Flügel aus Stahl haben Recyclingpotenzial
Bei Rotorblättern von kleineren Windkraftanlagen hat der Werkstoff Metall durchaus Chancen gegenüber faserverstärktem Kunststoff. Der Grund liegt in den Möglichkeiten der Wiederverwertung am Ende des Lebenszyklus.
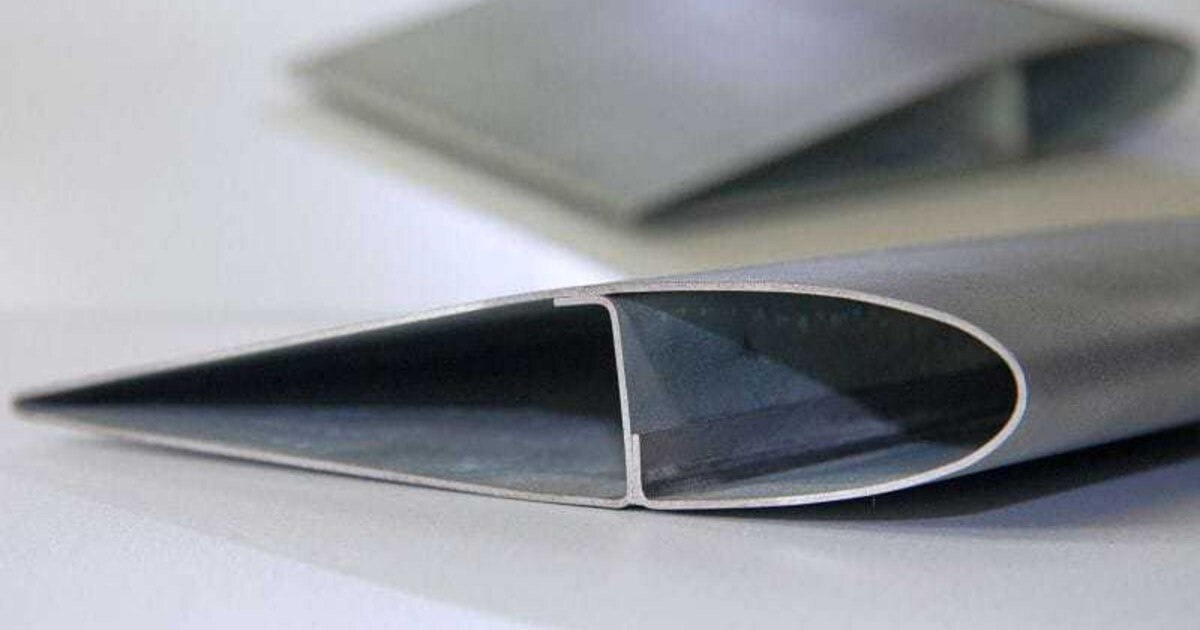
Windräder liefern umweltfreundlichen Strom. Die bei sehr großen Rotorblättern oft verwendeten, faserverstärkten Kunststoffe lassen sich kaum wiederverwerten. Anders bei Blättern aus Stahl: Ihre Recyclingquote liegt werkstoffbedingt bei über 90 Prozent. Zudem sind sie deutlich kostengünstiger als ihre Gegenstücke aus Kunststoff.
Der überwiegende Teil großer Rotorblätter besteht gewichtsbedingt aus faserverstärkten Kunststoffen. Diese Materialien lassen sich derzeit noch kaum recyceln, die Wiederverwertung ist sehr aufwändig. Forscher des Fraunhofer-Instituts für Werkzeugmaschinen und Umformtechnik IWU in Chemnitz setzen daher auf Metall als Flügelmaterial, insbesondere auf Stahl für kleinere Anlagen. Das höhere Gewicht von Stahlflügeln ist hier noch nicht relevant und kann bei wachsenden Anlagengrößen durch den Einsatz von Leichtmetallen kompensiert werden. Im Projekt „HyBlade“ entwickeln die Forscher die entsprechende Aerodynamik sowie die Prozessketten für die Fertigung. Flügel aus Stahl herzustellen, bietet zahlreiche Vorteile: „Zum einen werden die Windräder deutlich ökologischer, denn Stahl kann zu mehr als 90 Prozent recycelt werden. Mit Metallrotorblättern wird Windkraft daher wirklich umweltfreundlich“, konkretisiert Marco Pröhl, Wissenschaftler am IWU. Außerdem sinke der Preis für die Rotorblätter in der Serienfertigung um bis zu 90 Prozent, verglichen mit solchen aus faserverstärktem Kunststoff. „Und die Flügel lassen sich genauer fertigen“, so Pröhl.
Außerdem sind sie schneller produziert: Parallelisiert man den Prozess – wird also sofort ein neues Blech in die Fertigungslinie eingeschoben, wenn ein Flügel den ersten Fertigungsschritt hinter sich hat – fällt etwa alle 30 Sekunden ein fertiges Rotorblatt vom Band. Bei faserverstärkten Kunststoffen dauert dieser Vorgang dagegen meist mehrere Stunden. Denn bei Flügeln aus faserverstärkten Kunststoffen ist oftmals viel Handarbeit notwendig: Zunächst muss eine passende Form für die Flügel hergestellt werden. Je nach Fertigungsvariante legen die Arbeiter Fasermatten in diese Form, injizieren Harz und härten das Teil für mehrere Stunden im Ofen aus. Sie erhalten so zwei Halbschalen, deren Ränder sie zunächst beschneiden und die sie anschließend aufeinander kleben. Diese Schritte lassen sich zwar auch wie in der Blechteilfertigung zeitgleich durchführen – das ändert jedoch nichts an ihrem hohen Zeitbedarf. Man bräuchte Dutzende gleichzeitig laufende Anlagen, wollte man die Flügel ebenso schnell fertigen wie jene aus Metall.
Serienfähig
Die Herstellung von Metallrotoren hingegen lässt sich gut automatisieren, denn die Prozesse entsprechen denen der Automobilindustrie. Sie eignet sich daher für die Serienfertigung. Ausgangsmaterial ist ein flaches Stahlblech. Dieses kanten die Forscher mit einem Biegestempel ab, sodass es bereits die typische Flügelform erhält. Die Ränder verschweißen sie mit einem Laser – ein geschlossenes Profil entsteht. Diese Vorform legen die Wissenschaftler in ein Werkzeug mit der späteren Endform, pumpen ein wiederverwendbares Wasser-Öl-Gemisch ins Innere des Flügels und setzen ihn unter einen Druck von bis zu mehreren Tausend bar. Der Flügel wird dadurch quasi aufgeblasen und erhält so seine endgültige Form. „Die Flügel geben das ins Werkzeug gefräste Strömungsprofil auf 0,1 Millimeter genau wieder“, erläutert Pröhl.
Einen Flügel mit 15 Zentimetern Breite und 30 Zentimetern Länge haben die Forscher bereits hergestellt. An ihm optimierten sie die einzelnen Herstellungsschritte. In einem weiteren Schritt produzieren sie nun einen kompletten Rotor für eine Vertikalachs-Windkraftanlage mit 2,8 Metern Flügellänge und zwei Metern Durchmesser. An der belgischen Küste soll dieser dann zeigen, was er kann: auf einem Testfeld für kleine Windkraftanlagen. [red/iwu]