Edelstahl ist nicht gleich Edelstahl
Über die Jahre haben sich diverse Bezeichnungen für Edelstahl und mehr als 250 verschiedene Edelstahlsorten etabliert. Jedoch ist Edelstahl nicht gleich Edelstahl. Je nach Produkt, Einsatzgebiet und Verarbeitung sollte jener Edelstahl eingesetzt werden, der die besten Voraussetzungen bietet und mit dem man die gewünschten Ergebnisse erzielt. Wissenswertes zur Verarbeitung von Edelstahl in der Spenglertechnik.
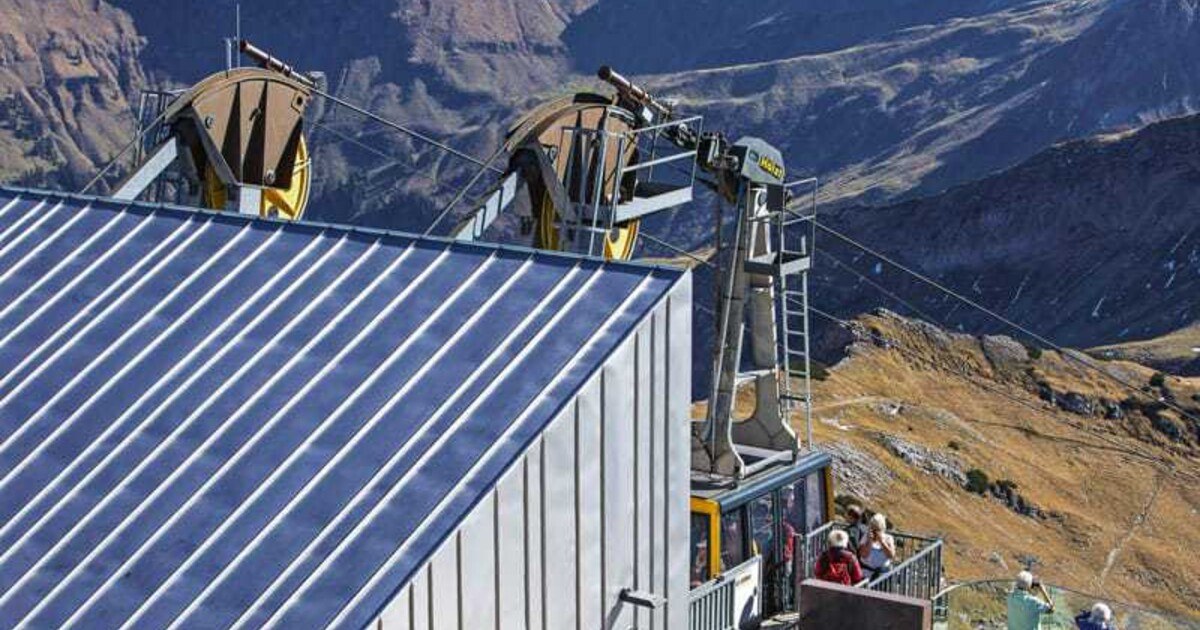
-
© Battisti / Dietmar Walser -
© Battisti / Dietmar Walser -
© Battisti / Dietmar Walser -
© Battisti / Dietmar Walser -
© Battisti / Dietmar Walser -
© Battisti / Dietmar Walser -
© Battisti / Dietmar Walser -
© Battisti / Dietmar Walser
Schon vor mehr als 5.000 Jahren lernten die Menschen aus verschiedenen Kulturkreisen die Gewinnung von Eisen aus Erz. Das damals seltene und sehr wertvolle Material wurde hauptsächlich zur Verarbeitung von Schmuck, Kultgegenständen oder Waffen verwendet. Jedoch hat Eisen einen entscheidenden Nachteil: Es neigt an feuchter Luft, im Wasser und in der nassen Erde zu Korrosion und ist somit nicht beständig.
