Spezialgetriebe ermöglicht Fertigung von vier Millionen Tonnen Stahl-Coils
Kraftübertragung in der Stahlindustrie. Für die Herstellung von Stahl-Coils profitiert ein internationales Stahlwerk vom Know-how der Firmengruppe FCMD.
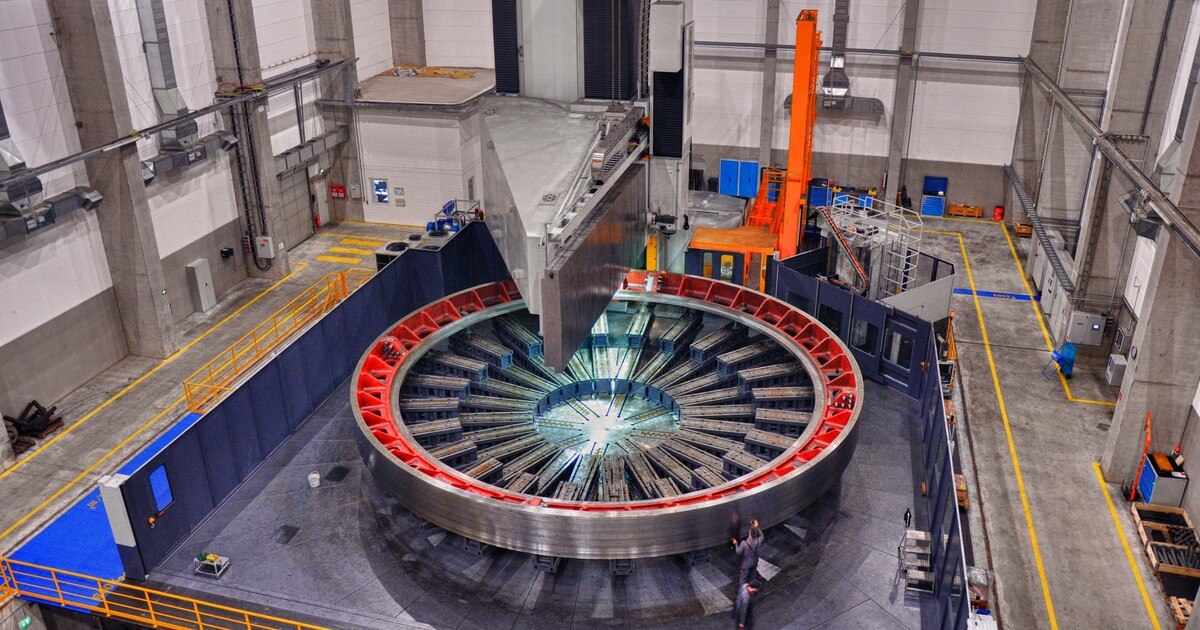
Für die Herstellung von Stahl-Coils in großen Mengen ist eine leistungsstarke Produktionslinie nötig, die sowohl den gewünschten Output als auch die erforderliche Effizienz bietet, um im globalen Wettbewerb der Stahlindustrie bestehen zu können. „Die besondere Herausforderung bei diesem Projekt war natürlich die schiere Größe des Getriebes“, erklärt Michael Hornecker, CEO der FCMD GmbH in Hattingen. „Angefangen bei den Zahnrädern, über das Gehäuse bis zum Transport von einzelnen Bauteilen mussten verschiedenste Aspekte bedacht werden.“ Die Planungen begannen im Jahr 2017, direkt nachdem das Sondergetriebe bestellt worden war. Geleitet wurde das Projekt von der französischen Seite der Groupe CIF, zu der auch FCMD gehört. Innerhalb eines Jahres konnten sämtliche Produktionsschritte, von der Konstruktion über die Fertigung der Einzelkomponenten und die Montage bis zur Lieferung und Inbetriebnahme abgeschlossen werden.
