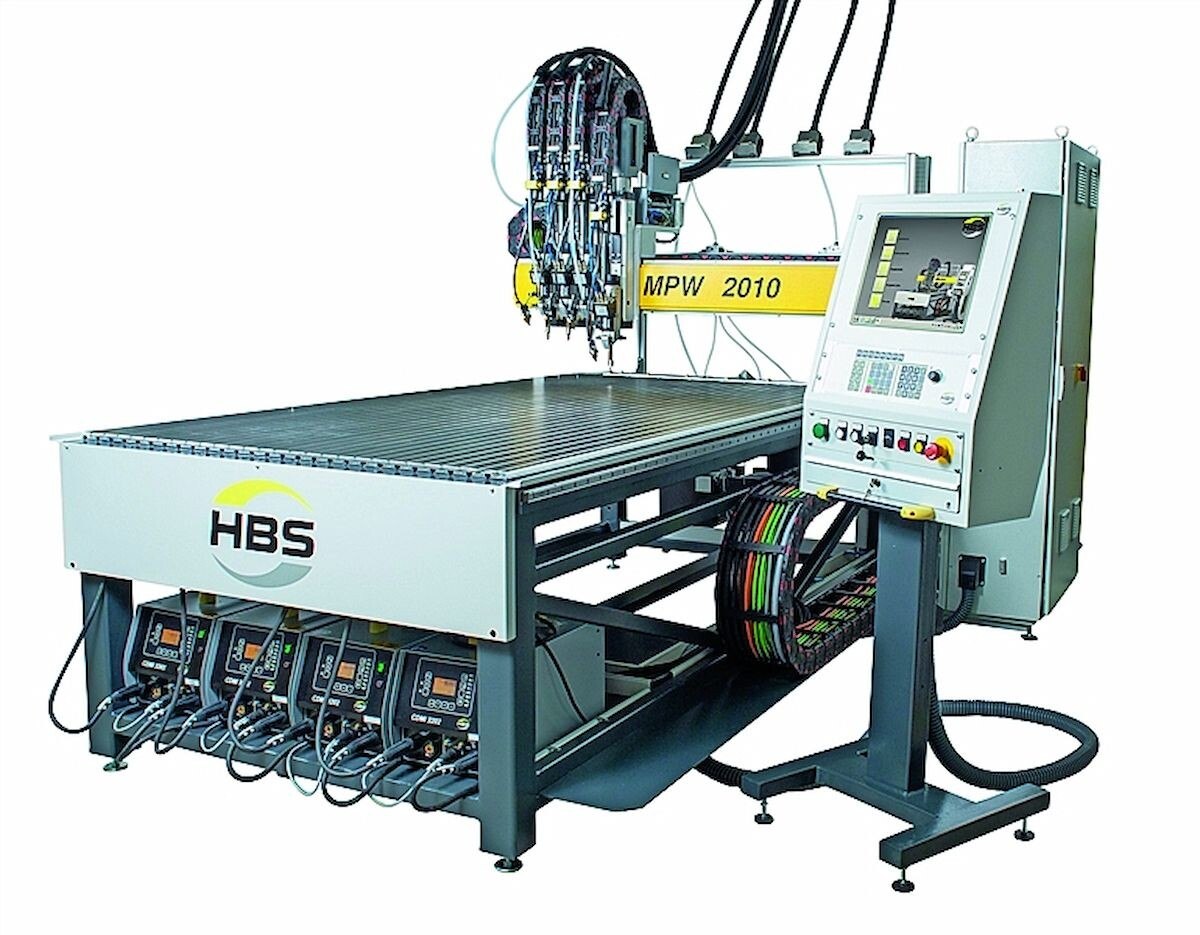
Soyer hat mit der SRM-Technologie (Magnetfeld-Bolzenschweißen) das Bolzenschweißen weiterentwickelt. Dabei können Bolzen mit besonders großem Durchmesser (bis M16) auch auf dünne Bleche geschweißt werden. Möglich ist ein Verhältnis bis zu 1:10 von Blechdicke zum Bolzendurchmesser, bisher wurde 1:4 erreicht. Außerdem bietet das patentierte SRM-Verfahren laut Soyer noch weniger Bolzenabbrand und Verzug des Werkstücks sowie eine deutliche Reduzierung bei Einbrandtiefe, Schweißzeit sowie Energie. Obwohl der Vergleich nicht ganz zulässig ist, könne man laut Soyer mit der SRM-Technologie oft Verfahren wie Kleben, Nieten oder Schrauben ersetzen. Speziell beim automatisierten Bolzenschweißen mit größeren Serien ist es die kostengünstigste Verbindungstechnik zum Befestigen von Bauteilen. Auf dünnen Blechen kann es auch oft die einzige technische Lösung sein.
[Quelle: METALL 12/2019]