Erst im 18. Jahrhundert wurden die drei Metalle entdeckt, die man zur Herstellung von Edelstahl benötigt, nämlich Nickel, Molybdän und schlussendlich Chrom. 100 Jahre später, genauer im Jahr 1912, gelang es erstmals durch die Kombination von Nickel und Chrom in Verbindung mit einer genau dosierten Wärmebehandlung ein rostresistentes Material mit gleichzeitig guten mechanischen Eigenschaften zu erzeugen. Das Material Edelstahl war geboren. Benno Strauß und Eduard Maurer aus Deutschland erhielten bei Krupp das erste Patent auf Edelstahl. Die Erfolgsgeschichte von Edelstahl, mit seinen fast unendlichen Einsatzmöglichkeiten und Vorteilen, nahm seinen Lauf.
Welche Edelstähle gibt es?
Über die Jahre haben sich diverse Bezeichnungen für Edelstahl und mehr als 250 verschiedene Edelstahlsorten etabliert. Jedoch ist Edelstahl nicht gleich Edelstahl. Die Vielzahl von Edelstahl-rostfrei-Sorten ist in ganz bestimmten Legierungsvarianten auf spezielle Anwendungen zugeschnitten. Gängige Namen und Marken sind unter anderem Chromstahl, Cr/Ni-Stahl, 18/8, Niro, Uginox, Inox, 304, V2A oder auch 1.4301. Die Bezeichnung V2A war eine Bezeichnung zu der Zeit, als die Testmannschaft von Krupp die Legierungen erprobten, somit steht V2A für Versuch 2 Austenit. Inox, 304 und AISI sind amerikanische Bezeichnungen für Edelstahl. Die Angabe 1.4301 bezeichnet nach der deutschen DIN-Verordnung eine bestimmte Sorte von Edelstahl und teilt dem Material im industriellen Einsatz eindeutige Eigenschaften zu. Es gibt somit nicht den einen Edelstahl. Je nach Produkt, Einsatzgebiet und Verarbeitung muss der Edelstahl eingesetzt werden, der die besten Voraussetzungen bietet und mit dem man die gewünschten Ergebnisse erzielt.
Aus den mehr als 250 verschiedenen Edelstahlsorten ergeben sich vier Hauptgruppen der Edelstähle: ferritische, martensitische, austenitische und ferritisch-austenitische Stähle. In der Spenglertechnik kommen austenitische und ferritische, also korrosionsbeständige bzw. korrosionsträge, Stähle zum Einsatz. Ferritische Edelstähle sind das Basismaterial von verzinnten Edelstählen und werden hauptsächlich in der Automobilindustrie, Bedachung und in der Hausgeräteindustrie eingesetzt. Austenitische Stähle sind die meistgenutzten Stähle und werden zur Produktion von 1.4301- und 1.4404-Legierungen verwendet. Martensitische Stähle finden ihre Anwendung in der Herstellung von Werkzeugen. Die ferritisch-austenitischen Stähle sind das bevorzugte Material für spezielle Anforderungen, etwa im Schiffsbau oder in der Erzeugung von Rohren. Sie zeichnen sich durch besondere Härte aus.
Was macht Edelstahl einzigartig?
Der Werkstoff definiert sich durch seine Legierung und durch seine Oberfläche. Legierungen sind Stoffgemische von zumeist zwei oder mehreren Metallen, die andere Eigenschaften aufweisen als die sie bildenden reinen Metalle. Die Legierung bestimmt den Einsatzort, die Verarbeitung und die gewünschte Korrosionsbeständigkeit für ein Produkt bzw. Bauwerk. Sie wird beeinflusst von den Legierungselementen Chrom, Nickel und Molybdän und deren Mischverhältnis. Der Begriff Edelstahl bezieht sich immer auf legierte Stähle mit besonderem Reinheitsgrad. Im Alltag werden gemeinhin nur rostfreie Stähle als Edelstähle bezeichnet. Rostfreie Stähle zeichnen sich durch einen Kohlenstoffanteil von weniger als 1,2 Prozent und einem Chromgehalt von mindestens 10,5 Prozent aus. Letzterer ermöglicht eine kontinuierliche Bildung von Chromoxid an der Oberfläche, das dauerhaft vor Rost schützt. Durch Zufügen von Nickel, Molybdän, Titan, Niob, Mangan oder anderen Elementen können die Einsatzbereiche optimiert werden.
