Turbinenschaufeln automatisiert schleifen
Das Fraunhofer Institut für Produktionstechnik (IPT) hat in Zusammenarbeit mit vier Industrieunternehmen den Prototypen einer Roboterzelle zum automatisierten Schleifen von gegossenen Turbinenschaufeln entwickelt.
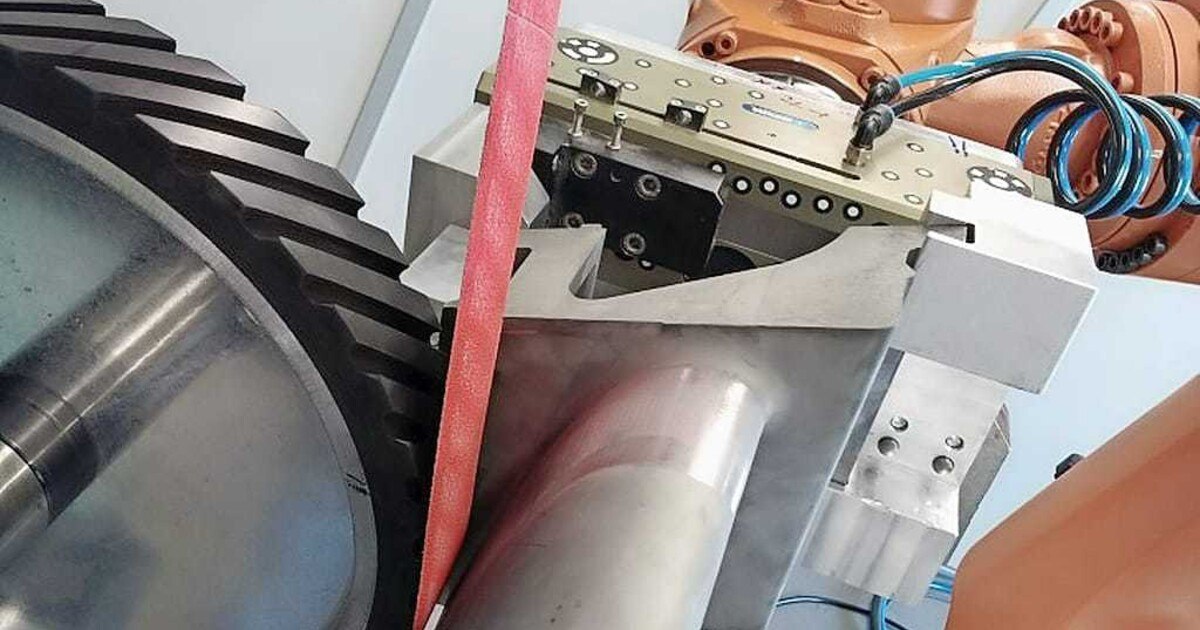
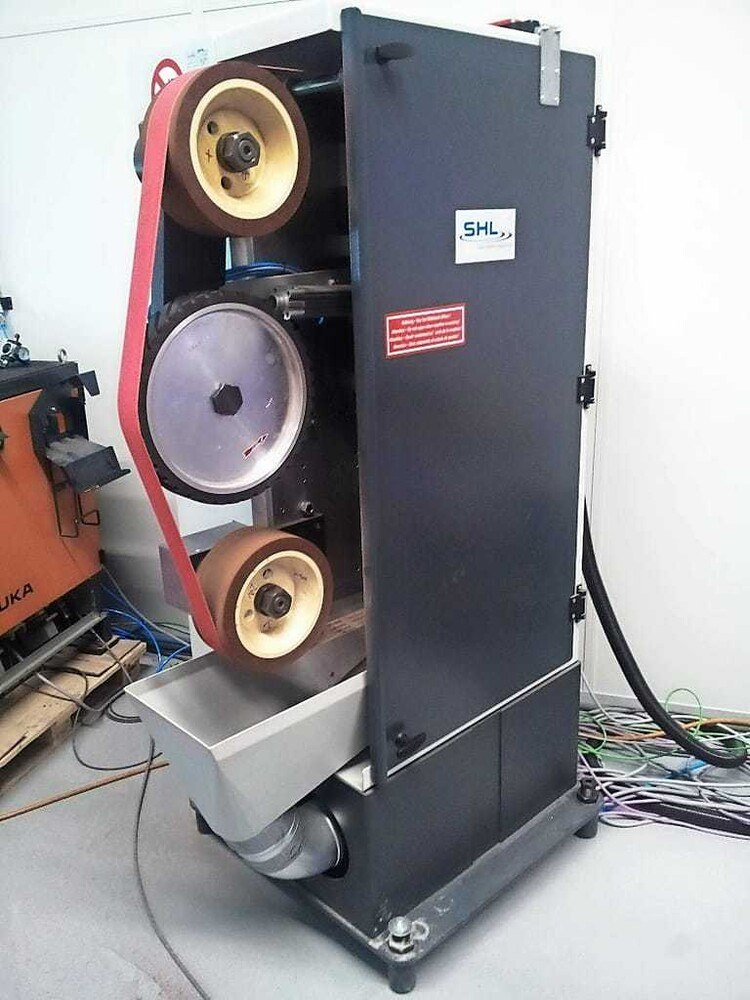
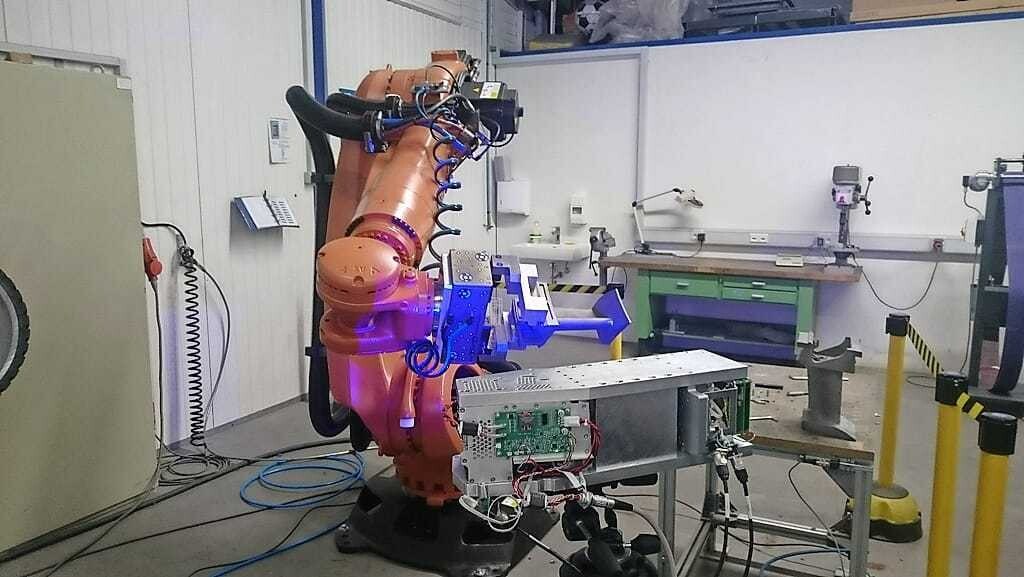
Experten rechnen in den kommenden Jahren mit einer steigenden Nachfrage nach Komponenten wie Turbinen- und Verdichterschaufeln. Vor allem in der Luftfahrtindustrie bestehen nach wie vor die permanenten Herausforderungen in Sachen Gewichtsreduktion und höherer Verbrennungstemperatur. Zum Einsatz kommen neuartige Hochleistungswerkstoffe wie Titanaluminide oder Nickel-Basis Legierungen. Die Komponenten entstehen dabei in einem Gussprozess, und Formabweichungen des Turbinenschaufel-Profils werden bislang manuell korrigiert. Dies ist jedoch äußerst zeitaufwendig, und stabile Verfahren wie das Fräsen kommen werkstoffbedingt nicht in Frage. Zudem entstehen beim Schleifen von hochtemperaturfesten Turbinenschaufeln aus Nickel-Basis Legierungen wie etwa Inconel 738 krebserregende Stäube. Die Entwicklung einer Roboterlösung sollte die Gesundheitsbelastung der Mitarbeiter nachhaltig minimieren. Darüber hinaus galt es, die Wirtschaftlichkeit und Prozessstabilität durch Automatisierung zu verbessern.