Extreme Hitze und Luftfeuchtigkeit
„Das Getriebe sollte auf einer Warmbreitbandstraße eingesetzt werden, die unter anderem aus fünf Vorwalz- und sechs Fertigwalzwerken besteht“, erläutert Hornecker. „Stahl-Brammen werden hier ausgewalzt und später zu Coils aufgewickelt.“ Die Überlegungen beim Engineering des Getriebes betrafen nun vor allem die Umgebungsbedingungen im Stahlwerk. Denn bevor das Material gewalzt werden kann, müssen die Brammen auf eine Temperatur von etwa 1250 ˚C erhitzt werden, um die für das Walzen nötige Kraft zu verringern und die Verformbarkeit zu erhöhen. Die vorherrschende Temperatur erfordert, dass sämtliche Maschinen und Bauteile der näheren Umgebung hitzebeständig sind. Gleichzeitig muss dem beständigen Auftreten von Schlacke auf der Oberfläche der Brammen in Form von oxidiertem Kohlenstoff mit wiederholter Reinigung durch Wasserstrahlanlagen begegnet werden. Der hierbei entstehende Wasserdampf sorgt für extreme Luftfeuchtigkeit, was wiederum das Material der Maschinen angreifen kann. „Daher fertigen wir unsere Getriebe aus korrosions- und hitzebeständigen Materialien“, erklärt Hornecker. „So ist die Maschine sowohl gegen Hitze als auch gegen Korrosion geschützt.“
190 Tonnen schweres Getriebe
Ein weiterer entscheidender Faktor im Walzwerk war die benötigte Leistung. „Auf dem Warmbreitband werden die Brammen mehrfach ausgewalzt, um die gewünschte Dicke zu erreichen“, so Hornecker. Hierbei wird zwischen den Walzen der Vorstraße, wo der Stahl reversierend gewalzt wird, und denen der Fertigstraße unterschieden. Insgesamt kommen elf Walzen zum Einsatz, die für eine Produktion von 4 Mio. t Stahl-Coils pro Jahr ausgelegt sind. Das Getriebe musste somit eine hohe Leistungsdichte aufweisen, um genug Kraft auf begrenztem Raum übertragen zu können. „Durch die Größe der eingesetzten Zahnräder sowie dank einer optimalen Kraftumsetzung in diesem 190 t schweren Getriebe, mit einer Länge von fast neun Metern und einer Höhe von fast fünf Metern, konnte eine Leistung von 9 MW erreicht werden. Auf diese Weise ist es möglich, sämtliche Walzwerke parallel zu betreiben“, berichtet Hornecker.
Doch auch der Wechsel zwischen den Betriebszuständen war aufgrund der permanenten und starken Beanspruchung eine Herausforderung: „Das Getriebe musste sieben Tage die Woche rund um die Uhr einsatzfähig sein – und das einerseits bei ununterbrochenem Betrieb mit nichtperiodischen Last- und Drehzahländerungen und andererseits bei periodischem Aussetzbetrieb, der auch Anlauf- und Bremsvorgänge des Getriebes beinhaltet“, erklärt Hornecker. „Dies stellte eine große mechanische und elektrische Belastung für das Aggregat dar, die wir beim Engineering berücksichtigen mussten.“
Fünf verschiedene Unternehmen steuern Expertise bei
Die Fertigung wurde dabei in Kooperation mehrerer Firmen innerhalb der Groupe CIF durchgeführt. Die meisten Arbeitsschritte fanden jedoch unter Leitung der in Cambrai ansässigen CMD Gears statt, wie zum Beispiel die finale Montage der einzelnen Teile vor Ort. „Vor Abschluss des Auftrags bestand noch eine letzte Herausforderung im Transport des extrem schweren Aggregats über 930 km zum Stahlwerk im Süden Frankreichs“, erklärt Hornecker. „Dafür musste das Getriebe in sechs Sendungseinheiten unterteilt werden, die selbst einzeln noch bis zu 60 Tonnen wogen. Gemeinsam mit Ferry-Capitain und CMD bewerkstelligten wir auch dies, sodass bereits 2018 die Sonderanfertigung in Betrieb genommen werden konnte.“ Ein zweites Getriebe, das noch im selben Jahr bestellt wurde, konnte 2019 geliefert werden und wartet noch auf seinen Einsatz.