Die Oberfläche des Edelstahls bestimmt dessen optische Erscheinung sowie die Mattheit oder Reflexion. Mit der Oberfläche legt man aber auch Instandhaltungsmöglichkeiten, etwa wie sich eine Oberfläche reinigen lässt, fest.
Edelstahl im Vergleich zu anderen Metallen
Der Werkstoff besticht mit ausgeprägter Korrosionsbeständigkeit, hoher Festigkeit und geringer Längenausdehnung sowie seiner optischen Erscheinung. Edelstahl ist eines der langlebigsten Metalle, da das Material nicht von sich aus rostet, keine Probleme mit Feuchtigkeit bzw. Kondensat und Bitumenkorrosion hat und kein Gewirrgelege notwendig ist, was wiederum Kosten spart. Auch die Ökobilanz ist positiv: Das Material benötigt zu seiner Erzeugung weniger Energie als vergleichbare Werkstoffe, ist recyclebar und hat keinen Metall- bzw. Ionenabtrag, was wertvoll für die Grundwassernutzung ist.
Auch bei der Zugfestigkeit und der Ausdehnung punktet Edelstahl im Vergleich mit anderen Materialien. Durch die hohe Festigkeit kann die Blechstärke auf 0,4/0,5 Millimeter reduziert werden, was Edelstahl im Preisvergleich sehr interessant macht. Durch die geringe Ausdehnung, die besonders im Frühjahr und im Herbst durch die extremen Temperaturschwankungen ein Thema bei anderen Metallen sein kann, werden der Werkstoff selbst und die Unterkonstruktion weniger beansprucht. Die Lärmentwicklung beim Dehnen ist sehr gering, und lange Scharen von bis zu 30 Meter sind möglich. Edelstahl ist durch seine leichte Lötbarkeit auch für den Spengler ideal zum Verarbeiten.
Weil Edelstahl in fast allen Lebensbereichen Verwendung findet, wurde viel daran geforscht, die physikalischen und chemischen Eigenschaften zu verbessern, um den Einsatz in nahezu allen Gebieten von Stadt, Land, Küste, Hochgebirge etc. ohne Qualitätseinbußen zu gewährleisten. Das Ergebnis ist, dass Niederschlag, Kälte und andere Umwelteinflüsse Bauteilen aus Edelstahl wenig anhaben können. Diese Widerstandsfähigkeit prädestiniert das Material für den Außenbereich – unabhängig von klimatischen und Witterungsbedingungen. Darüber hinaus ist nichtrostender Stahl mit anderen Materialien kombinierbar, beständig gegen Zement und Kaltmörtel und bildet keine Korrosion im Kontakt mit zum Beispiel Zink, Kupfer oder anderen Metallen am Bau. Einzige Einschränkung ist die Einwirkung von Fremdrost.
Edelstahl an Dach und Fassade
Weitere Pluspunkte: Edelstahl reflektiert Wärme, verringert das Brandrisiko und leitet Blitze ab. Schon seit 1929 wird Edelstahl in Bauwerken eingesetzt. Anfang der 1990er-Jahre wurde mit dem Chrysler Building (1930) und mit dem Empire State Building (1931) in New York ein Meilenstein bei dessen Einsatz am Dach gelegt.
Der Anspruch an Edelstahl bei der Anwendung an Dach und Fassade ist ein anderer als beim Industriestandard. Die Industrie definiert die Legierung 1.4301 zwar genau, aber die Norm ist so definiert, dass Hersteller möglichst einfach den Zielwert erreichen. Der Unterschied zwischen den Messfaktoren ist oft sehr groß, dabei kann etwa der Unterschied zwischen den Streckgrenzen innerhalb der Norm zwischen 20 und bis zu 35 Prozent liegen. Deshalb haben es sich Hersteller zur Aufgabe gemacht, einen speziellen Edelstahl für die Gebäudehülle zu entwickeln. Dieser ist um bis zu 20 Prozent weicher, um ihn perfekt löten, falzen und profilieren zu können. Für den Spengler, der viel mit der Hand bearbeitet, ist die Weichheit des Materials ausschlaggebend. Durch die einfachere Verarbeitung des weichen Materials spart man Zeit und kann außergewöhnliche Ergebnisse erzielen. Auch das Löten ist für den Verarbeiter ein entscheidendes Kriterium bei der Materialauswahl. Mit dem geeigneten Lötwasser des Herstellers lässt sich Edelstahl hervorragend löten. Auch die entsprechende Oberflächenstruktur (z. B. bürstgewalzt) bietet beste Lötbarkeit. Das Material bietet zudem eine matte Erscheinung von Bauwerken und verringert dadurch die Reflexion.