Neben der SHL AG und dem Fraunhofer IPT waren die Unternehmen ModuleWorks GmbH aus Aachen, die Doncasters Precision Castings-Bochum GmbH und die Carl Zeiss Optotechnik GmbH aus dem bayerischen Pilsting am Projekt beteiligt. Die Herausforderungen waren dabei klar definiert. Die Komplexität einer adaptiven Bearbeitung erfordert eine schnelle Erfassung der Ist-Geometrie und eine zuverlässige Analyse von Schaufellage und Formabweichungen zur Soll-Geometrie. Zudem galt es, die 6-achsigen Fertigungsbahnen automatisiert zu erstellen. Carl Zeiss Optotechnik steuerte dazu hardware- und softwaretechnische Komponenten für die optische 3D-Messtechnik bei, während ModuleWorks eine CAM-Software zur effizienten Programmierung und anschließenden präzisen, mannlosen Bearbeitung lieferte. Die Eignung des TurboERAS-Systems wurde an Schaufeln aus der Produktion des Endanwenders Doncasters Precision getestet. Das Fraunhofer IPT unterstützte das Konsortium durch die technologisch anspruchsvolle Entwicklung von Schleifprozess- und Korrekturalgorithmen.
Sichere Aufspannung am Roboter
Die Bearbeitung in der Zelle erfolgt werkstückgeführt. Ein Kuka-Industrieroboter bringt das Bauteil zunächst an ein fest installiertes 3D-Messsystem von Carl Zeiss Optotechnik. Anschließend führt er die Schaufel zum Schleifen an die Freiband- und Kontaktrollenschleifmaschine FKS 250/450 der SHL AG. Entstehende Stäube werden sofort abgesaugt, um Verschmutzungen zu vermeiden. Die Robotersteuerung regelt den Schleifprozess über die Stellgrößen Band- und Vorschubgeschwindigkeit sowie Anpressdruck. Das speziell auf die Schaufelgeometrie ausgelegte System ermöglicht eine sichere Aufspannung am Roboterflansch. Bedingt durch vorhandene Formabweichungen an den Spannflächen des gegossenen Bauteils ist dies allerdings nicht reproduzierbar möglich. Die Referenzierung der Schaufel erfolgt daher mit Hilfe der 3D-Messtechnik.
Die Vermessung des Bauteils geschieht mittels Streifenlicht-Projektion. Dabei entstehen dreidimensionale Abbildungen durch Aufnahmen aus mehreren Richtungen. Carl Zeiss Optotechnik entwickelte hierfür eine spezielle Systemkonfiguration. Die Verarbeitung der Messdaten erfolgt in der Software. Hier werden die 3D-Punktewolken der Einzelmessung automatisiert zusammengesetzt und in ein Dreiecksnetz transformiert. Daraufhin kommt es über eine Auswertesoftware zum Vergleich mit dem CAD-Modell der Schaufel. Über farbliche Darstellungen können Abweichungen detailliert visualisiert werden.
Um die geforderte Formgenauigkeit der Turbinenschaufel zu erfüllen, entwickelte ModuleWorks eine auf die adaptive Schleifbearbeitung zugeschnittene CAM-Lösung. Dabei wurde ein Grundgerüst realisiert, mit dem es möglich ist, ausgehend von einer CAD-Datei der Schaufel die passenden Bahnen entlang des Schaufelblatts zu programmieren. Eine wichtige Komponente der CAM-Software ist die Kollisionskontrolle. Diese berücksichtigt die Geometrie der Druckscheibe und des Schleifbandes bereits bei der Bahnplanung. Dabei wird unter anderem sichergestellt, dass der Fuß und das Deckband der Schaufel während des Prozesses nicht mit dem Werkzeug in Berührung kommen.
Zuverlässiger Prozess
Durch die erfolgreiche Zusammenführung der Systembausteine Roboterzelle, CAM-Technologie, 3D-Messtechnik und Prozesstechnologie ist es den Beteiligten des TurboERAS-Projekts gelungen, erstmalig die Voraussetzung für eine robotergestützte, adaptive Schleifbearbeitung von Turbinenschaufeln zu schaffen. Der Prozess ist vom Einspannen des Bauteils über die optische Vermessung bis hin zur Bearbeitung reproduzierbar und sicher. Er ist durch eine adäquate CAM-Bahnplanung sowie durch die Synchronisation mit dem Roboter und der Freiband- und Kontaktrollenschleifmaschine von SHL wirtschaftlich. Die Einzelprozesse können jederzeit in eine automatisierte Anlage übertragen werden. Ein entsprechendes Konzept für die industrielle Anwendung hat die SHL AG bereits entworfen.