Vielfältige Oberflächenvarianten
Auch im Bereich Oberflächendesign gibt es für verschiedene Zwecke eine Vielzahl an Oberflächenvarianten. Man unterscheidet grundsätzlich nichtpatinierende und patinierende Oberflächen. Nichtpatinierende Oberflächen verändern sich nicht, es gibt keine Entwicklung des Materials, und es lässt sich leicht reinigen. Patinierende Oberflächen unterliegen einem natürlichen Bewitterungsprozess und sind in ihrer Endfarbgebung wesentlich dunkler als das Ausgangsmaterial.
Oberflächen werden unbehandelt, spiegelnd oder matt, geschliffen, gebürstet, perlgestrahlt, poliert, marmoriert, gebeizt oder mustergewalzt mit verschiedenen Strukturdekoren angeboten. Strukturierte Oberflächen reflektieren Streiflichter wesentlich geringer als glatte oder gar polierte Bleche. Sie sind darüber hinaus unempfindlicher gegenüber Schmutz, Flecken oder Fingerabdrücken. Zuweilen werden Edelstahlbleche mit anderen Metallen beschichtet, etwa verzinnt oder verkupfert. Verzinnte Edelstähle eignen sich unter anderem nicht für den Einsatz im Sockelbereich. Dieser Bereich des Gebäudes ist erhöhten Belastungen, durch z. B. Streusalz, Hunde und Katzen, ausgesetzt und daraus können unschöne Verfärbungen resultieren. Im Sockelbereich ist der Einsatz von 1.4301-Edelstahl oder bei sehr hoher Belastung im industriellen Bereich 1.4404 zu empfehlen.
Auch farbige Oberflächenvarianten mit beeindruckender metallischer Leuchtkraft sind auf dem Markt. In der Regel sind Farben und Oberflächenausführungen kombinierbar. Jede spezifische, funktionelle und ästhetische Anforderung an den Edelstahl kann durch seine Vielfalt in der Oberflächenstruktur erfüllt werden. Um das ideale und gewünschte Endergebnis für den Kunden zu erzielen, ist es unerlässlich, dass der Spengler oder auch der Architekt alle Faktoren des Materials, wie etwa den Bewitterungsprozess und die Einsatzmöglichkeiten, mit dem Kunden vorab bespricht.
Die wichtigsten Auswahlkriterien
Der Ort des Bauwerks spielt bei der Auswahl des geeigneten Materials ebenso eine entscheidende Rolle. Die drei wichtigsten Legierungen für die Gebäudehülle sind 1.4510 mit Chrom als Legierungselement, 1.4301 mit Chrom und Nickel in der Legierung und 1.4404 mit einer Legierungsmischung aus Chrom, Nickel und Molybdän. Beim Einsatz auf dem Land und in der Stadt eignen sich 1.4510 verzinnt und 1.4301. Bei der industriellen Verarbeitung werden die Legierungen 1.4301 und 1.4404 bevorzugt. Bei der Verwendung in Küstennähe ist aufgrund der salzhaltigen Luft darauf zu achten, dass ausschließlich 1.4404-Edelstahl verwendet wird, um Korrosion zu vermeiden. Diese Werte gelten als grobe Richtwerte und sollten im konkreten Fall vom Hersteller bestätigt werden. Mit dem geeignetem Metall am jeweiligen Anwendungsort umgeht man schon im Vorfeld spätere Probleme.
Somit steht fest: Edelstahl ist nicht gleich Edelstahl. Bei Anfragen von Kunden nach Edelstahl, haben diese meist ganz bestimmte Vorstellungen. Daraus und dem Einsatzort entsprechend ergibt sich für Spengler die Anforderung, den Edelstahl des Herstellers mit der geeignetsten Legierung und Oberfläche auszuwählen.